J_Appl_Mater_Eng 2021, 60(10), 121-129; doi:10.35995/jame60040010
Determination of Mass Loss in Samples of Post-Regeneration Dust from Moulding Sands with and without PCL Subjected to Biodegradation Processes in a Water Environment
1
Faculty of Foundry Engineering, AGH University of Science and Technology, Mickiewicza 30, 30-059 Krakow, Poland; katmg@agh.edu.pl
2
Łukasiewicz Research Network—Krakow Institute of Technology, Zakopianska 73, 30-418 Krakow, Poland
*
Corresponding author: iwona.stachurek@kit.lukasiewicz.gov.pl
How to cite: Major-Gabryś, K.; Hosadyna-Kondracka, M.; Stachurek, I. Determination of Mass Loss in Samples of Post-Regeneration Dust from Moulding Sands with and without PCL Subjected to Biodegradation Processes in a Water Environment. J. Appl. Mater. Eng. 2020, 60(4), 121–129, doi:10.35995/jame60040010.
Received: 30 December 2020 / Accepted: 12 May 2021 / Published: 15 May 2021
Abstract
:In recent years, the demand for products made of biodegradable or partially biodegradable materials has been increasing. This is mainly due to the ever-increasing amount of waste in landfills, but also to the problem of post-production waste management. This problem also concerns waste from the casting process of sands made on the basis of furfuryl resin, as well as residues from the regeneration process of these sands. The article presents the issues related to the methodology of research on the biodegradation process both in the natural environment and methods conducted in laboratory conditions. The preliminary results of the research on the biodegradation process in the aquatic environment, to which the dusts from mechanical regeneration of moulding sand were subjected, indicate the directions of further research and work in the field of selection of components of moulding sand with biodegradable properties. These tests should be carried out primarily in terms of determining the minimum and maximum amount of the addition of a biodegradable component to the moulding sand.
Keywords:
moulding sand; biodegradability; methods of biodegradation1. Introduction
The increase in production processes resulting from the growing demand for all kinds of products contributes to the rapid increase in post-production waste and products, mostly landfilled and present in the soil. It should be noted that most commonly used raw materials for their production are not decomposable or are difficult to decompose. These materials are resistant to numerous environmental factors; most of them are not damaged by water, air, sunlight or the action of microorganisms. Therefore, in recent years, there has been a growing interest in photodegradable and biodegradable materials with a controlled lifetime, where their degradation should start only after fulfilling its task. Generally, degradation is defined as an irreversible, often multi-step process leading to marked changes in chemical structure, usually resulting in a loss of performance in the material. The degradation can be caused by various factors in the environment as described by Bastian and Alleman (1996) and Sobków et al. (2014). When the degradation occurs under the influence of electromagnetic radiation, mechanical forces, heat, and active chemical compounds, it is defined as abiotic degradation. When the degradation process is caused by the action of biological factors (living organisms), mainly enzymes produced by various microorganisms, such as bacteria or fungi, it is biotic degradation (biodegradation, biological degradation). The potential biodegradability of a material, which has been determined or predicted on the basis of appropriate laboratory tests under strictly defined, controlled conditions, is called specific biodegradability. In turn, total (final) biodegradability is the total decomposition of the material by microorganisms, either in the presence of oxygen (aerobic biodegradation) to CO2, H2O, mineral salts with the formation of new biomass, or under anaerobic conditions (anaerobic biodegradation, biomethanization) to CO2, CH4, inorganic salts and biomass.
According to the tendencies observed in recent years, moulding processes must meet high requirements connected to environmental protection. One of scientific research directions is a gradual replacement of binding materials produced from petrochemical origins, with biopolymers coming from renewable resources, which is consistent with the conception of sustainable development—one of the priorities of the European Community policy. It has been forecast that within the next few years, the biodegradable polymers will cover 10% of the world’s market of polyolefines used in agriculture and for packaging (Eastman 2000). Choi and Park (1996) indicate that poly ɛ-caprolactone (PCL) is one of the most famous completely biodegradable polymers and has a unique characteristic—its compatibility with a variety of other polymers.
