J_Appl_Mater_Eng 2020, 60(2–3), 47-52; doi:10.35995/jame60020004
Supporting Body Material for Ceramic Diamond Grinding Tools
1
Łukasiewicz Research Network – Krakow Institute of Technology, ul. Zakopiańska 73, 30-418 Kraków, Poland; pawel.figiel@kit.lukasiewicz.gov.pl (P.F.); grzegorz.skrabalak@kit.lukasiewicz.gov.pl (G.S.)
2
University of Silesia, Institute of Engineering Materials; ul. 75 Pułku Piechoty 1a, 41-500 Chorzów, Poland; karolus.@us.edu.pl
*
Corresponding author: barbara.brudnik@kit.lukasiewicz.gov.pl
How to cite: Staniewicz-Brudnik, B.; Figiel, P.; Skrabalak, G.; Karolus, M. Supporting Body Material for Ceramic Diamond Grinding Tools. J. Appl. Mater. Eng. 2020, 60(2–3), 47–52, doi:10.35995/jame60020004.
Received: 1 May 2020 / Accepted: 15 October 2020 / Published: 28 October 2020
Abstract
:The characteristics of abrasive tools (the type of grinding wheel, granulation of the super hard grain, type of structure, hardness, and the type of binder) contain information on the type of supporting body materials used (e.g., dural, ceramic, steel). In this work, diamond wheels were obtained on ceramic supporting bodies, containing a sintered mixture of white alumina 99A granulation F320, green silicon carbide 99A granulation F320, and binder Ba23 bis, together with modifiers. The mechanical properties (hardness, bending strength) of ceramic supporting bodies were tested. The structure of the phase boundary of the ceramic supporting body–abrasive grinding tool was analyzed on a BEC (backscattered electron composition) image by using SEM (Scanning Electron Microscopy). It was found that the hardness of the supporting body was slightly lower (70–75 HRB) than the diamond wheels (76–81 HRB). The bending strength of the supporting bodies was high (85 ±2 MPa). The BEC image from the scanning microscope did not show a sharp transition between the ceramic supporting body and the grinding wheel. Preliminary operational tests showed significant improvement in grinding wheel efficiency in comparison to diamond tools with the same ceramic binder on a duralumin supporting body during machining of G30 sintered carbide bush.
Keywords:
ceramic supporting body; vitrified bonds; diamond wheels; corundum; silicon carbide1. Introduction
New materials used in industry, such as plastics reinforced with glass fiber composites, non-ferrous metal alloys reinforced with hard particles, composites made of sintered carbides doped with super-hard grains, and super alloys of nickel (Hastalloy, Waspalloy, Inconel 718, Udimet 720) and titanium (Ti6Al4V, TiAl) for precise and effective machining of cavities, require novel machining technologies as well as novel tools, like super-hard abrasive tools with new binders and supporting bodies (Oczoś and Porzycki 1986; Weiß 2019).
For the proper choice of grinding tool for a specific application, the characteristics of the tool should be composed from not only the description of the binder and abrasive grain type and concentration, but it also should include information on the type of supporting body to which the abrasive coating of the tool has been attached. The literature analysis of the manufacturing catalogue (Swaty Comet 2014; Lukas Tool 2018; Winter’s Tool 2014; PFERD 2018; Krebs & Riedel 2016; DIAMENTPOL 2017) showed a wide range of materials used for the supporting bodies: starting from commonly used duralumin PA6, stainless steel, sintered carbides for mounted points, Bakelite–resin pistons, ceramic sinters, to composites containing carbon fiber, steel, and alumina (Winter’s Tool 2014). The use of each of these materials is justified. Lukas-made cBN ceramic bonded mounted points (Lukas Tool 2018) with carbide rather than steel-mounted points, because they have a three times higher elasticity modulus (module E). A higher elasticity modulus increases the stability of the tool, extends its service life, and improves the quality of the machined surface. Steel bodies, on the other hand, significantly heavier than duralumin ones, are used in very thin grinding wheels in order to maintain the stability of the mechanical properties of the tool. Ceramic sintered abrasive bodies have similar mechanical properties to aluminum sintered bodies; they are rigid, hard, well-damping, and allow full use of the working ring. Swaty Comet performed a comparative analysis of the degree of vibration damping, thermal conductivity, and mechanical strength of various types of supporting bodies (Table 1).
