J_Appl_Mater_Eng 2021, 60(2–3), 53-69; doi:10.35995/jame60020005
Spark Plasma Sintering/Field Assisted Sintering Technique as a Universal Method for the Synthesis, Densification and Bonding Processes for Metal, Ceramic and Composite Materials
Łukasiewicz Research Network—Krakow Institute of Technology, Zakopiańska 73, 30-418 Krakow, Poland; piotr.putyra@kit.lukasiewicz.gov.pl (P.P.); piotr.klimczyk@kit.lukasiewicz.gov.pl (P.K.); marcin.podsiadlo@kit.lukasiewicz.gov.pl (M.P.); kinga.bednarczyk@kit.lukasiewicz.gov.pl (K.B.)
*
Corresponding author: jolanta.laszkiewicz@kit.lukasiewicz.gov.pl
How to cite: Laszkiewicz-Łukasik, J.; Putyra, P.; Klimczyk, P.; Podsiadło, M.; Bednarczyk, K. Spark Plasma Sintering/Field Assisted Sintering Technique as a Universal Method for the Synthesis, Densification and Bonding Processes for Metal, Ceramic and Composite Materials. J. Appl. Mater. Eng. 2020, 60(2–3), 53–69, doi:10.35995/jame60020005.
Received: 26 November 2020 / Accepted: 25 January 2021 / Published: 28 January 2021
Abstract
:This paper presents the technology of powder sintering by the spark plasma sintering method, also known as the field assisted sintering technique. The mechanisms, compared to other sintering techniques, advantages of this system, applied modifications and the history of the development of this technique are presented. Spark Plasma Sintering (SPS) uses uniaxial pressing and pulses of electric current. The direct flow of current through the sintered material allows high heating rates to be reached. This has a positive effect on material compaction and prevents the grain growth of sintered compact. The SPS mechanism is based on high-energy spark discharges. A low-voltage current pulse increases the kinetics of diffusion processes. The SPS temperature is up to 500 °C lower than the sintering temperature using conventional methods. The phenomena that occur during sintering with the Field Assisted Sintering Technology (FAST)/SPS method give great results for consolidating all types of materials, including those which are nonconductive. This method is used, among others, in relation to metals, alloys and ceramics, including advanced and ultra-high-temperature ceramics. Due to the good results and universality of this method, in recent years it has been developed and often used in research institutions, but also in industry.
Keywords:
spark plasma sintering; field assisted sintering technique; sintering; SPS; FAST; flash sintering; FSPS1. Introduction
The progress in advanced industries requires new, “perfect” materials. There is a demand for materials which are able to work under specific conditions such as very high temperatures or in particularly aggressive environments. This demand opens up many new opportunities and provides a challenge for scientists to obtain new durable materials. There are many methods of manufacturing and for the consolidation of materials. The powder sintering technology, however, allows the obtention of materials with specific designed microstructures and compositions with widely changing properties depending on the used technique and its parameters. Various powder sintering techniques have been used successfully to consolidate both metals and ceramic materials. Despite sintering being a mature method of material manufacturing known for thousands of years (it is known that the first ceramic products were made by humans over 25,000 years ago), the most significant progress in sintering methods started with the development of the pressure assisted technology. Then, the application of a current and electromagnetic field (microwave sintering, spark plasma sintering) turned out to be the milestone in powder sintering techniques (Biesuz et al. 2020). Among all the sintering methods, the spark plasma sintering technique, also known as the field assisted sintering technique, deserves special attention.
The Field Assisted Sintering Technology (FAST)/Spark Plasma Sintering (SPS) technique uses a combination of uniaxial external pressure and electric current in order to rapidly sinter a wide range of powders. This manufacturing method allows higher heating rates (up to 1000 °C/min) and shorter holding times to be reached compared with conventional sintering techniques, which is undeniably one of the greatest advantages of the FAST/SPS method (Hu et al. 2020). It was found that high heating rates can suppress the grain growth in the sample (Liu et al. 2014). For this reason, the SPS technique can be successfully used to produce nanostructured materials (Wei et al. 2014; Nygren 2007). The FAST/SPS method extends the possibility of manufacturing and modifying a wide range of traditional materials, including metals, ceramics, alloys and various types of composites, and even nonconductive materials. In addition, spark plasma sintering offers an opportunity to manufacture hard-to-sinter materials such as refractory materials (Abe et al. 2020) or high-entropy alloys (HEAs) that are a new type of advanced material which consist of five or more elements (Hu et al. 2020). Peng et al. investigated and compared mechanical properties and microstructures of HEAs (FeCoCrNi-Mo) prepared by vacuum hot-pressing (VHP) sintering and spark plasma sintering (SPS). The SPS method allowed the reduction in sintering time by 207 min and sintering temperature by 250 °C compared to VHP sintering. Moreover, the microstructure of the sample obtained by SPS was uniform, while the VHP sintering resulted in the appearance of new phases due to the higher temperature and longer sintering time (Peng et al. 2020). The FAST/SPS process can be also used to sinter transparent ceramics (Xiao et al. 2020), carbon-containing materials and nonequilibrium or metastable phases (Fong et al. 2014; Suffner et al. 2010). This technique is also used for cross-linking polymers, crystallisation and synthesis of materials, but also in the diffusion bonding processes in the solid phase, or modification of surface layers (Omori 2000; Kessel 2009).
To date, many modifications of the FAST/SPS process and devices have been applied to meet the challenges of the fast-growing industry. In a recent study (Balima et al. 2018), an innovative Hot Pressing (HP)-SPS-Belt equipment was designed. The new system with a large volume chamber is able to reach pressures up to 6 GPa. Giuntini et al. developed free pressure-less SPS. The process was conducted with a T-shaped graphite punch which was stopped by the top surface of the graphite die; thus, the sample had a load-free status (Giuntini et al. 2013).