Literature data—presented in publications of Major-Gabryś et al. (2016) and Eastmond (2000)—shows that there is a possibility of using biodegradable materials as additives for petrochemical materials to increase their biodegradability. Further advantages of using biodegradable polymers, such as poly ɛ-caprolactone (PCL), as additives might include increase in flexibility of moulding sands with new two-component resins.
PCL is a polymer with proven biodegradable properties, belonging to the group of aliphatic polyesters. It is obtained from caprolactone by ring-opening polymerization. This polymer is easily mixed with many other raw materials and is therefore used as a plasticizer—increasing the flexibility of materials and their biodegradability. Degradation process of poly ɛ-caprolactone can be catalysed by enzymes and chemicals (Iwamoto and Tokiwa 1994).
Low flexibility of moulding and core sands is a problem in automated foundries (Grabarczyk and Dobosz 2016). The use of PCL as a plasticizer for plastics is not a new matter. From a technological point of view, the use of plasticizers for polymers is very important and widely used in various industries. In 1966, the use of PCL as a plasticizer for polyvinyl chloride (PVC) was patented (Major-Gabryś 2019).
Our own preliminary research, included in Major-Gabryś (2016), has shown that the moulding sands with biodegradable materials as binders are not only less toxic but they have a greater ability for mechanical regeneration than traditional synthetic resin moulding sands. It can be concluded that the partial replacement of the petrochemical origin binder with biodegradable material will improve the quality of tested moulding sands. In addition, the use of poly ɛ-caprolactone as a component of the new binder can improve the resistance to deformation of the moulding sand at ambient temperature, known in the literature as flexibility/elasticity (Major-Gabryś 2016; Eastmond 2000).
A broad analysis of literature data and our own research led us to a new perspective on the production of moulding and core sands that is based on partial replacement of synthetic foundry resins with biodegradable materials. This approach will reduce the technological costs in relation to process which used only biodegradable material as moulding sand’s binder. At the same time, it will allow us to modify well-known and widely used mould and core preparation technologies (Grabarczyk and Dobosz 2016). In parallel the effect of use of moulds made of moulding sand with biodegradable materials to cast ductile cast iron was examined. The quality, i.e., mechanical properties and microstructure characteristic, of the cast parts poured to sands moulds both, standard and modified, were examined and discussed (Hosadyna-Kondracka et al. n.d.). The problem in production of castings in moulding sands with organic binder is waste sand and/or regenerated dust.
The idea of the moulding sands with biodegradable materials as binders is to reduce the amount of waste materials. Initial comparative research of reclamation dusts of standard mould with furfuryl binder and two-component binder with the addition of PCL was presented.
There are several methods for determining the degree of degradation and biodegradation, and their main task is to determine the time after which they decompose and to determine the type and quantity of products produced during this process (Figure 1).
