J_Appl_Mater_Eng 2021, 60(2–3), 81-89; doi:10.35995/jame60020007
Effect of Pouring Temperature and Heating of Ceramic Shells Mould on Projection of Thin Wall Castings
1
Łukasiewicz Research Network—Krakow Institute of Technology, Zakopiańska 73 Str., 30-418 Krakow, Poland; waclaw.oleksy@kit.lukasiewicz.gov.pl
2
Specodlew Sp. z o.o., Rotmistrza Witolda Pileckiego 3 Str., 32-050 Skawina, Poland; wojciech.maj@specodlew.com.pl (W.M.); piotr.tkaczewski@specodlew.com.pl (P.T.); wladyslaw.madej@specodlew.com.pl (Wł.M.); piotr.garbien@specodlew.com.pl (P.G.); artur.dydak@specodlew.com.pl (A.D.)
3
Institute of Metallurgy and Materials Science, Polish Academy of Sciences, Reymonta 25 Street, 30-059 Krakow, Poland; l.rogal@imim.pl (Ł.R.); w.maziarz@imim.pl (W.Ma.)
*
Corresponding author: zdzislaw.zolkiewicz@kit.lukasiewicz.gov.pl
How to cite: Żółkiewicz, Z.; Rogal, Ł.; Maj, W.; Maziarz, W.; Tkaczewski, P.; Madej, W.; Garbień, P.; Dydak, A.; Oleksy, W. Effect of Pouring Temperature and Heating of Ceramic Shells Mould on Projection of Thin Wall Castings. J. Appl. Mater. Eng. 2020, 60(2–3), 81–89, doi:10.35995/jame60020007.
Received: 19 January 2021 / Accepted: 18 February 2021 / Published: 23 February 2021
Abstract
:One of the research directions of this study is to determine the possibility of making precise, thin-walled castings from selected iron alloys. The scope of research work is aimed at determining the applicability of the casting process of selected iron alloys with the technology of wax pattern, for making precise castings with a wall thickness of less than 3 mm. The article presents the results of tests carried out for experimental castings with the shape of steps, characterized by different wall thicknesses: 1 mm, 5 mm, 10 mm, 25 mm. The castings were made of LH14, Gs42crMo4, L35H7MP2, LH26N9, 316L cast steel, and a new alloy marked “0”. The metal was smelted in an induction furnace with a capacity of 150 kg. The technology of ceramic shell mould used in the plant was used to make the experimental castings. Ceramic shell moulds were heated in a chamber furnace at a fixed temperature. The time of annealing the ceramic mould was constant in a ceramic form. The following parameters were variable during the tests: iron alloy, pouring temperature, and annealing temperature of the ceramic shell mould.
Keywords:
iron alloy; ceramic shell mould; wall thickness1. Introduction
Foundry technologies that use wax models to make precise ceramic shell moulds are characterized by many advantages, primarily technological, economic and ecological. They make it possible to obtain thin-walled, precise castings from ferrous and non-ferrous alloys. They are haracterized by good shape reproducibility, dimensional repeatability, surface quality, and the possibility of obtaining external and internal shapes without the use of machining (Stachańczyk 1995; Czekaj et al. 2012; Karwiński 1997; Karwiński et al. 2006; Tomasik et al. 2010). The limitation is the wall thickness of the casting. Usually, obtaining a good quality cast with a wall thickness with a large area of less than 3 mm is associated with great problems.
At PIO Specodlew, research was carried out on the use of the innovative material of the wax model developed as part of the project, the composition and method of making a ceramic mould, the chemical composition of an iron alloy with an innovative technology of cast steel smelting to be made of an iron alloy, thin-walled castings of various shapes, wall thickness below 3 mm. Iron alloy castings must meet the requirement of high dimensional accuracy, surface quality, reproducibility of assumed shapes, and assumed mechanical properties.
When starting the tests, the chemical composition of the cast steel, method of smelting, tapping and pouring temperature, time, and annealing temperature of the ceramic mould were assumed. The method of making ceramic moulds, and the annealing time during the trials and tests, were constant.
The scope of the research included the execution of a series of thin-walled melts with the use of selected cast steel grades LH14, Gs42crMo4, L35H7MP2, LH26N19, 316L, “0” (Kniaginin 1977; Bydałek and Mutwil 1997; Stachańczyk et al. 1995) poured into a ceramic shell mould (Figure 2) (Żółkiewicz et al. 2018, 2019, 2020). The shape of the experimental casting was adopted for the tests—a step with a wall thickness of 1 mm, 5 mm, 10 mm, and 25 mm; the dimension of the step with the minimum thickness of 30 × 30 × 1 mm (Figure 1) (Technological tests of cast steel—Castability test BN-66/4051-12). The process of making a cast in a ceramic mould was simulated (Figure 3). The degree of mapping of the casting wall of the tested alloy was analysed depending on the pouring temperature and the annealing temperature of the ceramic shell mould. The dimensions of the tested step are 30 × 30 × 1 mm. The results showing the degree of mapping the shape of the casting with a thickness of 1 mm are presented in Figure 5, Figure 6, Figure 7, Figure 8 and Figure 9 (Żółkiewicz et al. 2018, 2019, 2020). The occurrence of possible shape, surface, external and internal defects and the method of their elimination were analysed.
2. Materials and Methods
The aim of the research was to determine the effect of the pouring temperature of selected iron alloys, the annealing temperature of the ceramic shell mould on the mapping of the shape of the casting with dimensions of 30 × 30 mm and thickness of 1 mm. The tests were carried out with the use of the shape of a stepped casting with a wall thickness of 1 mm, 5 mm, 10 mm, 25 mm (Figure 1, Technological tests of cast steel—Castability test BN-66/4051-12).