As a result, it is necessary to adapt the tool body to the type of machining operation and the type of adhesive used. The aim of our work is to obtain a diamond abrasive tool with a ceramic bond and ceramic supporting body in one technological operation. The body of the diamond tool contains a newly developed ceramic bond modified with green silicon carbide and white fused corundum in appropriate proportions. The advantage of using such a supporting body is the limitation of possibility of residual stresses appearing at the interface between the supporting body and the abrasive ring, with similar hardness and bending strength.
2. Materials and Methods
The subject of research was abrasive composites with structures of 40 and 42 containing a working ring with diamond grains and a ceramic bond Ba23 bis (Staniewicz-Brudnik et al. 2017) and a ceramic supporting body being a mixture of white fused corundum 99A with granulation F320, silicon carbide 99C with granulation F320, and ceramic bond Ba23 bis with modifiers selected from among 30 previously developed and tested formulas. The abrasive masses for the working coating (diamond) and the ceramic supporting body were prepared in separate containers, in which the sieved and weighed components were mixed using a turbula. The cold pressing of the tools was divided into three stages, using a multi-part matrix. During the first stage, the tools were backfilled into the matrix and the ceramic supporting body was pressed. In the second stage, the working ring was backfilled and pressed. Finally, in the third stage, the whole unit was pressed. The heat treatment of the tool (grinding wheels type 1A1) was carried out in an electric furnace type KS 520/14, in accordance with the previously determined characteristics (Staniewicz-Brudnik 2017).
After the heat treatment, the tools were subjected to a sensory analysis (measurement of diameter, height of the coating, determination of deviations from the assumed values). Next, the tools were examined using a JOEL JSM 6460LV scanning electron microscope. The measurements were made in high vacuum conditions (10−5 Torr), at accelerating voltage of 20 kV and 100× magnification, using a backscattered electron composition (BEC) image. Microanalysis of the chemical composition “along the line” at the border of the body of the ceramic abrasive coating was made, along with maps of the surface distribution of the elements in the same area, using the EDS INCA X-act Energy 350 spectrometer by Oxford Instruments. The hardness of the grinding wheel was measured along the entire diameter of the wheel, based on the reading of a 1/16-inch steel ball indentation on the HRB scale on the Rockwell hardness tester. The bending strength of the body abrasives was tested using a three-point bending method on a 50 × 4 × 4 × 4 mm Instron machine under the following conditions: support spacing of 40 mm, test rate of 0.1 mm/min, and 90% Fmax failure rate. Preliminary and comparative tests were carried out on diamond grinding wheels with a ceramic bond with a ceramic supporting body (2 pieces) and diamond grinding wheels with the same adhesive bond bonded to a duralumin supporting body (2 pieces).
3. Discussion of the Results
Sensory analysis of the diamond grinding wheels with ceramic bodies type 1A1 35x5x5x5x10 D 126 c100 V (four pieces) showed deviations in tool diameter in the range of 0.12% (0.04 mm—average from four measurements) and on the height of the coating—shrinkage of 0.09 mm, i.e., 1.8%—which confirmed the proper selection of heat treatment characteristics (Figure 1a,b).
The analysis of the ceramic coated grinding wheel surface in the BEC (backscattered electron composition) image did not show any distinctive marked difference between the ceramic supporting body and the grinding wheel coating (Figure 2). Only the distribution of the elements “along the line” showed a change in the elemental composition. In the grinding wheel coating, an increased content of carbon (diamond) was visible, which almost completely disappeared on the surface of the ceramic supporting body.
On the other hand, the content of the aluminum significantly increased on the surface of the ceramic supporting body. Silicon was present both in the grinding wheel coating and in the ceramic supporting body. This was confirmed by maps of the surface distribution of the elements of this area (Figure 3).
The results of the tests of the hardness of the grinding wheels with structures of 40 and 42 showed slight differences in values along the line of the ceramic body diamond mound. For both structures, the average value of the hardness of the body was in the range 70–75 HRB and the hardness of the diamond ring 76–81 HRB (Table 2). Bending strength tests of the ceramic supporting bodies confirmed their high bending strength (85 ±2 MPa).