The FAST/SPS technique is a complex, multiphysical method of material manufacturing that combines several fields of science and requires a deep and detailed understanding of the mechanism and phenomena that occur during sintering. Although the existence of plasma during FAST/SPS processes is still controversial and has never been confirmed, the technique is extremely effective for almost all materials, making it extremely versatile.
The aim of this review is to summarise the principal knowledge about the history and development of the FAST/SPS technique, fundamental mechanisms responsible for powder sintering and, finally, some interesting modifications that have already been applied to the SPS method.
2. Sintering of Materials
Sintering of ceramic and metallic powders is a phenomenon that occurs spontaneously with increasing temperature. As a result of the heating, after reaching the temperature in the range from 0.4 to 0.8 of the melting point, formation of necks, pore reduction and powder consolidation occur. The connection of powder grains is accompanied by the contraction of the entire system and the loose or weakly bound powder transition into a solid polycrystal. These changes are the result of mass transfer processes, initially moving particles against each other, and then moving the individual atoms. At lower temperatures, mass transport is a result of diffusion along the grain boundaries and surface diffusion. At the highest temperature, mass transport takes place due to volumetric diffusion, as well as evaporation and condensation (Figure 1).
These processes require both a high temperature and appropriate time. The value of these parameters strongly depends on the sintered material, its melting point or the type of atomic bonds. The sintering process is also determined by the pressing force, atmosphere used (e.g., argon, nitrogen, vacuum), powder particle size and the method of their initial preparation. The intensification of diffusion processes, and thus the shortening of the sintering duration, can be achieved by using devices that enable the generation of an appropriate pressing force, as well as heating due to the current pulse flowing directly through the sintered sample (Putyra et al. 2015; Lis and Pampuch 2000; Oczoś 1996).
2.1. Spark Plasma Sintering/Field Assisted Sintering
2.1.1. FAST/SPS—Characteristics of the Technique
Spark plasma sintering, also called the field assisted sintering technique or Puls Electric Current Sintering (PECS), is a sintering technique using uniaxial pressing and electric current pulses. The direct current that flows through the sintered material, allows high heating rates to be reached. This has a positive effect on material compaction and prevents the sinter grains growth. The SPS sintering mechanism is based on high-energy spark discharges. A low-voltage current pulse increases the kinetics of diffusion processes.
There are several names for this method in the literature. In addition to SPS, it is also called Plasma Assisted Sintering (PAS) and FAST (Field Assisted Sintering Technology). Moreover, the Pulse Plasma Sintering (PPS) method is common, which is characterised by similar phenomena as in the above-mentioned methods, but as it was reported (Michalski and Siemiaszko 2006), the power of the pulse is higher in the PPS method. The literature also proposes the name spark plasma system because these devices are used not only for sintering, but for cross-linking polymers, bonding metals, crystallisation and synthesis of materials. However, the acronym SPS is the most often used for this method.
Currently, the SPS mechanism is explained by discharges arising in the spaces between the sintered powder particles, causing local temperature increases, powder surface melting and neck formation. After creating the neck, resistance heating occurs as a result of the current flow through a conductor with a small cross-section (Figure 2). Spark discharges lead to the elimination of adsorbed gases and oxides from the surface of the particles, thus increasing the formation of active contacts, which results in a reduction in the temperature and sintering time. During the process, crystallisation and chemical reactions may take place, leading to new compound formations (Jaworska et al. 2013; Michalski and Siemiaszko 2006).
The SPS temperature is up to 500 °C lower than the sintering temperature used in conventional sintering methods. Evaporation, melting and sintering between the powder particles takes place in a few to several dozen minutes, including the heating time and holding at the sintering temperature (Somiya and Tokita 2013; Groza and Zavaliangos 2000; Suárez et al. 2013; Raichenko et al. 1976; Conrad 2002).
The SPS technique is characterised by direct heating of the sintered material as a result of the current flow; thus, it has a high heating rate compared to traditional HP (hot pressing) and Hot Isostatic Pressing (HIP) processes. This is especially so when compared to the heating rates obtained during free sintering, or even microwave sintering (Figure 3). The heating rate in the SPS process depends on the geometry and type of graphite elements (i.e., grade, electrical resistance, thermal conductivity) and the electrical properties of the system: graphite elements and sintered material. The heating rate in the SPS process can reach 1000 °C/min. As a consequence, the duration of the sintering process using this method, depending on the material and dimensions of the element, may be from several to several dozen minutes (Suárez et al. 2013). In the HP or HIP methods, the material is heated by the thermal radiation of the heating element and convection, which is determined by the location of the graphite die with the sintered material (HP) and the sintered material (HIP) in relation to the heating elements (Figure 4). Additionally, the material is heated by heat transfer and conduction, which means that the heating rate is usually low, and the process may take several hours. Figure 5 shows programmed and real temperature curves, as well as the time needed to equalise the temperature between the set value and measured value in the HP and SPS processes.
It should be mentioned that in SPS processes, powder conductivity is highly important, as well as achieving a homogeneous current density and temperature distribution. In materials characterised by high electrical resistance, the current flows through the graphite set, which acts as a heating element located around the sintered material. The density of current flowing through the graphite elements and the sintered material, depending on its electrical conductivity, is shown in Figure 6. Significant parameters determining the temperature distribution inside the sample are the electrical conductivity of the sample material, the die wall thickness and the presence of additional graphite elements in the sintering insert (Zhang 2010; Anselmi-Tamburini et al. 2005; Vanmeensel et al. 2005). Graphite elements such as foil and washers are used to avoid direct contact between the punches, die and sample and to provide electrical contact between all parts of the system. Figure 7 shows the results of modelling (using the finite element method) the temperature distribution in the sintered material and in graphite elements, depending on the graphite materials with different geometries and electrical properties.