The obtained test results were analysed (Table 1); curve, solidus and liquidus temperatures for a given chemical composition of the alloy, the lowest allowable metal tapping temperature and pouring temperature were determined (Żółkiewicz et al. 2018, 2019, 2020). The method of smelting an experimental iron alloy, the order of adding individual batch materials, technical and technological parameters of smelting was developed. These data were compared with the parameters used to simulate the pouring, freezing and cooling processes in the SolidCast software.
The made wax experimental pattern of the steps was used to make sets of ceramic shell mould, which, after drying and heating, were poured with liquid metal, cast steel: successively LH14, Gs42crMo4, L35H7MP2, LH26N19, 316L, “0” (Figure 2) (Żółkiewicz et al. 2018, 2019, 2020). These castings, after manual separation of the ceramic shell mould from the casting, after the process of cleaning the casting surface (shot blasting, sandblasting), were submitted for further tests (surface quality assessment, the degree of reproduction of the casting wall with a thickness of 1 mm). The test results are presented in the following figures. Wax pattern made of wax used according to the PIO Specodlew recipe were adopted for the tests. The chemical composition of the metal was checked before pouring the metal into the mould. After pouring the ceramic shell mould with metal, the temperature of the mould surface was measured using a thermal imaging camera (Żółkiewicz et al. 2018, 2019, 2020). At the same time, the solidification curve of the tested alloy was determined with the help of a Pt Pt Rh thermocouple installed in the mould.
The metal was poured into ceramic shell mould (Figure 2) with a repetitive composition and method of implementation. A wax pattern with a repeatable composition and method of production was used to make a ceramic shell mould. The pouring temperature, heating of the ceramic shell mould and alloy composition were changed. The location of the model, formed during trials and tests, would be repeatable. The baking time for the ceramic shell mould was constant.
During the tests, the coagulation curve of the selected iron alloy and the temperature distribution of the ceramic shell mould during pouring, solidification and cooling were examined.
3. Results and Discussion
At the beginning of the study, the process of flooding, solidification and cooling was simulated (Garbień et al. 2018). The US license was used for the simulation of flooding and solidification. In the absence of the tested iron alloy in the material database, cooperation with the licensor of the program enables the extension of this database with new casting alloys. Such studies were conducted. This made it possible to determine the liquidus and solidus lines and the pouring temperature for the tested cast steel.
By entering the tests, a simulation of the pouring, solidification and cooling process was carried out. An exemplary simulation of casting pouring a step with a small alloy 0 is shown in Figure 3 (Garbień et al. 2018). The simulations were carried out using a database and the SolidCast program. The simulations were carried out for the assumed parameters:
- Type of ceramic shell mould material: quartz sand
- Ceramic shell mould thickness: ~8 mm
- Mould cavity temperature just before pouring:
- ○
- 975 ℃
- ○
- Type of foundry alloy: alloy “0”
- ○
- Metal temperature in the furnace before flooding—drain: 1639 ℃, 1556 ℃, 1505 ℃.
- ○
- Temperature of the metal cast into the ceramic shell mould: 1580 ℃, 1516 ℃, 1475 ℃.
- ○
- Prime time: 15 s.
- ○
- Cooling the flooded ceramic shell mould set—chamber furnace with a constant temperature of approx. 5 h.
Parameters obtained during the simulation were checked in experimental conditions.
Made of selected iron alloys at the assumed pouring temperature, heating of the ceramic shell mould, a series of experimental castings and evaluated the shape and method of reconstitution of a step sample with a wall thickness of 1 mm (Table 1 and Table 2).
The temperature range for soaking the ceramic shell mould was variable and ranged from 850 °C to 1060 °C. The pouring temperature was related to the composition of the alloy tested and contained at least three temperatures: the highest, lowest and middle.
Selected test results are shown in Figure 4, Figure 5, Figure 6, Figure 7, Figure 8 and Figure 9 (Żółkiewicz et al. 2018; 2019).
The result of the research was to determine the possibility of recreating the shape of a casting with dimensions of 30 × 30 mm and a wall thickness of 1 mm. The experimental tests were carried out on a step-shaped casting with a specific shape and wall thickness from 1 to 50 mm. The metal was poured into ceramic shell moulds annealed at the temperature specified during the tests. Castings were made of alloys selected for testing; LH14, Gs42crMo4, L35H7MP2, LH26N19, 316L, “0”.
The conducted analysis of the degree of mapping the wall of the experimental casting, the step with the assumed technological parameters of cast steel melting and the parameters of pouring, heating the mould showed (Żółkiewicz et al. 2018, 2019, 2020):
- a complete representation of the casting wall made of the tested alloys with a thickness of 5 mm, 10 mm, 25 mm and 50 mm was obtained.
- obtaining a complete reproduction of the wall of the casting made of the tested alloys with a thickness of 1 mm depends on the type of alloy poured into the ceramic shell mould and the parameters of the technological process.
- a 100% reconstruction of the wall of a 1 mm-thick cast, poured with an LH14 alloy was obtained at the tested temperature of heating the ceramic shell mould (Figure 5) in one trial.
- a 100% wall reconstruction of a 1 mm-thick cast with a Gs42CrMo4 alloy was obtained at the highest annealing temperature of the ceramic shell mould (Figure 6).
- a 100% reconstruction of the wall was obtained of a 1 mm-thick cast with an L35H7MP2 alloy at the temperature of heating the ceramic mould above 980 °C (Figure 6).
- a 100% reconstruction of the wall was obtained of a 1 mm-thick cast with an LH26N19 alloy, regardless of the temperature of annealing the ceramic shell mould (Figure 7).
- a full reconstruction of the wall of a 1 mm-thick cast, cast with alloy 0 and 316L cast steel for a ceramic shell mould was obtained, dependent on the pouring temperature.