The most reliable results come from tests carried out in an appropriate environment (inoculum) and consisting of the assessment of changes in a specific environment and changes in the properties of the tested material. A commonly used environment for testing biodegradation is compost, i.e., a mineral soil nutrient obtained in the process of biological decomposition of mixtures of various plant residues, containing additional organic substances and a certain amount of minerals. The storage time of the material, depending on the environment, may be from several dozen days to several months or even years. A very important factor is the size of the tested material sample—the ratio of the sample surface area to its volume should be as large as possible, as the more developed the specific surface of the sample, the faster the material degrades. In the case of research carried out in soil, compost or in the aquatic environment, its quality plays an important role, including the type and activity of microorganisms that live in it, and the storage conditions of the tested material. Temperature and pH of the biodegradation process are also important factors. Their selection depends primarily on the planned duration of the experiment. Conducting biodegradation at a higher temperature promotes faster degradation; however, the results obtained in the study may differ from the actual ones, as artificially increasing the temperature creates conditions that differ from those in the natural environment. The most favourable temperature range for biodegradation in soil is 10–27 °C. In turn, biodegradation in compost takes place at a higher temperature than the process carried out in soil—the optimal temperature range is 56–65 °C. An important factor during biodegradation is the measurement of pH, O2, CO2 and humidity of the degradation environment, as water is the basic medium carrying microorganisms and mineral nutrients, and an insufficient amount may inhibit the metabolism of microorganisms (Sobków et al. 2014; Fecko et al. 2010; Park et al. 2001). Laboratory methods used to study the course of degradation and biodegradation of materials consist mainly of determining the loss of sample mass and analysing changes in the chemical structure and morphology, as well as determining the changes in the mechanical and physicochemical properties of the material. Measurement of the loss of mass after a certain period is one of the most frequently used methods of determining the degree of biodegradation. However, this method leads to approximate results. During the process, part of the material is converted into CO2 and other products, such as CH4, which reduce the mass of the test sample. There are several ways to conduct the biodegradation process where the released CO2 is measured and each of these methods is defined by appropriate standards. One of them is carrying out the process in a reactor in a suitable environment (e.g., soil, compost, water). During the process, the amount of CO2 evolved is measured by titration analysis, infrared spectroscopy or gas chromatography, and the humidity, temperature and oxygenation levels in the reactors are monitored. In the case of biodegradable materials, the test lasts 28 days, while for materials that require longer time, the so-called “Bottle method” is used, in which the reactors are replaced by 1–2-liter bottles (Gutowska et al. 2013; Stachurek 2010). This method does not require continuous aeration of the reaction medium (Figure 2).
Measurement of the amount of released CO2 requires an initial determination of the organic carbon content in the sample—Ci; then, the theoretical CO2 efficiency that may arise during the biodegradation process (ThCO2) should be determined:
where:
- Mt—mass of the sample in the reactor;
- 44—CO2 molar mass;
- 12—C atomic mass.
The amount of CO2 formed during biodegradation is determined from the difference in mass of the CO2 absorber (Ba(OH)2 or NaOH) at the beginning of the process and after a specified degradation time. The total degree of biodegradation (B) is calculated as the ratio of the amount of released CO2 determined in the test to the theoretical efficiency:
where:
- mCO2 (test)—CO2 mass separated from the tested sample in (g);
- mCO2—CO2 mass separated from the blank in (g).
2. Materials and Methods
Dust samples obtained after mechanical regeneration of self-hardening moulding sands with furfuryl resin were subjected to biodegradation tests (Table 1). The composition of the sand mixtures used for regeneration process are presented in Table 2.
Two types of samples were tested. The first group was made up of dust samples obtained after the sand regeneration process without the addition of biodegradable substances; the second group consisted of sand dust samples with the addition of a biodegradable substance, which is poly ɛ-caprolactone (PCL). The regeneration process was carried out in an RD-6 rotor regenerator and was carried out with a closed dust chamber. In the first stage of the process, the used moulding sand was crushed and dedusted in a cascade classifier. Samples were taken from the obtained material—sample 1 and sample 5. Next, the regeneration process was carried out, the duration of which were 5, 10 and 15 min. The obtained regenerates were dedusted in a cascade classifier (Major-Gabryś et al. 2020).
Biodegradation studies were carried out in a natural environment, which was water from the Vistula River (inoculum). The location of water intake was the Kościuszko barrage in Krakow. Three gram samples were placed in polypropylene containers and then 100 ml of water was added to each system. The samples were stored in closed vessels at room temperature for 3 months.
After completion of the test, the samples were drained, dried in a laboratory dryer at 105 °C to constant weight, weighed and the weight loss of the samples was determined. At the same time, the colour of the sediment was assessed.
The weight loss was calculated from the formula:
where:
- Δm—percentage of weight loss, %;
- mp—initial mass, g;
- msp—mass of solid residue, g.