2.1.2. FAST/SPS Technique—History and Development
The development of sintering methods assisted with electric currents began in the 1930s. Initially, resistance sintering was utilised in the hot-pressing process. Then, spot welding equipment was introduced. The exploitation of an external electric current to assist sintering was initiated in 1933 by Taylor, who patented a device and a method combining resistance sintering and hot pressing of sintered carbides (Taylor 1932, 1933). In 1944, Cramer patented the method of resistance sintering for copper matrix materials (copper, brass, bronze) (Cremer 1944). In the 1960s, metal sintering processes were carried out with the assistance of an electrical discharges, using spot welding and metal welding devices (Inoue 1966). The 1970s was a period of development for Electric Discharge Compaction (EDC) and Electric Discharge Sintering (EDS) methods for metal powder sintering (Clyens and Al-Hassani 1976). In all the above-mentioned methods, the powder sintering process was carried out with heating due to Joule heat (resistance heating with flowing electric current) (Somiya 2013).
The SPS method was developed in Japan. In 1962, Dr. Kiyoshi Inoue of Japax Inc. elaborated the Spark Sintering (SS) method, which was then extended by introducing current pulses at the initial stage of heating. The second generation of powder consolidation equipment was developed in 1986 by Inoue-Japax Research Inc. and was called PAS (plasma assisted/activated sintering). Currently, the SPS method is recognised as the third generation (after SS and PAS) of such methods, initiated by Sumitomo Coal Mining Co., Ltd. (Japan) in 1989 (Somiya 2013; Somiya and Tokita 2013).
SPS devices can be used to consolidate conductive materials as well as materials with high electrical resistances. The development of both methods and devices for using impulse current enabled the consolidation of a wide range of metallic, ceramic and composite materials, also at an industrial scale. Currently, SPS devices are used not only in material sintering, but also in the processes of solid phase material diffusion bonding or surface layer modification. In the years 2000–2009, there was a tendency to use the SPS method in industrial production at small and medium-series scales. Process automation and the creation of industrial lines, which include, among others, devices with impulse heating systems, constitute the fourth generation of the SPS system. SPS devices adapted to other technologies, sometimes far away from the sintering process, which resulted in numerous research and industrial works being carried out in recent years; these can be thought of as the fifth generation of SPS technology. A chart showing the increase in the number of publications on SPS since 1994 is presented in Figure 8.
The powder consolidation methods of the second and third generations (PAS and SPS) differ mainly in the duration of the stage in which the pulse current is used to heat the material. In the PAS method, heating with an impulse current is carried out at the beginning of the process, and in the subsequent stages of sintering it is realised by applying a direct current (Figure 9a). In the SPS method, heating and sintering of the material is carried out as a result of the impulse current flow throughout the entire process (Figure 9b). Exemplary waveforms of impulse currents reported in the heating and sintering process using the FCT GmbH SPS apparatus are shown in Figure 10. Powder sintering in the SPS method is carried out in graphite dies, and the maximum pressure is determined by the compressive strength of the graphite elements forming the sintering inset. A diagram of the SPS device is shown in Figure 11. The initial pressing stage is carried out under vacuum conditions, which allows the removal of the gases from the powders. The protective gases (e.g., nitrogen or argon) can then be introduced into the chamber of the SPS device. The SPS HP D5 laboratory machine was manufactured by FCT, and the heating chamber and die elements are shown in Figure 12. In the FCT HP D5 device, the temperature is measured with a pyrometer, located in the axis of the upper pressing punch. The temperature is measured from the bottom of the upper graphite punch hole (2–3 mm from the sintered material surface), which substantially reduces the temperature difference between the sample and the measurement point. The influence of the pyrometer location on the temperature difference between the sample and measuring surface is shown in Figure 13.
Figure 14 shows the changes in temperature, pressing force, punch displacement and current voltage parameters during sintering with the SPS method. The SPS apparatus also enables monitoring of the material compaction during the processes. The change in sample height is determined by displacement of the pressing punch during heating and cooling. Due to this, it is possible to analyse the mechanisms of material compaction (Figure 15).
The Łukasiewicz—Krakow Institute of Technology possesses an SPS machine manufactured by an FCT System GmbH, model HP D5. This device is characterised by a maximum sintering temperature of 2400 °C, pulse duration in the range of 1 to 255 ms and an additional option to regulate the time interval between the pulses as well as between the group of pulses. The pressing force can achieve values in the range of 3–50 kN and the maximum force is defined by the graphite element’s strength. Additionally, the SPS machine is equipped with a hermetic chamber that enables the performance of the process with vacuum conditions (50 Pa) or to provide a protective atmosphere (argon, nitrogen). Moreover, the control system offers heating rate regulation ranging from 5 to 400 °C/min.
The HP D5 device can be used for the sintering of various metallic, ceramic and composite materials—in particular, the so-called advanced ceramics, including ceramic composites reinforced with diamond and cubic boron nitride (cBN) (Klimczyk et al. 2016; 2020). Diamond and cubic boron nitride belong to the category of superhard materials and have a wide range of applications due to their unique properties, especially such as very high hardness and wear resistance. Sintered polycrystalline diamond (PCD) and polycrystalline cubic boron nitride (PcBN) as well as a number of composites based on diamond and cBN are used as cutting tools for difficult-to-machine materials. Both diamond and cBN are metastable phases and therefore need high-pressure/high-temperature (HPHT) conditions for sintering, where a pressure in the range of 5 to 8 GPa and a temperature of 1300 to 2200 °C are achieved. HPHT sintering methods are rather expensive and low in efficiency because of their general complexity and the time-consuming process of assembly before sintering. The densification of diamond/cBN-containing composites at moderate pressures of up to 100 MPa is advantageous, especially from technical and economical perspectives. The SPS method, due to direct resistance heating, moderate pressure application and possible plasma generation, enhances sintering kinetics and facilitates the formation of a new class of composites reinforced with superhard particles without the use of ultrahigh pressure.