Preliminary Operational Tests of Diamond Grinding Wheels
The tests were carried out on an SOJ hole grinder made by Jotes (Staniewicz-Brudnik 2017). G30 sintered carbide bushings of hardness HV30 1250 and dimensions 42 × 18 mm were machined using diamond grinding wheels with a ceramic binder on ceramic supporting bodies (two pieces) and diamond grinding wheels with the same ceramic binder, adhesive to a PA6 dural supporting body. The tests were carried out under the following conditions (Table 3):
In Table 4 below comparative results are presented of grinding wheel no. 1 with a ceramic supporting body and grinding wheel no. 3 with abrasive adhesives to the supporting body made of duralumin PA6. Significant differences in the work of the tools can be explained by additional vibrations occurring in the grinding wheels’ adhesives to the duralumin supporting body, which interfere with the work of the tool and reduce its efficiency.
4. Conclusions
- The analysis of the obtained results (hardness, bending strength) confirmed the proper selection of the chemical composition of the ceramic supporting body for a diamond grinding wheel with a ceramic binder, as well as the characteristics of heat treatment (curing time and controlled cooling).
- The BEC image from the scanning microscope did not show any sharp borderline between the ceramic body and the grinding wheel coating (Figure 3). Microanalysis of the elemental composition “along the line” on the phase border confirmed the presence of carbon (diamond) only in the grinding wheel coating, alumina—first of all in the cermet body, and silicon, in the supporting body and coating of the grinding wheel.
- Operational tests of the grinding wheels when grinding holes in G30 sintered carbide sleeves showed the significant influence of the type of applied bodies on the tool performance.
- The possibility of shortening the grinding wheel production time by sticking the grinding wheel coating to the duralumin supporting body reduces the cost of manufacturing the tool and, most of all, affects its quality and durability.
- The concept of using this modified bond for abrasive tool bodies is limited to small size grinding tools (ϕ 12–50 mm) because of the slightly higher cost of manufacturing glass frit than PA6 duralumina supporting body. This kind of grinding tool can be used for grinding internal and external cylindrical surfaces e.g., in rolling bearing elements, carbide matrix elements, and holes in ceramic nozzles.
Author Contributions
Conceptualization, B.S.-B.; Methodology, B.S.-B. and M.K.; Validation, B.S.-B., M.K. and P.F.; Formal Analysis: B.S.-B., P.F., and M.K.; Investigation, B.S.-B., P.F., G.S. and M.K.; Resources, B.S.-B.; M.K., Data Curation, B.S.-B.; Writing—Original Draft Preparation, B.S.-B.; Writing—Review and Editing, B.S.-B.; Visualization, B.S.-B., G.S., and P.F., Supervision, B.S.-B.; Project Administration, B.S.-B.; Funding Acquisition, B.S.-B.
Funding
The project was carried out at Łukasiewicz – IAMT own funds.
Conflicts of Interest
The authors declare no conflict of interest.
References
- DIAMENTPOL. Catalogue of DIAMENTPOL Firm: Main Catalogue of Diamonds and CBN Tools. 2017. Available online: www.diamentpol.com.pl (accessed on 6 April 2020).
- Krebs & Riedel. Catalogue of Krebs & Riedel Firm: Vitrified—Bonded CBN and Diamond Tools from KREBS&RIEDEL—The Ultimate in Grinding. 2016. Available online: www.krebs-riedel.com (accessed on 8 April 2020).
- Lukas Tool. Catalogue of Lukas Tool. 2018. Available online: https://lukas-erzett.com (accessed on 17 April 2020).
- Oczoś, K.; Porzycki, J. Grinding of the Base and Technique; Wydawnictwa Naukowo-Techniczne: Warszawa, 1986. [Google Scholar]
- PFERD. Catalogue of PFERD Firm: Diamond and CBN Tools (in Polish), No. 205. 2018. Available online: www.pfered.com (accessed on 19 April 2020).
- Staniewicz-Brudnik, B. Korpusy ceramiczne do narzędzi ściernych supertwardych, Raport of IAMT DS. 3.2.2. (Not published, in Polish). 2017.
- Staniewicz-Brudnik, B.; Bączek, E.; Skrabalak, G. Patent PL226 206, 30 June 2017. (In Polish).
- Swaty Comet. Catalogue 1 Superabrasive Grinding Tools by Swaty Comet. Paragon Invent d.o.o. 2014 Edition. 2014. Available online: www.tesmasport.com (accessed on 4 April 2020).
- Weiß, M. Surface and profiling grinding. Paper presented at Grinding Symposium, Thun, Switzerland, May 8–10; 2019. [Google Scholar]
- Winter’s Tool. Catalogue of Winter’s Tool. 2014. Available online: www.nortonabrasives.com (accessed on 3 April 2020).
Figure 1.
Diamond grinding wheels with ceramic body (a); matrix for pressing of diamond grinding wheels with ceramic supporting body (b)
Figure 1.