3. Results and Discussion
During the biodegradation test, the colour changes of the solutions were assessed. Additionally, after the test was completed, the colour of the sediment was assessed (Table 3). In the case of systems containing a biodegradable substance in their compositions, a slight change in the colour of the solution was observed. In the case of solutions containing dust after regeneration of furfuryl resin without the addition of PCL, the solutions were colourless. On the other hand, the dust solutions with the addition of poly ɛ-caprolactone showed a light brown colour. The discolouration of the solution was probably due to compounds, that went into the solution. The poly ɛ-caprolactone probably dissolved in water and coloured the solution.
Figure 3 and Figure 4 show the appearance of the sediment of selected samples after the biodegradation process.
Figure 5 shows the percentage weight loss determined after the biodegradation process.
Table 4 presents the obtained results of the percentage weight loss of the samples after the biodegradation process.
In the case of samples 1 to 4, a slight weight loss was noted after the biodegradation process, which amounted to an average 3%. Larger weight loss was noted for samples 5 to 8, i.e., dust samples after the regeneration process of moulding sands based on furfuryl resin when a biodegradable agent, poly ɛ-caprolactone, was added. In the case of these samples, a weight loss at the level of 8–9% was noted.
The greater weight loss recorded for the samples with the addition of the biodegradable factor poly ɛ-caprolactone was the result of changes in the polymer morphology under the influence of the water environment. Polymers are semi-crystalline compounds, meaning they contain both amorphous and crystalline regions. In the amorphous phase, the polymer chains are arranged in a disorderly manner, more or less entangled, and entangled with each other. The distances between macromolecules vary and are in most cases too large for strong intermolecular bonds to form. These factors influence the high mobility of macromolecule chains and their higher availability for microorganisms, hence the biodegradation process takes place faster in amorphous areas. Literature data—presented in publications of Choi and Park (1996)—shows that mass losses were also observed in the case of moulding sand samples to which a mixture of poly ɛ-caprolactone with styrene acrylonitrile (PCL/SAN) was added in the compositional range above 50 wt% of PCL. The research assumed that the crystalline phase of the blend sample was only composed of the pure PCL component without any SAN impurity, while the amorphous phase was a homogeneous mixture of PCL and SAN which was used to quantify the morphological factor. The morphological factor is defined as the fraction of amorphous region based on the total weight of the blend sample and determines the biodegradability of compounds. The obtained results indicated the biodegradation process in the samples of PCL/SAN blends.
4. Conclusions
The introduction of recovery and re-use in the production of raw materials is currently one of the methods with an ever-increasing amount of post-production waste. A solution that is beneficial from the point of view of environmental protection is the process of regeneration of moulding and core sands. The use of this process has not only environmental but also economic benefits. Reusing sand not only reduces the amount of waste generated, but also reduces the amount of purchased sand used in the production process.
Biodegradation tests proved that moulding sand with PCL added at the stage of the production process is characterized by a better biodegradability, by about three times, than the same moulding sand without additive.
The presented results are part of complex comparative research concerning mechanical and thermal behaviours of various types of moulding and core sands. Their ability to conduct mechanical reclamation and an investigation into the biodegradation rate of moulding sands with new binders are also worth considering.
Author Contributions
Conceptualization, K.M.-G., M.H.-K. and I.S.; Methodology, K.M.-G., M.H.-K. and I.S.; Software, K.M.-G., M.H.-K. and I.S.; Validation, K.M.-G., M.H.-K. and I.S.; Formal Analysis, K.M.-G., M.H.-K. and I.S.; Investigation, K.M.-G., M.H.-K. and I.S.; Resources, K.M.-G., M.H.-K. and I.S.; Data Curation, K.M.-G., M.H.-K. and I.S.; Writing—Original Draft Preparation, K.M.-G., M.H.-K. and I.S.; Writing—Review and Editing, K.M.-G., M.H.-K. and I.S.; Visualization, K.M.-G., M.H.-K. and I.S.; Supervision, K.M.-G., M.H.-K. and I.S.; Project Administration, K.M.-G., M.H.-K. and I.S.; Funding Acquisition, K.M.-G., M.H.-K. and I.S.