The sintering behaviour and mechanical properties of Al2O3-based matrix composites reinforced with up to 30 vol.% of diamond and cBN were investigated. Additionally, pure Al2O3 powder was treated separately under identical SPS conditions for the purpose of comparison. The sintering behaviour of the composites is different than that of the Al2O3 matrix sintered separately. The Young’s modulus of Al2O3 increases with temperature up to a specific value and does not change thereafter. The composites attain maximum values of density and Young’s modulus around the sintering temperature of 1300–1400 °C. This difference can be explained by the cubic to hexagonal phase transitions. During SPS, two opposing processes occur: densification of the material (increase in density and Young’s modulus), and diamond/cBN → graphite/hexagonal boron nitride (hBN) transformation at higher temperatures (reduction in density and Young’s modulus). The best composites reinforced with diamond have high relative densities (99%), and moderate Young’s modulus (74% of theoretical value); nevertheless, the hardness and fracture toughness of these sinters are too low in relation to the values assumed. Notably, good improvements in fracture toughness, of about 1.5 MPa∙m1/2 on average over that of Al2O3, are observed in the case of composites sintered with cBN. Crack deflection on cBN grains is identified as the main toughening mechanism of the materials investigated (Klimczyk et al. 2020).
2.1.3. Flash SPS Sintering (FSPS)—Modifications of SPS Technique
Despite the SPS technology being a well-known method that ensures great results both in process parameters (sintering time reduction and lowering sintering temperature) and material properties, some improvements are still being developed. One of the most promising routes for further SPS evolution is a sintering method called Flash SPS (FSPS), which is a combination of the standard SPS method and flash sintering.
Flash sintering itself (without SPS), as a novel method based on applying an electric field to a conventionally heated sample, allows the reduction in the time and temperature required to sinter ceramic materials. The sample, initially nonconductive, is heated by radiation in a conventional furnace. At the same time, an electric field is applied through the electrodes (usually highly conductive metal), forcing a current flow in the ceramic body. During the so-called “flash event”, rapid densification takes place as well as a sudden sample resistance drop and thermal runaway of internally generated Joule heat. It is possible to obtain almost a fully dense body while flash sintering in only a few seconds. Moreover, this process enables one to achieve metastable phases and produce ceramics with nanometric grains (Biesuz and Sglavo 2019; Biesuz et al. 2020). Since flash sintering has been shown to be a promising densification method, some developments have been made. One of the most important is a combination of flash and SPS techniques, which involves a flash event (rapid densification, resistance decrease and Joule heat generation) provided in SPS machines. This combination enables the extension of classic flash sintering configurations by the assistance of external pressure, which enhances the densification process. Main limitations for FSPS are related to SPS machine outputs, generally limited to 10 V. Consequently, only highly conductive materials can be sintered using FSPS techniques, which result in the necessity to adapt SPS devices to high voltages (Biesuz et al. 2020).
To date, some configurations have already been developed for carrying out FSPS processes. Die isolated from punches or die-less configurations (Figure 16a,b) can be implemented if the material is conductive sufficiently at room temperature to sustain current flow. In this particular case, the ceramic sample is sintered by forcing all (or most) of the electric current to flow through the sample, causing a flash event to occur, contrariwise to conventional SPS, where a significant part of the current flows through the graphite die, resulting in heat generation both in the sample and the die. If preheating is necessary to increase conductivity, a sacrificial metal tube or graphite felt can be applied (Figure 16c) (Olevsky et al. 2016; Biesuz et al. 2020). In a recent study (Olevsky et al. 2016), copper collar was used as a heating element—at the initial stage, an electric current was applied only to the collar, leading to copper temperature growth by resistant heating, thus heating the ceramic sample by radiation. Then, after reaching the melting point, the copper collar slumped downwards, allowing SPS punches to come into contact with the ceramic sample, thus flowing all the current through the ceramic body, causing rapid heating by Joule heat generation and, consequently, powder densification.
Although flash sintering and Flash SPS are considered as innovative methods leading to extremely desirable process parameters and material properties, a more detailed understanding of the “flash event” phenomenon is still required.
3. Summary
In summary, the SPS equipment allows the sintering of a wide variety of materials and operations at lower temperatures and pressures compared to the free sinter or conventional HP (hot pressing) process. It affects the reduction in grain growth by shortening the sintering process time. In addition, it enables materials to be shaped without prepressing, isostatic densification and drying. Moreover, it allows the visualisation of changes in the sintering process parameters (temperature, time, heating and cooling rates, pressure force) and the visualisation of changes in the resistance of the sintered material. This technique is used to produce and shape a wide range of materials: metallic, composites and ceramics, including superhard materials. Furthermore, spark plasma sintering is a modern method that enables the simultaneous performance of syntheses with the features of self-developing high-temperature synthesis (SHS) and the densification of the produced materials. The phenomena accompanying the SPS processes favours the formation of new compounds and also contributes to the reduction in the sintering temperature required to obtain a material with a high relative density.
Author Contributions
Conceptualisation, J.L.-Ł. and P.P.; Methodology, J.L.-Ł. and P.P.; Validation, P.K.; Formal Analysis, P.K.; Investigation, M.P.; Resources, J.L.-Ł., P.P. and P.K.; Data Curation, J.L.-Ł., P.P. and P.K.; Writing—Original Draft Preparation, J.L.-Ł., P.P. and K.B.; Writing—Review and Editing, J.L.-Ł. and P.K.; Visualisation, P.P.; Supervision, P.P. and P.K.; Project Administration, P.P.; Funding Acquisition, P.P.
Funding
This work was carried out in the Łukasiewicz Research Network—Krakow Institute of Technology, under the following project supported by the Ministry of Science and Higher Education of Poland (subvention): “Preparation of ceramic composites with the strengthening phase in the form of diamond nanostructures using HPHT method” (Project No. DS 4402/1031). The results presented were also partially achieved within the DURACER project, entitled “Durable ceramic composites with super-hard particles for wear-resistant cutting tools”, cofounded by the Polish National Centre for Research and Development within the framework of the M-ERA.NET programme (Agreement No. M-ERA.NET2/2017/1/2018).