The analysis of the obtained test results shows the possibility of making a casting with dimensions of 30 × 30 × 1 mm. It is suggested to extend the scope of tests to include castings of other, variable shapes and wall thicknesses, made not only of the tested cast steel.
4. Conclusions
The analysis of the test results on the example of a step casting made of the tested iron alloys (LH14, Gs42crMo4, L35H7MP2, LH26N19, 316L, “0”), in a ceramic shell mould, showed that it is possible to recreate the shape of a casting with dimensions of 30 × 30 mm and a wall thickness of 1 mm.
With the assumed technological parameters of the technological process, a complete representation of the cast wall of a step with a wall thickness of over 5 mm was obtained, and an incomplete representation of a step cast with a wall thickness of 1 mm (Figure 4, Figure 5, Figure 6, Figure 7, Figure 8 and Figure 9). In the conducted tests, between 5% and 100% of the discussed wall thickness of the casting was achieved.
In real conditions, the shape of the casting is variable and has a different wall thickness.
It is proposed to extend the tests to iron alloy castings with variable wall thickness (Żółkiewicz et al. 2018, 2019, 2020).
Author Contributions
Conceptualization, Z.Ż., Ł.R., W.M.; Methodology, W.M., Z.Ż., Ł.R., W.Ma.; Software, W.Ma., P.G., A.D.; Validation, Wł.M., W.Ma.; Formal Analysis, W.M.; Investigation, W.Ma.; Resources, Wł.M.; Data Curation, Z.Ż.; Writing—Original Draft Preparation, W.Ma., A.D., P.G., Z.Ż.; Writing—Review and Editing, Z.Ż., Ł.R., P.G.; Visualization, Z.Ż., Ł.R., P.G., W.O.; Supervision, W.M., W.O., Z.Ż.; Project Administration, W.M., Z.Ż.; Funding Acquisition, W.M.
Funding
The research was carried out as part of a fast track funded by the National Center for Research and Development, Intelligent Development Operational Program (SG OP) for the years 2014–2020, project no. POIR.01.01.01-00-0197/17-00, contract no. POIR.01.01.01-00-0197/17.
Acknowledgments
The article presents the results of the research work carried out at PIO Specodlew Sp z o.o., entitled “Development and implementation of an innovative technology of casting thin-walled products made of Fe-based materials dedicated to the armaments and automotive industries, characterized by high dimensional accuracy and increased strength”.
Conflicts of Interest
The authors declare no conflict of interest.
References
- Badania technologiczne staliwa — Próba lejności BN-66/4051-12 (Technological Tests of Cast Steel—Castability test BN-66/4051-12). (In Polish)
- Bydałek, A.; Mutwil, J. Solidification of Metals and Alloys 1997, 31.
- Czekaj, E.; Karwiński, A.; Pączek, Z.; Pysz, S. A new method of producing precision castings made of copper alloy in the moulds of ceramic. Archives of Foundry Engineering 2012, 12, 9–16. (In Polish) [Google Scholar]
- Garbień, P.; Maziarz, W.; Żółkiewicz, Z.; Rogal, Ł.; Maj, W.; Nawrocki, J.; Madej, W.; Oleksy, W. Sprawozdanie z przeprowadzonej symulacji procesu zalewania i krzepnięcia płytki schodkowej małej wykonanej ze stopu 0; PIO Specodlew sp. z o.o.: Skawina, 2018; (Un-published, in Polish). [Google Scholar]
- Karwiński, A. Wpływ za wartości krzemionki koloidalnej na właściwości ciekłej masy ceramicznej stosowanej w technologii wytapianych modeli. Solidification of Metals and Alloys 1997, 31, 89–96. [Google Scholar]
- Karwiński, A.; Wieliczko, P.; Leśniewski, W. Zastosowanie środków powierzchniowo czynnych w procesach odlewania precyzyjnego. Inżynieria i Aparatura Chemiczna 5, 58–60. (In Polish)
- Kniaginin, G. Staliwo. Metalurgia i odlewnictwo; Wydawnictwo “Śląsk”: Katowice, 1977. (In Polish) [Google Scholar]
- Stachańczyk, J. Materiały stosowane w procesie wytwarzania wysokiej jakości odlewów precyzyjnych. Paper Presented at Sympozjum “Najnowsze rozwiązania technologiczne i materiałowe w procesie wytwarzania odlewów precyzyjnych”, Kraków, Poland; Instytut Odlewnictwa, 1995. (In Polish). [Google Scholar]
- Stachańczyk, J.; Gwiżdż, A.; Pirowski, Z. Opracowanie technologii odlewania wysokiej jakości odlewów precyzyjnych ze staliwa l LOH22N5M3-N2 z dodatkiem azotu. Krzepniecie Metali i Stopów 1995, 24, 101–06. (In Polish) [Google Scholar]
- Tomasik, J.; Haratym, R.; Kłębczyk, M. Jakość odlewów w procesie wytapianych modeli oraz Replicast CS w aspekcie ekologii. Archives of Foundry 2010, 10, 151–55. (In Polish) [Google Scholar]
- Żółkiewicz, Z.; Maj, W.; Maziarz, W.; Rogal, Ł; Madej, W.; Garbień, P.; Oleksy, W. Sprawozdania i raporty z realizacji projektu; PIO Specodlew Sp. z o.o.: Skawina, 2018; (Un-published, in Polish). [Google Scholar]
- Żółkiewicz, Z.; Maj, W.; Maziarz, W.; Rogal, Ł; Madej, W.; Garbień, P.; Oleksy, W. Sprawozdania i raporty z realizacji projektu; PIO Specodlew Sp. z o.o.: Skawina, 2019; (Un-published, in Polish). [Google Scholar]
- Żółkiewicz, Z.; Maj, W.; Maziarz, W.; Rogal, Ł; Madej, W.; Garbień, P.; Oleksy, W. Sprawozdania i raporty z realizacji projektu; PIO Specodlew Sp. z o.o.: Skawina, 2020; (Un-published, in Polish). [Google Scholar]
Figure 1.