Funding
This research was performed within the project of MNiSW “Oddziaływanie odlewniczych mas odpadowych na środowisko naturalne – proces (bio)degradacji w środowisku wodnym i glebie” (project no. 1012/00).
Conflicts of Interest
The authors declare no conflict of interest.
References
- Bastian, K. C.; Alleman, J. Environmental Bioassay Evaluation of Foundry Waste Residuals; Publication FHWA/IN/JHRP-96/04. Joint Highway Research Project; Indiana Department of Transportation and Purdue University: West Lafayette, IN, 1996. [Google Scholar] [CrossRef]
- Choi, E. J.; Park, J. K. Study on biodegradability of PCL/SAN blend using composting method. Polymer Degradation and Stability 1996, 52(3), 321–26. [Google Scholar] [CrossRef]
- Eastman, J. Protein-Based Binder Update: Performance Put to the Test. Modern Casting 2000, 10, 32–34. [Google Scholar]
- Eastmond, G. C. Poly(ε-caprolactone) Blends. Advances in Polymer Science 2000, 149, 59–222. [Google Scholar]
- Fecko, P.; Pertile, E.; Lyčková, B.; Vojtkova, H.; Janáková, I.; Tora, M. Biodegradation of hazardous pollutants. Journal of the Polish Mineral Engineering Society 2010, January–December, 41–48. [Google Scholar]
- Grabarczyk, A.; Dobosz, St. M. V Conference of PhD Students at the Faculty of Foundry Engineering; AGH University of Science and Technology: Kraków, Poland, 9 May 2016. [Google Scholar]
- Gutowska, A.; Michniewicz, M.; Ciechańska, D.; Szalczyńska, M. Metody badania biodegradowalności materiałów biomasowych. In Chemik; 2013; Volume 67, 10, pp. 945–54. (In Polish) [Google Scholar]
- Hosadyna-Kondracka, M.; Major-Gabryś, K.; Brůna, M. n.d. The influence of biodegradable additive in moulding sand on structure and mechanical properties of ductile iron casting. Archives of Metallurgy and Materials. submitted for publishing.
- Iwamoto, A.; Tokiwa, Y. Enzymatic degradation of plastics containing polycaprolactone. Polymer Degradation and Stability 1994, 45(2), 205–13. [Google Scholar] [CrossRef]
- Major-Gabryś, K.; Hosadyna-Kondracka, M.; Skrzyński, M.; Pastirčák, R. The quality of reclaim from moulding sand with furfuryl resin and PCL additive. The abstract paper at XXVI International Conference of Polish, Czech and Slovak Founders—Spolupráca, Baranów Sandomierski, Poland, 7–9 September 2020; 2020. [Google Scholar]
- Major-Gabryś, K. Environmentally Friendly Foundry Molding and Core Sands. Journal of Materials Engineering and Performance 2019, 28(7), 3905–11. [Google Scholar] [CrossRef]
- Major-Gabryś, K. Odlewnicze masy formierskie i rdzeniowe przyjazne dla środowiska; Wydawnictwo Archives of Foundry Engineering: Katowice; Gliwice, 2016. (In Polish) [Google Scholar]
- Major-Gabryś, K.; Grabarczyk, A.; Dobosz, St. M.; Jakubski, J. New Bicomponent Binders for Foundry Moulding Sands. Metalurgija 2016, 55(3), 385–87. [Google Scholar]
- Park, J.; Chen, Y. M.; Kukor, J.J.; Abriola, L.M. Influence of substrate exposure history on biodegradation in a porous medium. Journal of Contaminant Hydrology 2001, 51(3–4), 233–56. [Google Scholar] [CrossRef]
- Sobków, D.; Barton, J.; Czaja, K.; Sudoł, M.; Mazoń, B. Badania odporności materiałów na działanie czynników środowiska naturalnego. Chemik 2014, 68(4), 347–54. [Google Scholar]
- Stachurek, I. Biomedical Systems of Polyethylene Oxide Biodegradable in the Aquatic Environment. Doctoral dissertation, Cracow University of Technology, Poland, 2010. [Google Scholar]
Figure 1.