Diamond grinding wheels with ceramic body (a); matrix for pressing of diamond grinding wheels with ceramic supporting body (b)
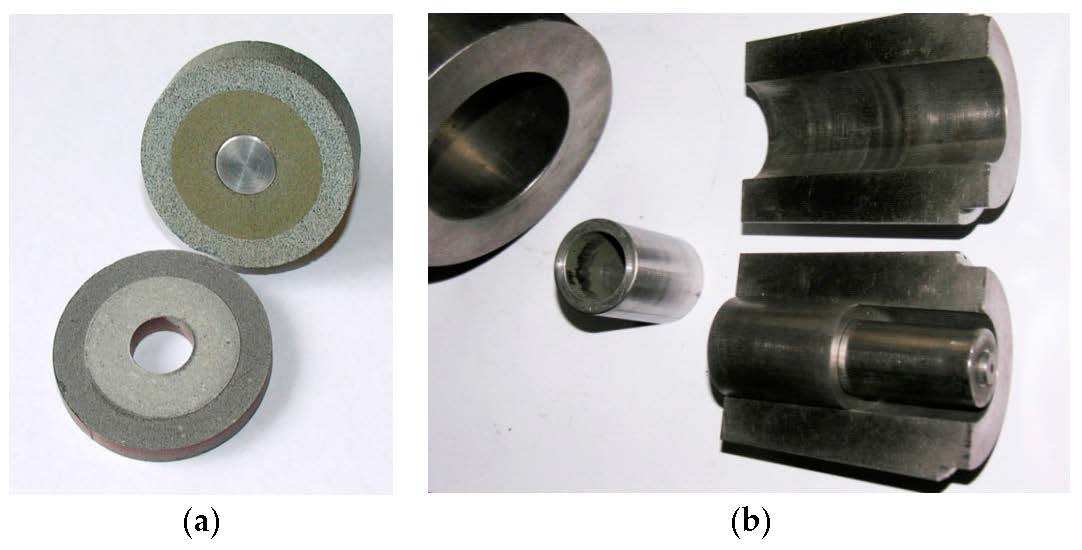
Figure 2.
Micrograph of the surface area of the boundary area ceramic supporting body—diamond grain (obtained by backscattered electron composition (BEC) techniques)
Figure 2.
Micrograph of the surface area of the boundary area ceramic supporting body—diamond grain (obtained by backscattered electron composition (BEC) techniques)
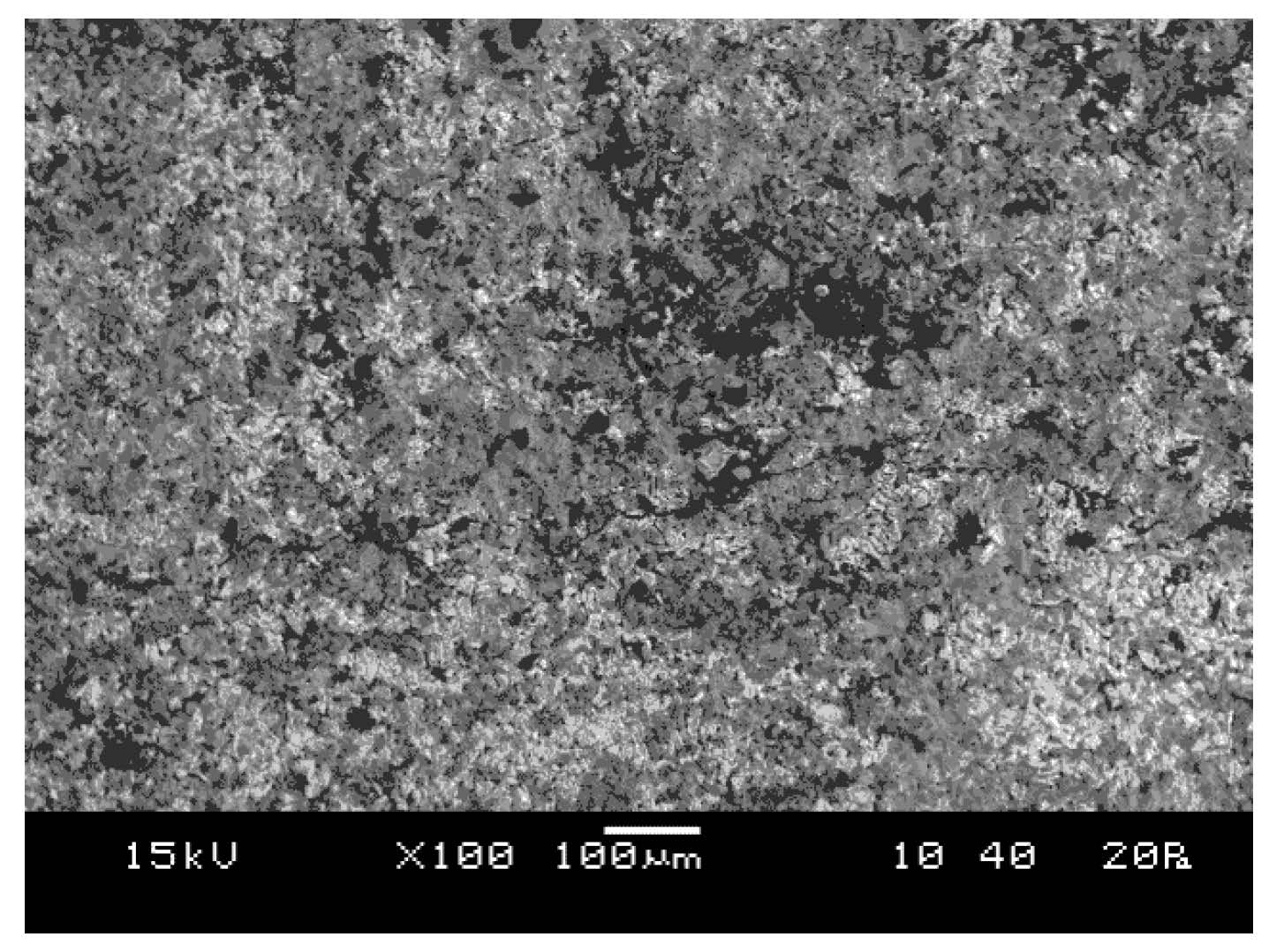
Figure 3.
SEM image of wheel surface (a); elemental analysis of composition along the red line and their mapping (b–d): (b) carbon (diamond); (c) aluminum; (d) silicon
Figure 3.
SEM image of wheel surface (a); elemental analysis of composition along the red line and their mapping (b–d): (b) carbon (diamond); (c) aluminum; (d) silicon
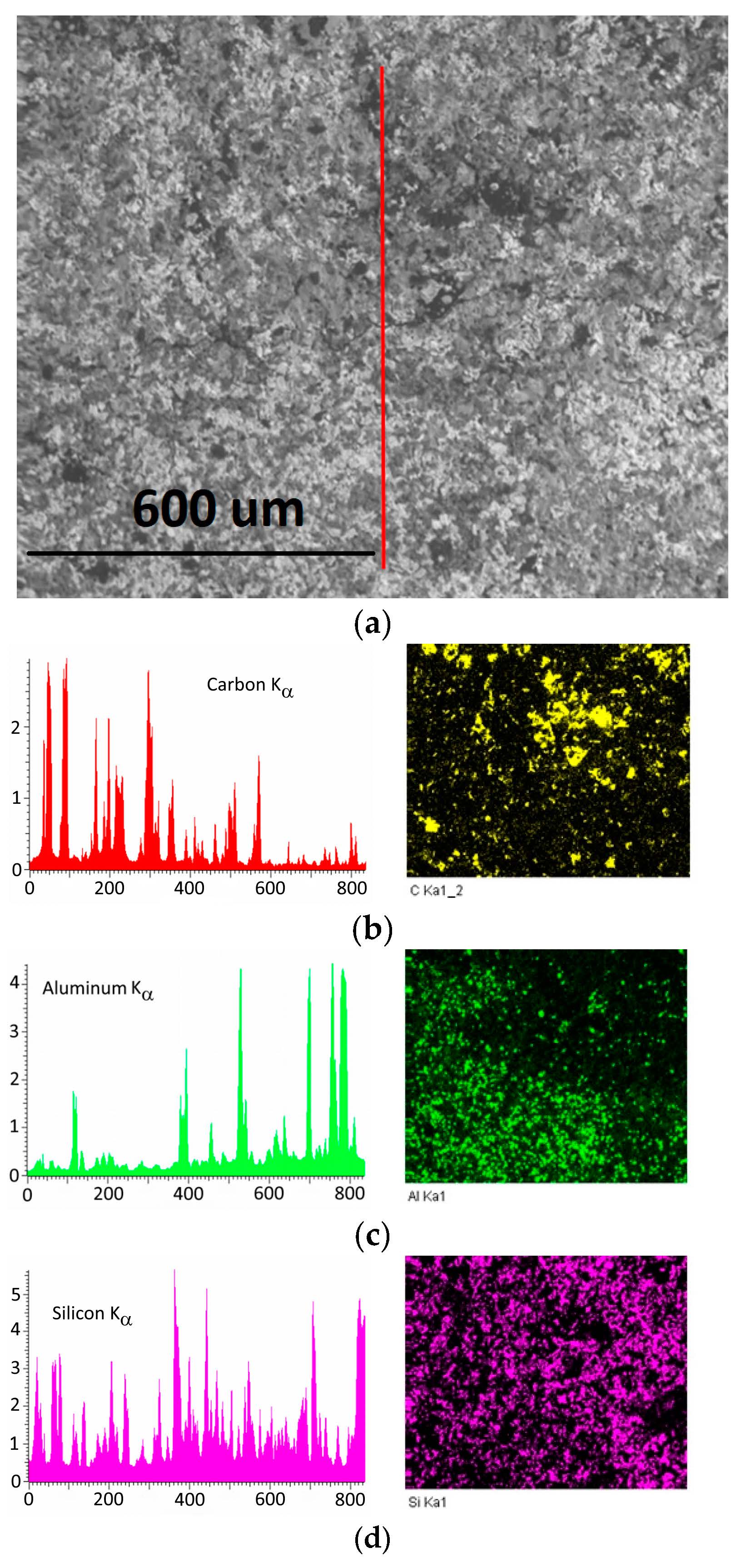
Table 1.
Relative comparison of properties of materials used for grinding wheel bodies (Swaty Comet 2014)