Stair wax pattern
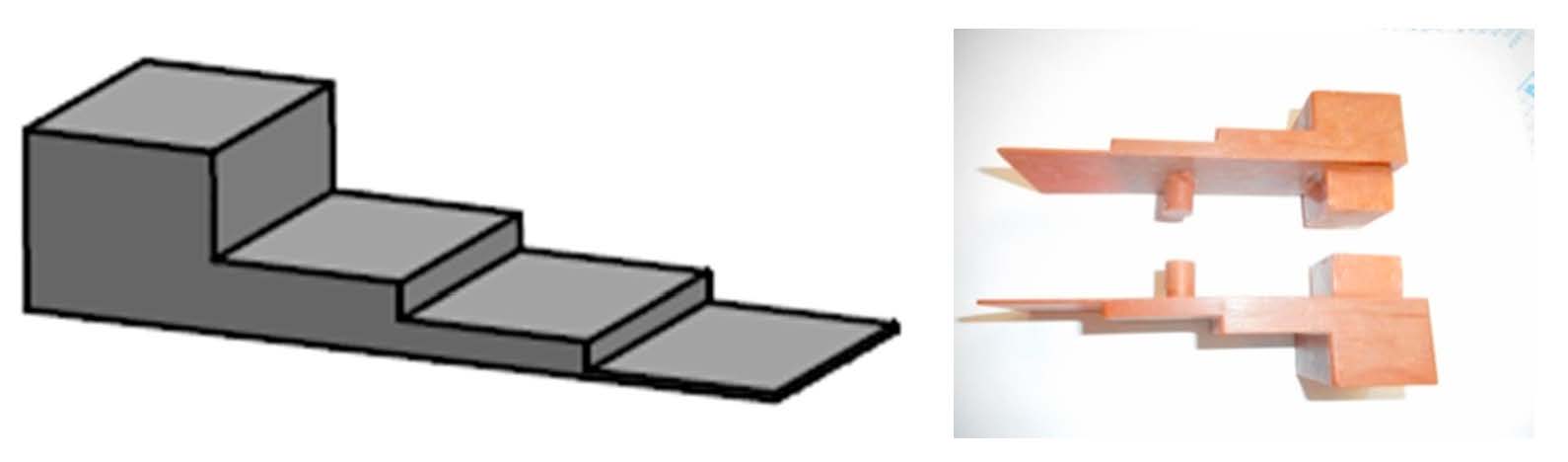
Figure 2.
Ceramic shell mould (Żółkiewicz et al. 2018; Żółkiewicz et al. 2019)
Figure 2.
Ceramic shell mould (Żółkiewicz et al. 2018; Żółkiewicz et al. 2019)
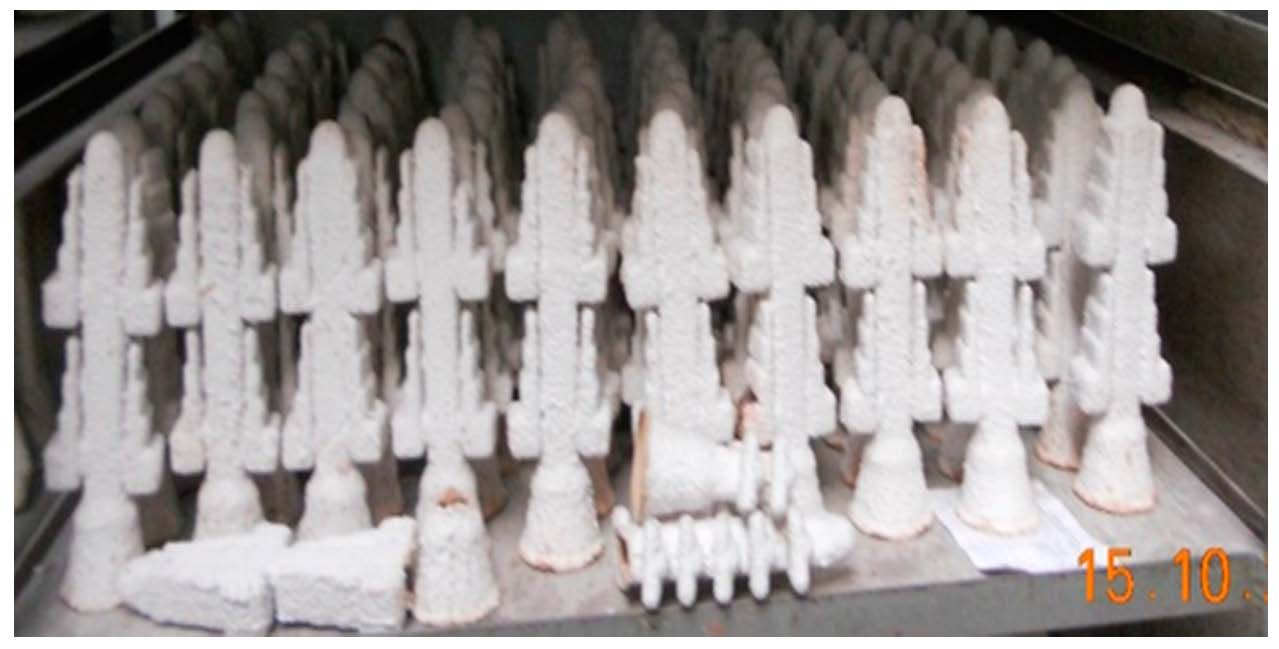
Figure 3.