Test methods for the biodegradation process (Gutowska et al. 2013; Stachurek 2010)
Figure 1.
Test methods for the biodegradation process (Gutowska et al. 2013; Stachurek 2010)
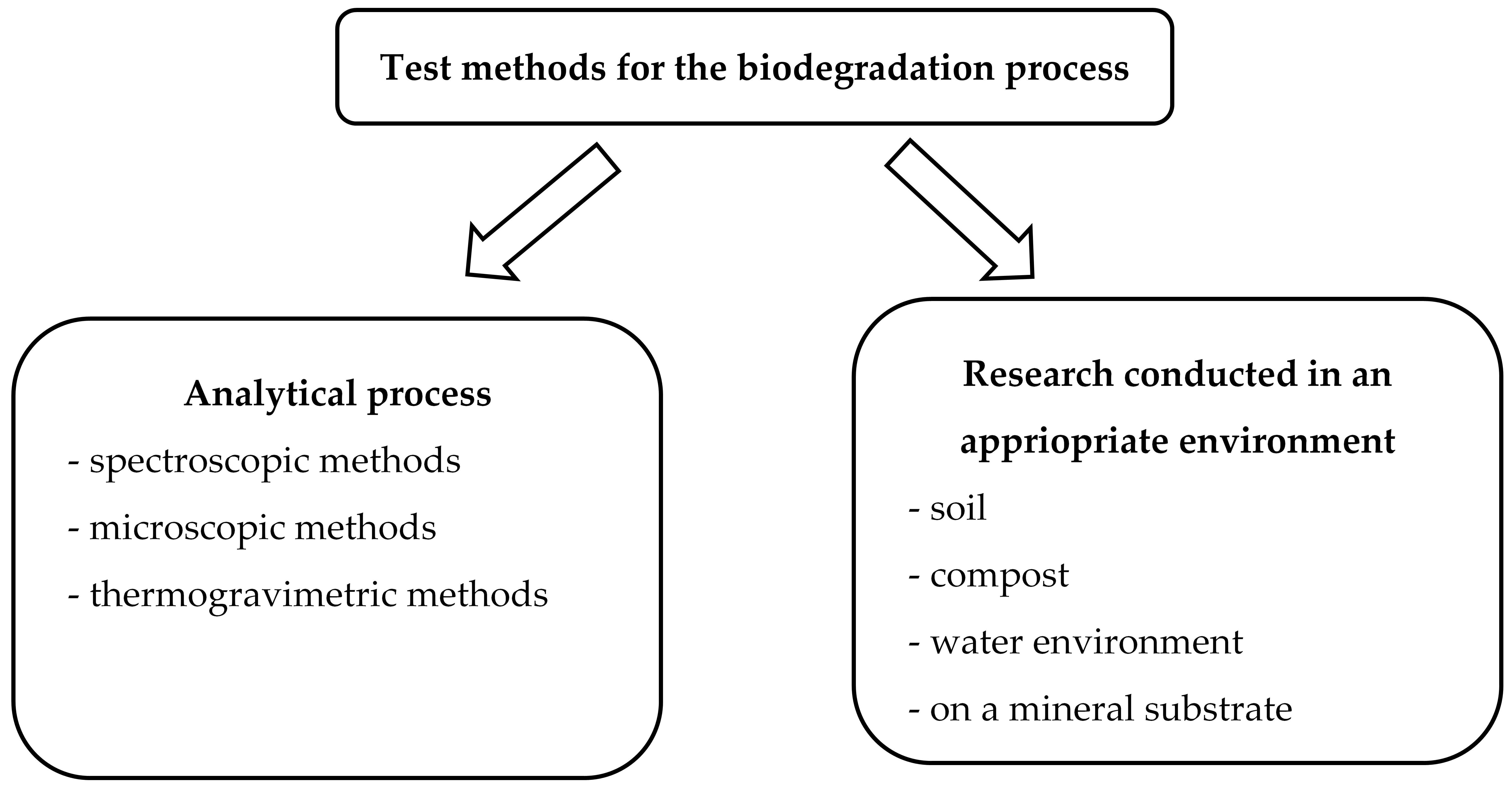
Figure 2.