Conflicts of Interest
The authors declare no conflict of interest. The funders had no role in the design of the study; in the collection, analyses, or interpretation of data; in the writing of the manuscript, or in the decision to publish the results.
References
- Abe, J. O.; Popoola, A. P. I.; Popoola, O. M. Consolidation of Ti6Al4V Alloy and Refractory Nitride Nanoparticles by Spark Plasma Sintering Method: Microstructure, Mechanical, Corrosion and Oxidation Characteristics. Materials Science and Engineering A 2020, 774(January), 138920. [Google Scholar] [CrossRef]
- Anselmi-Tamburini, U.; Gennari, S.; Garay, J. E.; Munir, Z. A. Fundamental Investigations on the Spark Plasma Sintering/synthesis Process. Materials Science and Engineering: A 2005, 394(1–2), 139–48. [Google Scholar] [CrossRef]
- Balima, Félix; Bellin, Federico; Michau, Dominique; Viraphong, Oudomsack; Poulon-Quintin, Angéline; Chung, U. Chan; Dourfaye, Alfazazi; Largeteau, Alain. High Pressure Pulsed Electric Current Activated Equipment (HP-SPS) for Material Processing. Materials and Design 2018, 139, 541–8. [Google Scholar] [CrossRef]
- Biesuz, Mattia; Sglavo, Vincenzo M. Flash Sintering of Ceramics. Journal of the European Ceramic Society 2019, 39(2–3), 115–43. [Google Scholar] [CrossRef]
- Biesuz, Mattia; Grasso, Salvatore; Sglavo, Vincenzo M. What’s New in Ceramics Sintering? A Short Report on the Latest Trends and Future Prospects. Current Opinion in Solid State and Materials Science 2020, 24(5), 100868. [Google Scholar] [CrossRef]
- Clyens, S.; Al-Hassani, S. T. S. The Compaction of Powder Metallurgy Bars Using High Voltage Electrical Discharges. International Journal of Mechanical Sciences 1976, 18(1), 37–40. [Google Scholar] [CrossRef]
- Conrad, H. Thermally Activated Plastic Flow of Metals and Ceramics with an Electric Field or Current. Materials Science and Engineering 2002, 322(1–2), 100–7. [Google Scholar] [CrossRef]
- Cremer, G. D. Sintering Together Powders Metals Such as Bronze, Brass or Aluminum. U.S. Patent 2,355,954, 15 August 1944. [Google Scholar]
- Ertug, B. (Ed.) Sintering Applications; InTech: Croatia, 2013. [Google Scholar] [CrossRef]
- Fong, A. Y.; Xu, H.; Page, K.; Dirmyer, M. R.; Kodera, Y.; Obrey, S. J.; Garay, J. E. Synthesis and Structural Characterization of Dense Polycrystalline Mg9Sn5, a Metastable Mg-Sn Phase. Journal of Alloys and Compounds 2014, 616, 333–9. [Google Scholar] [CrossRef]
- Giuntini, Diletta; Wei, Xialu; Maximenko, Andrey L.; Wei, Li; Ilyina, Alexandra M.; Olevsky, Eugene A. Initial Stage of Free Pressureless Spark-Plasma Sintering of Vanadium Carbide: Determination of Surface Diffusion Parameters. International Journal of Refractory Metals and Hard Materials 2013, 41, 501–6. [Google Scholar] [CrossRef]
- Groza, Joanna R.; Zavaliangos, Antonios. Sintering Activation by External Electrical Field. Materials Science and Engineering: A 2000, 287(2), 171–7. [Google Scholar] [CrossRef]
- Hu, Zheng Yang; Zhang, Zhao Hui; Cheng, Xing Wang; Wang, Fu Chi; Zhang, Yi Fan; Li, Sheng Lin. A Review of Multi-Physical Fields Induced Phenomena and Effects in Spark Plasma Sintering: Fundamentals and Applications. Materials and Design 2020, 191, 108662. [Google Scholar] [CrossRef]
- Inoue, K. Electric-Discharge Sintering. U.S. Patent 3,241,956 A, 22 March 1966. [Google Scholar]
- Jaworska, Lucyna; Putyra, Piotr; Wyżga, Piotr; Figiel, Paweł. Nowoczesne metody spiekania. Annales Iniversitatis Paedagogicae Cracoviensis 2013, 6, 35–40. [Google Scholar]
- Kessel, H. U. Sintered Materials on the Way to Production by Means of Modern SPS Technologies. Ceramic Forum International Berichte Der Deutschen Keramischen Gesellschaft 2009, 10, 145–52. [Google Scholar]
- Klimczyk, Piotr; Cura, M. E.; Vlaicu, A. M.; Mercioniu, I.; Wyżga, Piotr; Jaworska, Lucyna; Hannula, S.-P. Al2O3-cBN Composites Sintered by SPS and HPHT Methods. Journal of the European Ceramic Society 2016, 36(7), 1783–89. [Google Scholar] [CrossRef]
- Klimczyk, Piotr; Wyżga, Piotr; Cyboroń, Jolanta; Laszkiewicz-Łukasik, Jolanta; Podsiadło, Marcin; Cygan, Sławomir; Jaworska, Lucyna. Phase Stability and Mechanical Properties of Al2O3-cBN Composites Prepared via Spark Plasma Sintering. Diamond and Related Materials 2020, 104(April), 107762. [Google Scholar] [CrossRef]
- Lis, Jerzy; Pampuch, Roman. Spiekanie; Wydawnictwa AGH: Kraków, 2000. [Google Scholar]