Simulation of the casting process and solidification of the casting small step (Garbień et al. 2018)
Figure 3.
Simulation of the casting process and solidification of the casting small step (Garbień et al. 2018)
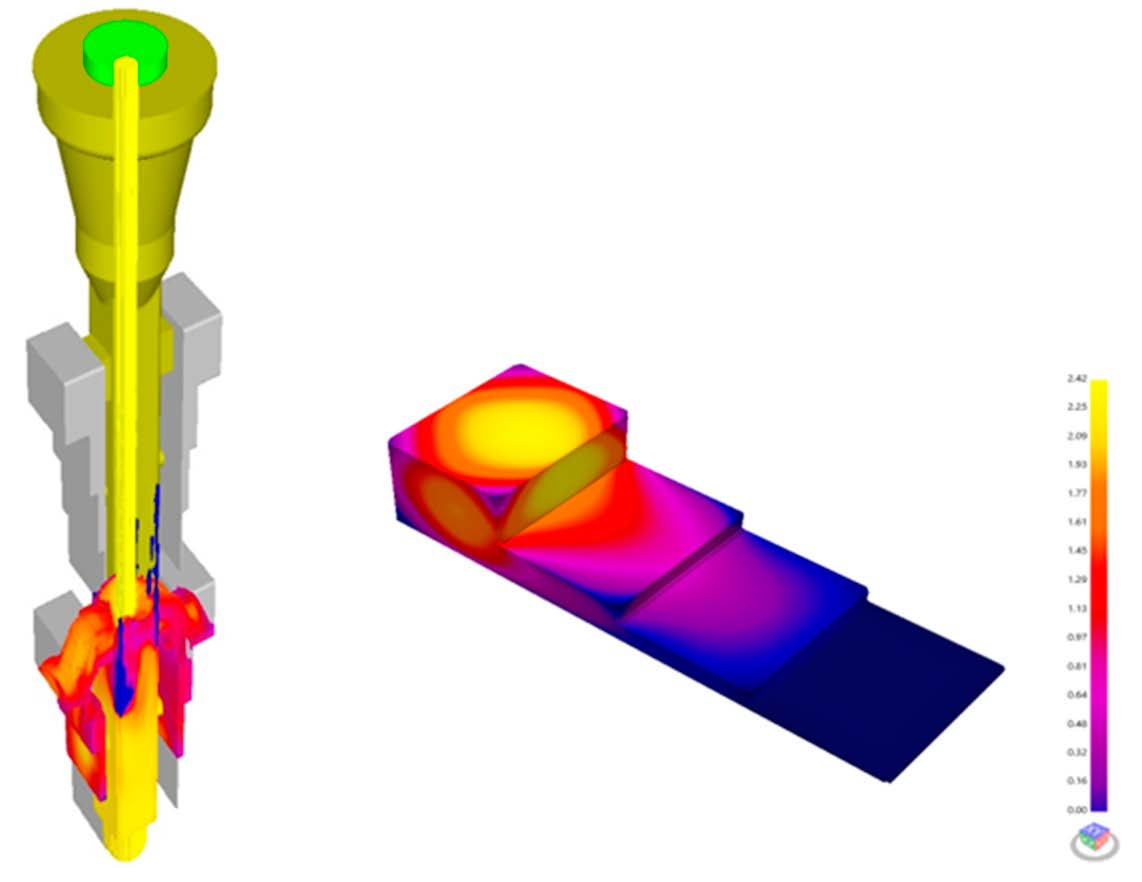
Figure 4.
Dependence of the mapping level of the 1 mm thick casting wall on the temperature of the ceramic shell mould, LH14 cast steel (Żółkiewicz et al. 2018; 2019)
Figure 4.
Dependence of the mapping level of the 1 mm thick casting wall on the temperature of the ceramic shell mould, LH14 cast steel (Żółkiewicz et al. 2018; 2019)