Diagram of apparatus for the biodegradation process using the “bottle method” (Stachurek 2010)
Figure 2.
Diagram of apparatus for the biodegradation process using the “bottle method” (Stachurek 2010)
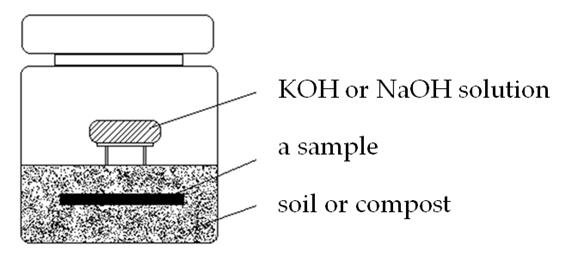
Figure 3.
The sediment of sample 4 after the biodegradation process
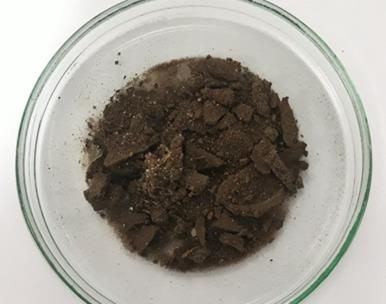
Figure 4.
The sediment of sample 8 after the biodegradation process
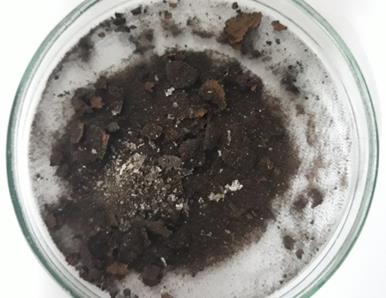
Figure 5.
Percentage weight loss red colour and residue materials blue of samples after completion of the biodegradation process
Figure 5.
Percentage weight loss red colour and residue materials blue of samples after completion of the biodegradation process
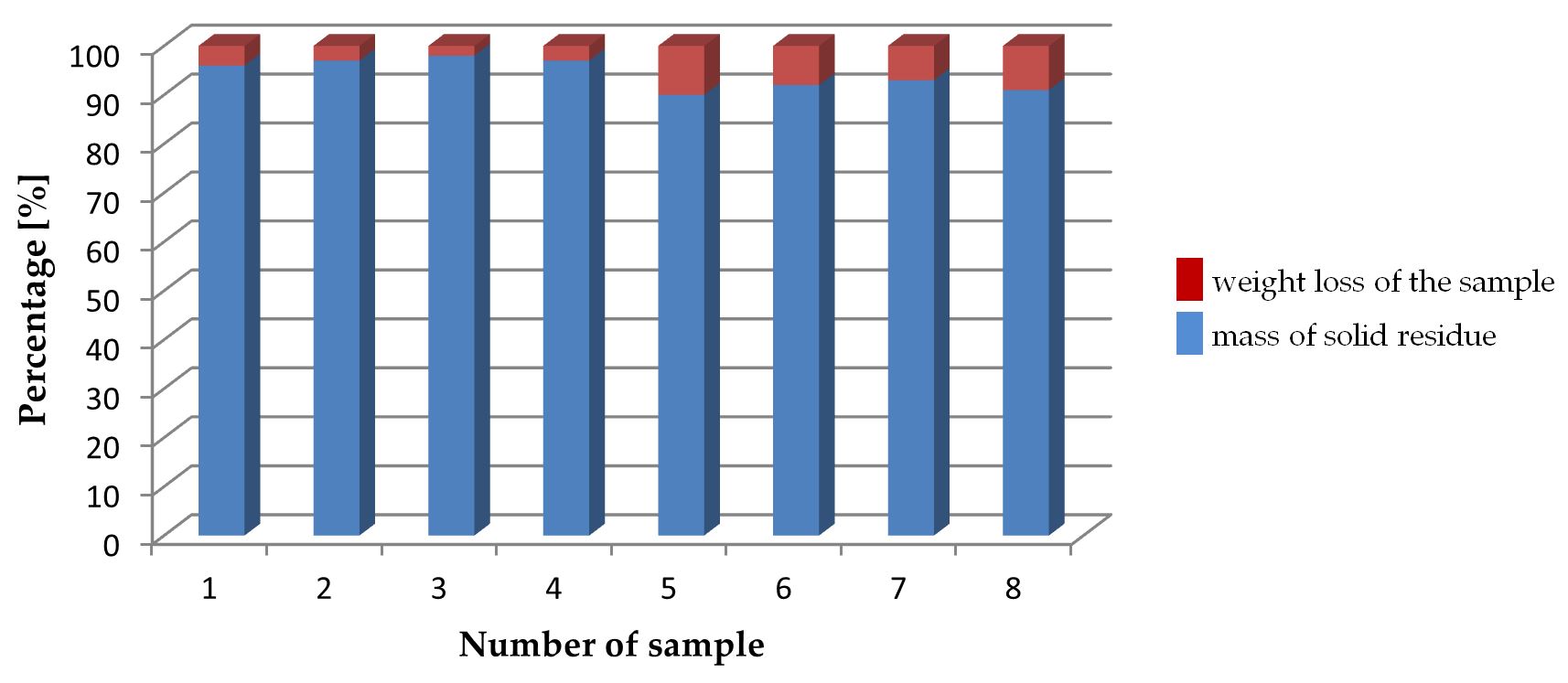
Table 1.
List of tested samples in biodegradation tests
Sample number | Time of sampling from the beginning of the regeneration process | |
---|---|---|
1 | after initial regeneration | Dust samples obtained after mechanical regeneration of Moulding sand no. 1 (without the addition of biodegradable substances) |
2 | 5 minutes | |
3 | 10 minutes | |
4 | 15 minutes | |
5 | after initial regeneration | Dust samples obtained after mechanical regeneration of Moulding sand no. 2 (with the addition of poly ɛ-caprolactone) |
6 | 5 minutes | |
7 | 10 minutes | |
8 | 15 minutes |
Table 2.
The composition of self-hardening moulding sands subjected regeneration process