- Liu, Jianghao; Fu, Zhengyi; Wang, Weimin; Zhang, Jinyong; Wang, Hao; Wang, Yucheng; Lee, Soowohn; Niihara, Koichi. Ultra-High Heating Rate Densification of Nanocrystalline Magnesia at High Pressure and Investigation on Densification Mechanisms. Journal of the European Ceramic Society 2014, 34(12), 3095–102. [Google Scholar] [CrossRef]
- Michalski, Andrzej; Siemiaszko, Dariusz. Impulsowo plazmowe spiekanie nanokrystalicznych węglików WC-12Co. Inżynieria Materiałowa 2006, 3, 629–31. [Google Scholar]
- Nygren, M. SPS Processing of Nano-Structured Ceramics. Journal of Iron and Steel Research International 2007, 14 5 Suppl. 1, 99–103. [Google Scholar] [CrossRef]
- Oczoś, Kazimierz. Kształtowanie ceramicznych materiałów technicznych; Oficyna Wydawnicza Politechniki Rzeszowskiej: Rzeszów, 1996. [Google Scholar]
- Olevsky, Eugene A.; Rolfing, Stephen M.; Maximenko, Andrey L. Flash (Ultra-Rapid) Spark-Plasma Sintering of Silicon Carbide. Scientific Report 2016, 6, 33408. [Google Scholar] [CrossRef]
- Omori, M. Sintering, Consolidation, Reaction and Crystal Growth by the Spark Plasma System (SPS). Materials Science and Engineering 2000, A287, 183–8. [Google Scholar] [CrossRef]
- Peng, Y. B.; Zhang, W.; Mei, X. L.; Wang, H. J.; Zhang, M. Y.; Wang, L.; Li, X. F.; Hu, Y. Microstructures and Mechanical Properties of FeCoCrNi-Mo High Entropy Alloys Prepared by Spark Plasma Sintering and Vacuum Hot-Pressed Sintering. Materials Today Communications 2020, 24(February). [Google Scholar] [CrossRef]
- Putyra, Piotr; Jaworska, Lucyna; Podsiadło, Marcin; Laszkiewicz-Łukasik, Jolanta. Materiały ceramiczne spiekane metodą SPS. Materiały Kompozytowe 2015, 4, 42–46. [Google Scholar]
- Raichenko, A. I.; Burenkov, G. L.; Leshchinsky, V. I. Theoretical Analysis of the Elementary Act of Electric Discharge Sintering. Physics of Sintering 1976, 5(2), 215–25. [Google Scholar]
- Somiya, Shigeyuki. Handbook of Advanced Ceramics: Materials, Applications, Processing, and Properties, 2nd ed.; Elsevier, Academic Press: Waltham, Oxford, Amsterdam, 2013. [Google Scholar]
- Somiya, Shigeyuki; Tokita, Masao. Chapter 11.2.3: Spark Plasma Sintering (SPS) Method, Systems, and Applications. In Handbook of Advanced Ceramics; Elsevier, Academic Press: Waltham, Oxford, Amsterdam, 2013; pp. 1149–77. [Google Scholar] [CrossRef]
- Suárez, M.; Fernández, A.; Menéndez, J. L.; Torrecillas, R.; Kessel, H. U.; Hennicke, J.; Kirchner, R.; Kessel, T. Chapter 13: Challenges and Opportunities for Spark Plasma Sintering: A Key Technology for a New Generation of Materials. In Sintering Applications; Ertuğ, Burcu, Ed.; InTech: Croatia, 2013. [Google Scholar] [CrossRef]
- Suffner, J.; Wang, D.; Hahn, H. Enhancing Superplasticity of ZrO2 (Y2O3)-Al2O3 Composites Prepared by Spark Plasma Sintering of Metastable Powders. Materials Science and Engineering A 2010, 527(29–30), 7885–92. [Google Scholar] [CrossRef]
- Taylor, G. F. Improvements in and Relating to Methods of and Apparatus for Producing Hard Metal Compositions. GB Patent No. 385629, 1932. [Google Scholar]
- Taylor, G. F. Apparatus for Making Hard Metal Compositions. U.S. Patent 1,896,854, 7 February 1933. [Google Scholar]
- Vanmeensel, K.; Laptev, A.; Hennicke, J.; Vleugels, J.; Vanderbiest, O. Modelling of the Temperature Distribution during Field Assisted Sintering. Acta Materialia 2005, 53(16), 4379–88. [Google Scholar] [CrossRef]
- Web of Science. n.d. Available online: https://apps.webofknowledge.com/summary.do?product=WOS&search_mode=GeneralSearch&qid=5&SID=R1miR8IcLkJ99i7kyhj (accessed on 27 November 2020).
- Wei, Kaya; Martin, Joshua; Nolas, George S. Synthesis, SPS Processing and Low Temperature Transport Properties of Polycrystalline FeSb2 with Nano-Scale Grains. Materials Letters 2014, 122, 289–91. [Google Scholar] [CrossRef]
- Xiao, Zhuohao; Yu, Shijin; Li, Yueming; Ruan, Shuangchen; Kong, Ling Bing; Huang, Qing; Huang, Zhengren; Zhou, Kun; Su, Haibin; Yao, Zhengjun; et al. Materials Development and Potential Applications of Transparent Ceramics: A Review. Materials Science and Engineering R: Reports 2020, 139, 100518. [Google Scholar] [CrossRef]
- Zhang, Jing. Field Activated Sintering Technology: Multi-Physics Phenomena Modeling; Lambert Academic Publishing AG & Co: Saarbrücken, 2010. [Google Scholar]
Figure 1.
Model of mass transport during sintering in the two-grain system (Oczoś 1996)
Figure 1.