Table 1.
Relative comparison of properties of materials used for grinding wheel bodies (Swaty Comet 2014)
Material | Designation | Vibration Damping | Thermal Conductivity | Mechanical Strength |
---|---|---|---|---|
sintered alumina | I | x x x | x x x | x x x |
duralumin | A | x x | x x x x | x x x x |
bakelite | B | x x x x | x | x x |
steel | J | x | x x x x | x x x x |
ceramic abrasive sinter | K | x x x | x x x | x x x |
x—Less pronounced of property; x x x—Well pronounced of property.
Table 2.
Results of mechanical properties tests of ceramic supporting bodies
Designation | Average Supporting Body Hardness [HRB] | Average Ceramic Diamond Ring Hardness [HRB] | Average Bending Strength of the Body [MPa] |
---|---|---|---|
1A135x5x5x5x10D76EA+SZ s.40 | 72.5 ±2 | 77 ±2 | 84 ±2 |
1A135x5x5x5x10D76EA+SZ s.40 | 74.0 ±1 | 78 ±2 | 86 ±2 |
1A135x5x5x5x10D76EA+SZ s.42 | 73.0 ±2 | 79 ±2 | 84 ±2 |
1A135x5x5x5x10D76EA+SZ s.42 | 72.5 ±2 | 77 ±1 | 85 ±1 |