Moulding sand no. 1 | ||
silica sand | 100 parts by weight | |
phenol-furfuryl resin | 1.1 parts by weight | |
hardener | 0.55 parts by weight | |
Moulding sand no. 2 | ||
silica sand | 100 parts by weight | |
phenol-furfuryl resin | 1.1 parts by weight | 1.045 parts by weight (95%) |
PCL polikaprolakton | 0.055 parts by weight (5%) | |
hardener | 0.55 parts by weight |
Table 3.
Evaluation of the colour of the solution and sediment of the systems after 30 days of biodegradation
Table 3.
Evaluation of the colour of the solution and sediment of the systems after 30 days of biodegradation
Sample number | Colour of the solution | Colour of the sediment |
---|---|---|
1 | colourless | brown |
2 | colourless | brown |
3 | colourless | dark brown |
4 | colourless | dark brown |
5 | light brown | dark yellow |
6 | light brown | light brown |
7 | light brown | brown |
8 | light brown | dark brown |
Table 4.
Percentage results of the sample weight loss after the biodegradation process
Sample number | Percentage of weight loss (%) |
---|---|
1 | 4 |
2 | 3 |
3 | 2 |
4 | 3 |
5 | 10 |
6 | 8 |
7 | 7 |
8 | 9 |
Publisher’s Note: MDPI stays neutral with regard to jurisdictional claims in published maps and institutional affiliations. |
© 2021 Open Access. This article is distributed under the terms of the Creative Commons Attribution-ShareAlike 3.0 (CC BY-SA 3.0).