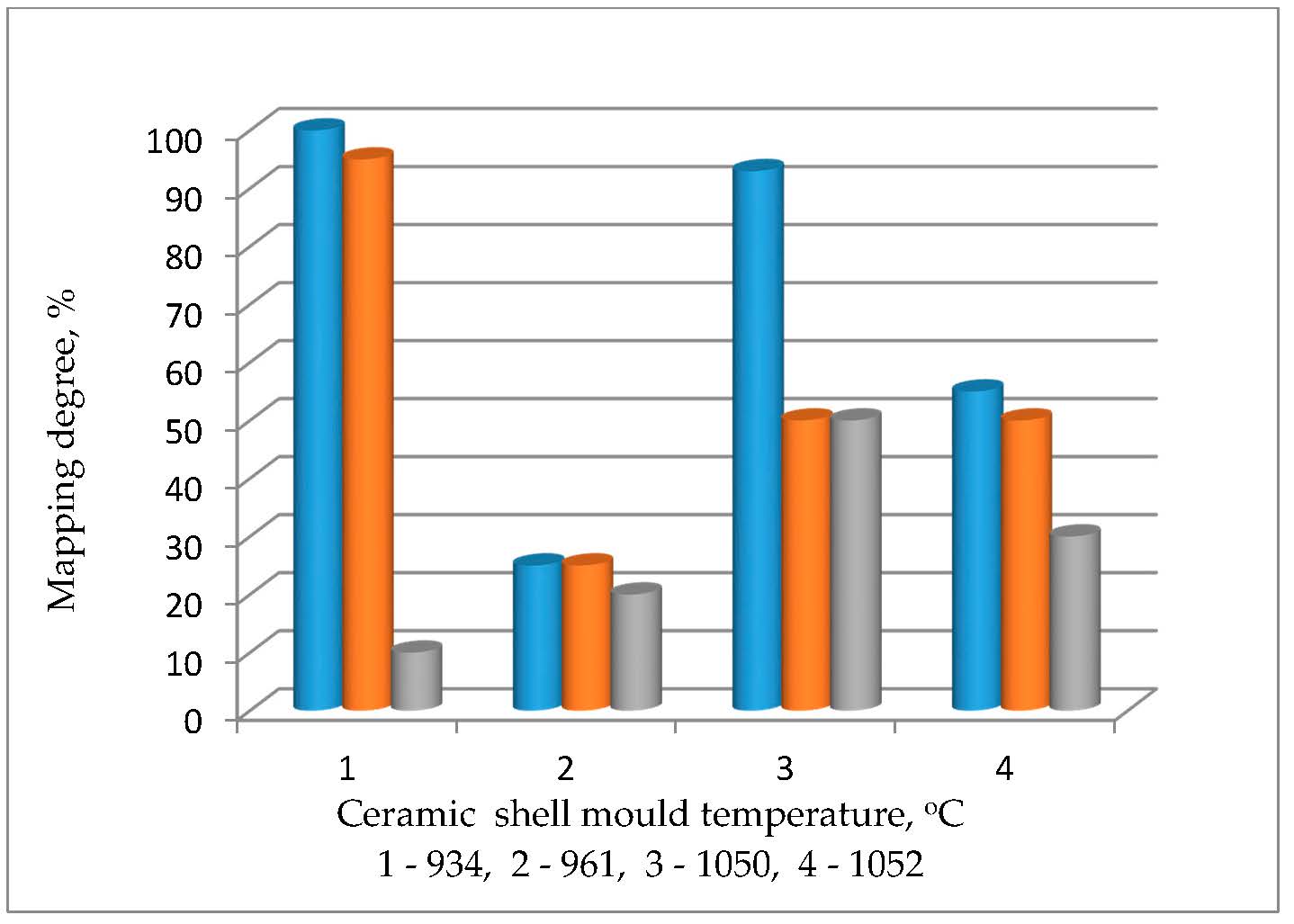
Figure 5.
Dependence of the mapping level of the 1 mm thick casting wall on the temperature of the ceramic shell mould, Gs42crMo4 cast steel (Żółkiewicz et al. 2018; 2019)
Figure 5.
Dependence of the mapping level of the 1 mm thick casting wall on the temperature of the ceramic shell mould, Gs42crMo4 cast steel (Żółkiewicz et al. 2018; 2019)
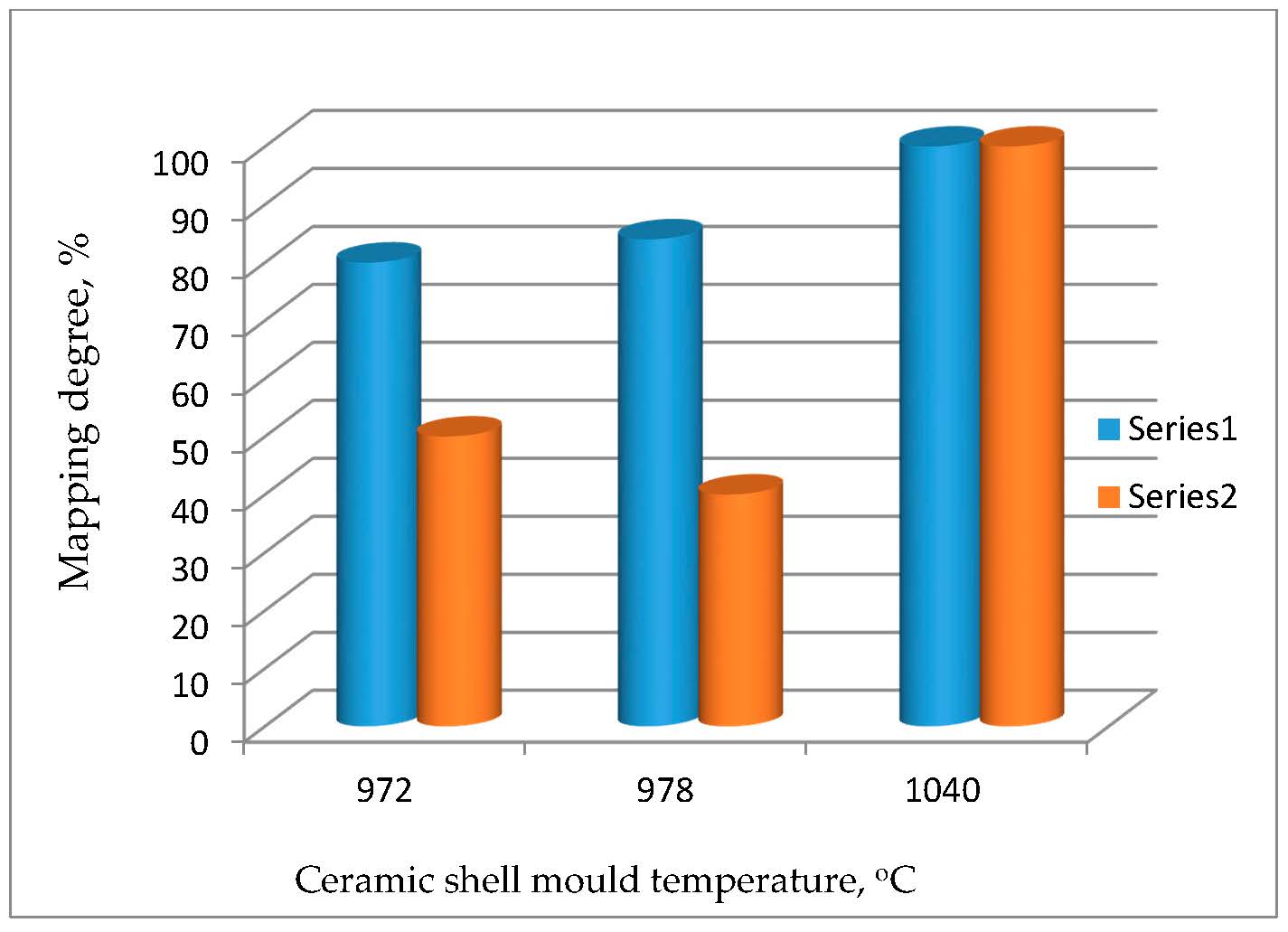
Figure 6.