Model of mass transport during sintering in the two-grain system (Oczoś 1996)
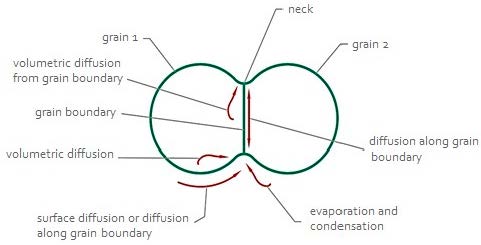
Figure 2.
Diagram of the current flow during Spark Plasma Sintering (SPS) method
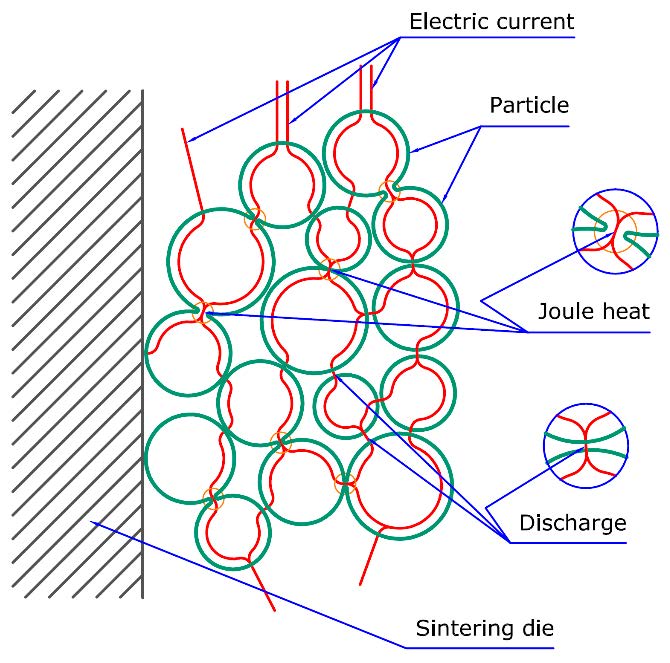
Figure 3.
Comparison of the heating rate and duration of the sintering process of ceramics with the Al2O3 matrix sintered by SPS, microwave and free sintering (Putyra et al. 2015)
Figure 3.
Comparison of the heating rate and duration of the sintering process of ceramics with the Al2O3 matrix sintered by SPS, microwave and free sintering (Putyra et al. 2015)
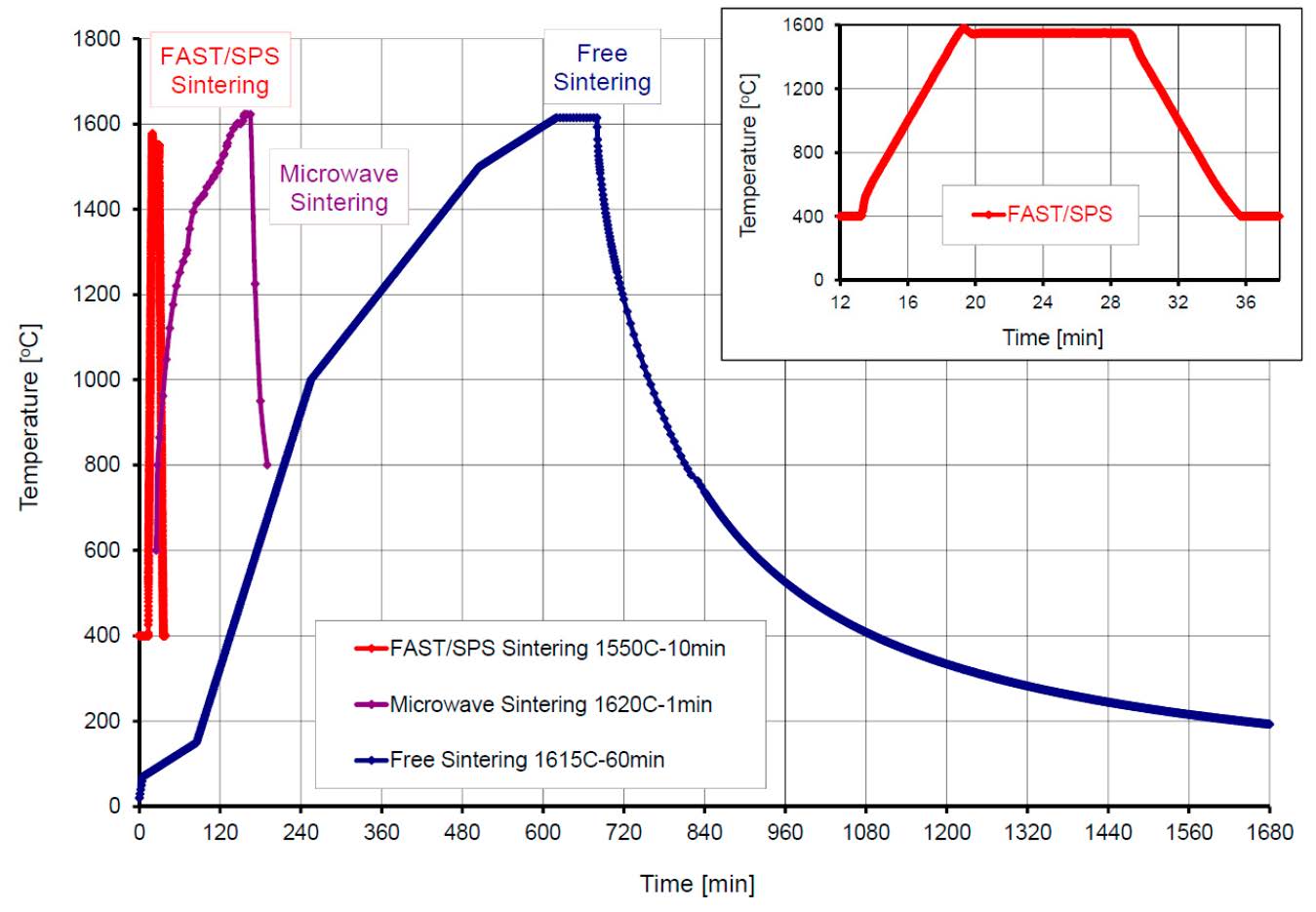
Figure 4.