1A1 type of wheels shape (peripheral shape); 35x5x5x5x10—wheels dimensions; D76—granulation of diamond grain; EA+SZ s.40—type of modification.
Table 3.
Test parameters
Parameter | Value |
---|---|
Wheel circumferential velocity | 18.22 m/s |
Work piece peripheral speed | 250 rpm |
Longitudinal displacement speed | 5 m/min |
Grinding depth in single pass | 0.01 mm |
Cooling | flooding method (GRINDIX coolant) |
Table 4.
Results of exploitation tests of grinding wheels
Designation | Circumferential Speed of Grinding Wheel [m/s] | Loss on Grinding Wheel Diameter R [mm] | Relative Wear [mg/g] |
---|---|---|---|
1A1 35x5x5x10 D76, EA+SZ 100 V | 18.00 | −0.01 ±0.002 | 1.570 |
1A1 35x5x5x10 D76, EA+SZ 100 V | 22.00 | −0.02 ±0.002 | 2.873 |
1A1 35x5x5x10 D76, 100 V | 18.00 | −0.015 ±0.003 | 2.156 |
1A1 35x5x5x10, D76, 100 V | 22.00 | −0.025 ±0.003 | 3.594 |
© 2020 Open Access. This article is distributed under the terms of the Creative Commons Attribution-ShareAlike 3.0 (CC BY-SA 3.0).