Degree of mapping the wall shape 1 mm thick from the temperature of the ceramic shell mould, alloy L35H7MP2 (Żółkiewicz et al. 2018; 2019)
Figure 6.
Degree of mapping the wall shape 1 mm thick from the temperature of the ceramic shell mould, alloy L35H7MP2 (Żółkiewicz et al. 2018; 2019)
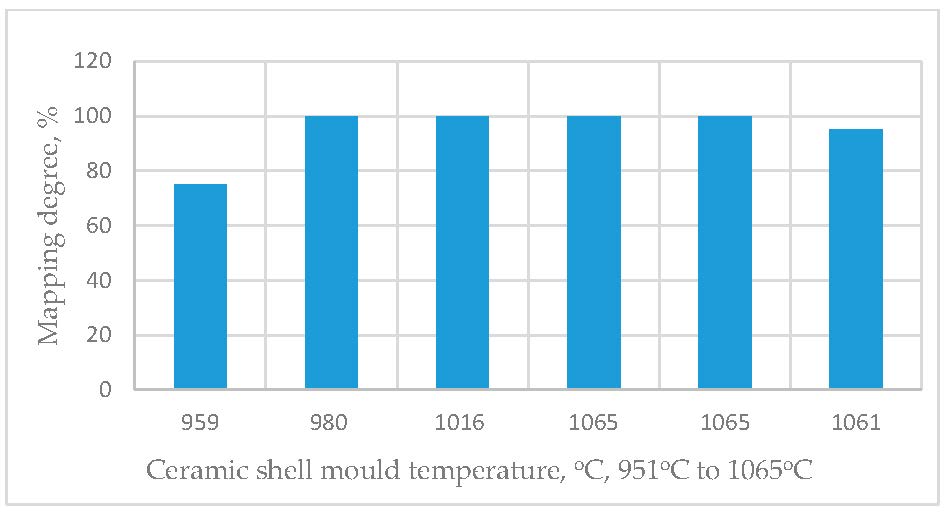
Figure 7.
Degree of mapping the wall shape 1mm thick from the pouring temperature of the ceramic shell mould, alloy LH26N9 (Żółkiewicz et al. 2018; 2019)
Figure 7.
Degree of mapping the wall shape 1mm thick from the pouring temperature of the ceramic shell mould, alloy LH26N9 (Żółkiewicz et al. 2018; 2019)
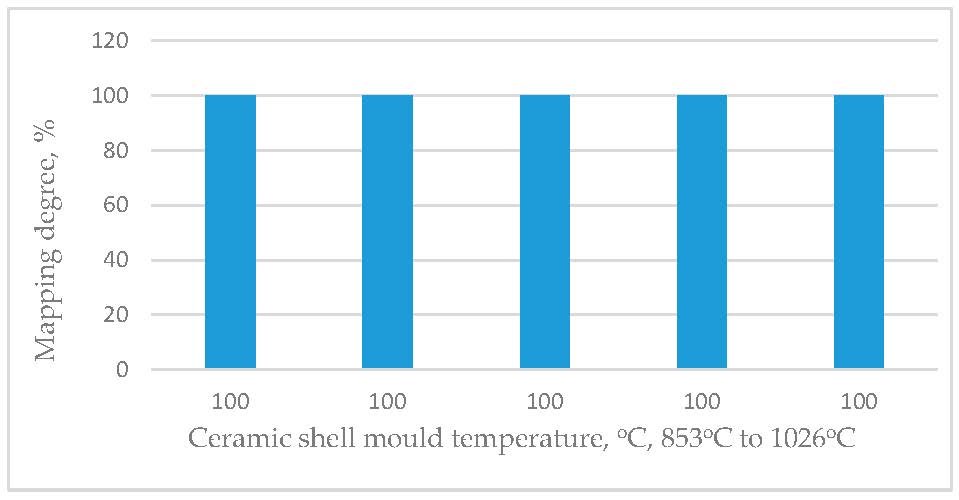
Figure 8.
Dependence of the degree of mapping the shape of a 1 mm thick casting made of alloy 0 from the pouring temperature, series 1 to 3 (Żółkiewicz et al. 2018; 2019)
Figure 8.
Dependence of the degree of mapping the shape of a 1 mm thick casting made of alloy 0 from the pouring temperature, series 1 to 3 (Żółkiewicz et al. 2018; 2019)
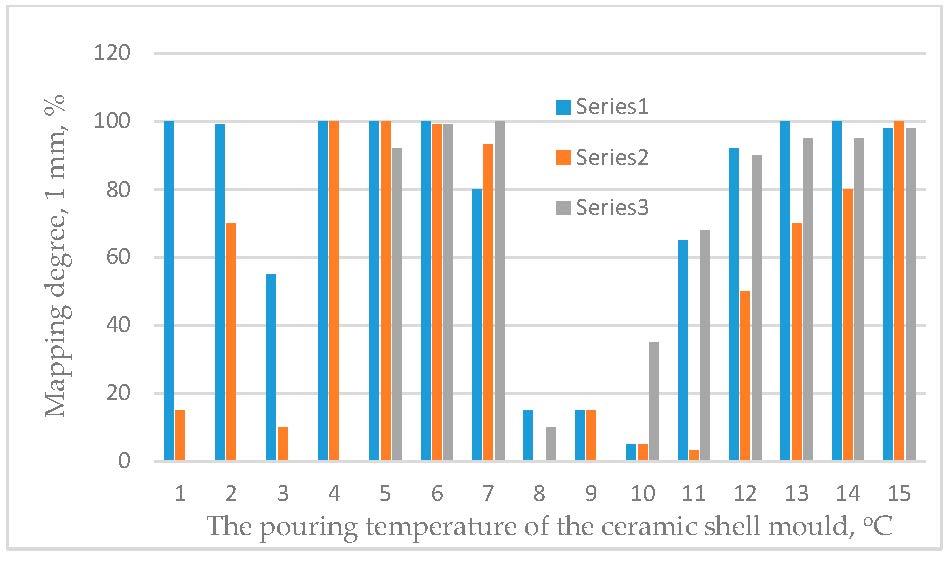
Figure 9.
Dependence of the mapping level of the casting wall 1 mm thick on the pouring temperature of the ceramic shell mould, 316L cast steel (Żółkiewicz et al. 2018; 2019)
Figure 9.
Dependence of the mapping level of the casting wall 1 mm thick on the pouring temperature of the ceramic shell mould, 316L cast steel (Żółkiewicz et al. 2018; 2019)
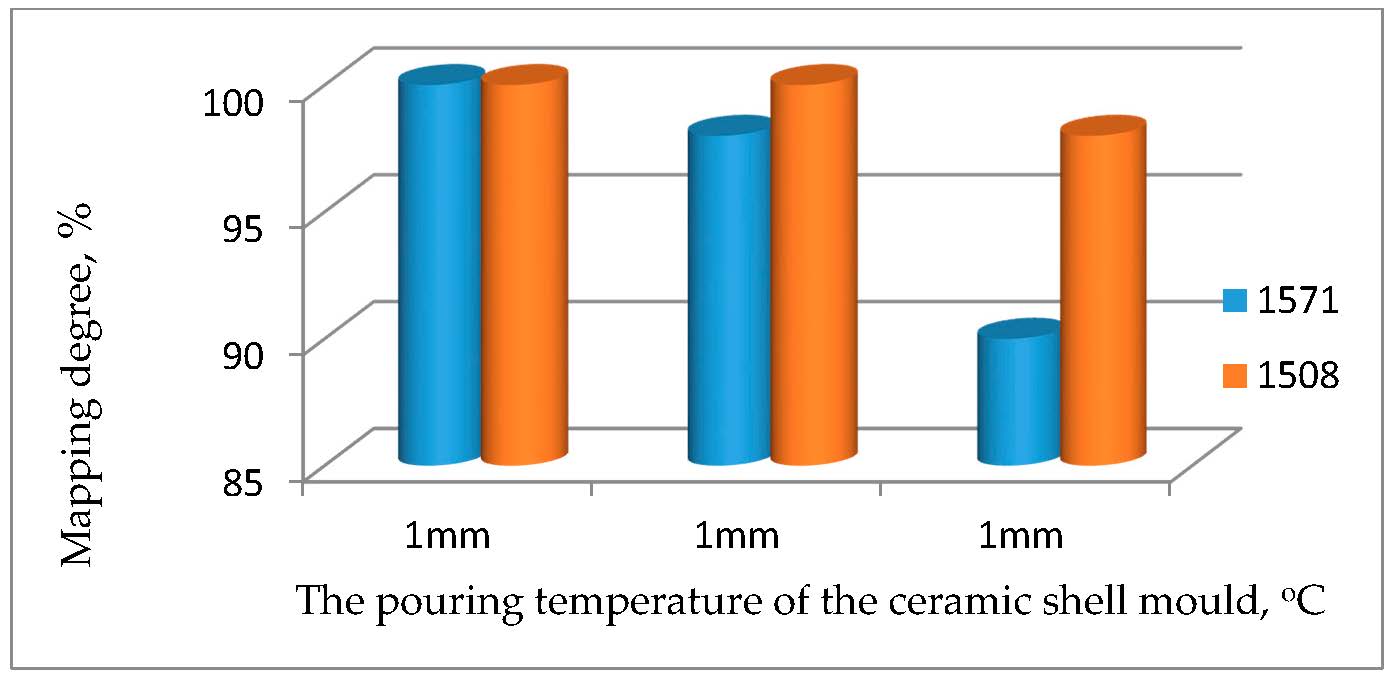
Table 1.
Dependence of the degree of mapping on the face of the casting made of the L35H7MP2 alloy 1 mm thick from the annealing temperature of the ceramic shell mould
Table 1.
Dependence of the degree of mapping on the face of the casting made of the L35H7MP2 alloy 1 mm thick from the annealing temperature of the ceramic shell mould
Temperature of the Ceramic Shell Mould [°C] | 959 | 980 | 1016 | 1061 | 1065 | 1066 |
Mapping Degree [%] | 77 | 100 | 100 | 94 | 100 | 100 |
Table 2.
Dependence of the degree of mapping on the face of the casting made of the LH14 alloy 1 mm thick from the annealing temperature of the ceramic mould
Table 2.
Dependence of the degree of mapping on the face of the casting made of the LH14 alloy 1 mm thick from the annealing temperature of the ceramic mould
Temperature of the Ceramic Shell Mould [°C] | 934 | 961 | 1050 | 1052 |
Mapping Degree [%] No 1 | 100 | 22 | 93 | 55 |
© 2021 Open Access. This article is distributed under the terms of the Creative Commons Attribution-ShareAlike 3.0 (CC BY-SA 3.0).