Scheme of hot pressing (HP) (a) and SPS (b) methods (Suárez et al. 2013)
Figure 4.
Scheme of hot pressing (HP) (a) and SPS (b) methods (Suárez et al. 2013)
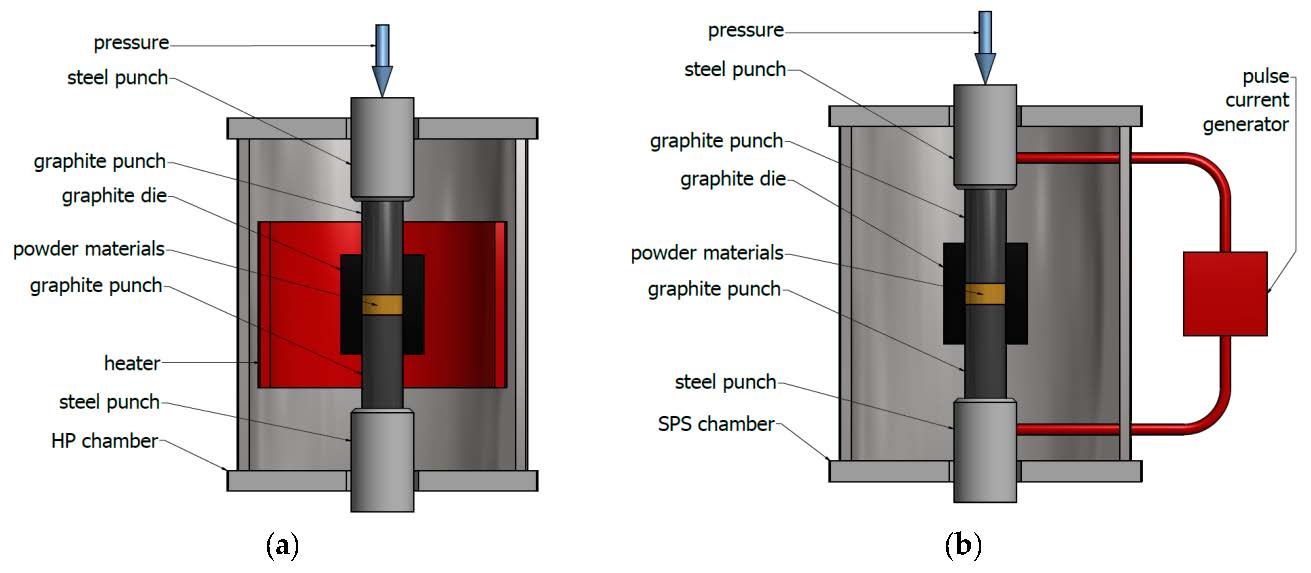
Figure 5.
Difference (ΔT) between set temperature (TA) and the measured temperature (TI), and the time (t *) needed to equalise the temperature in the processes: (a) hot pressing (HP); (b) SPS sintering (Kessel 2009)
Figure 5.
Difference (ΔT) between set temperature (TA) and the measured temperature (TI), and the time (t *) needed to equalise the temperature in the processes: (a) hot pressing (HP); (b) SPS sintering (Kessel 2009)
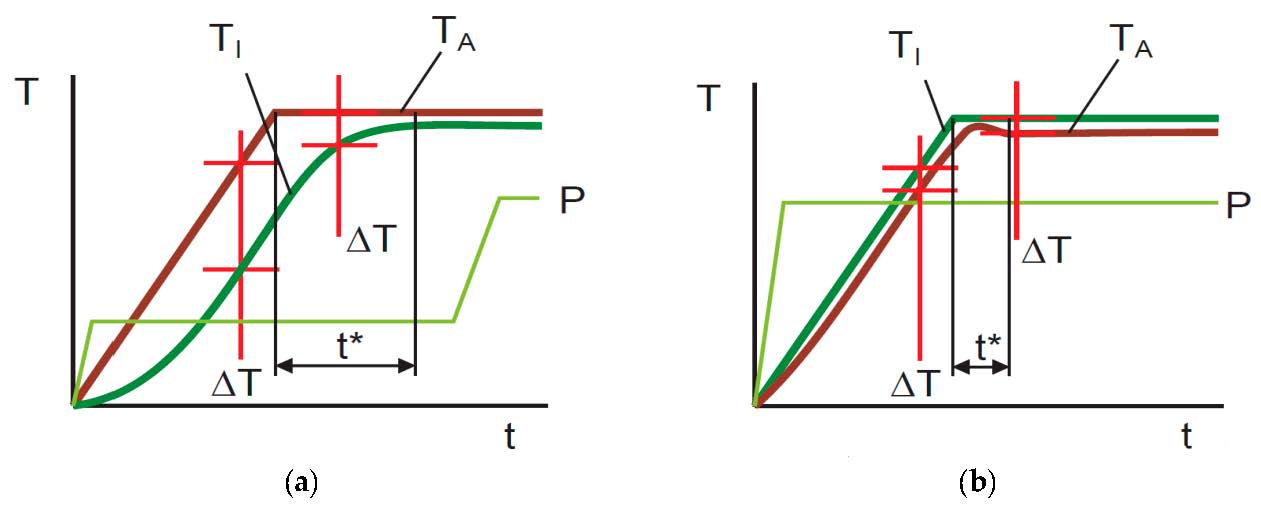
Figure 6.
Current flow during SPS heating, depending on the electrical conductivity of the sintered material: (a) Al2O3; (b) Cu (Anselmi-Tamburini et al. 2005)
Figure 6.
Current flow during SPS heating, depending on the electrical conductivity of the sintered material: (a) Al2O3; (b) Cu (Anselmi-Tamburini et al. 2005)
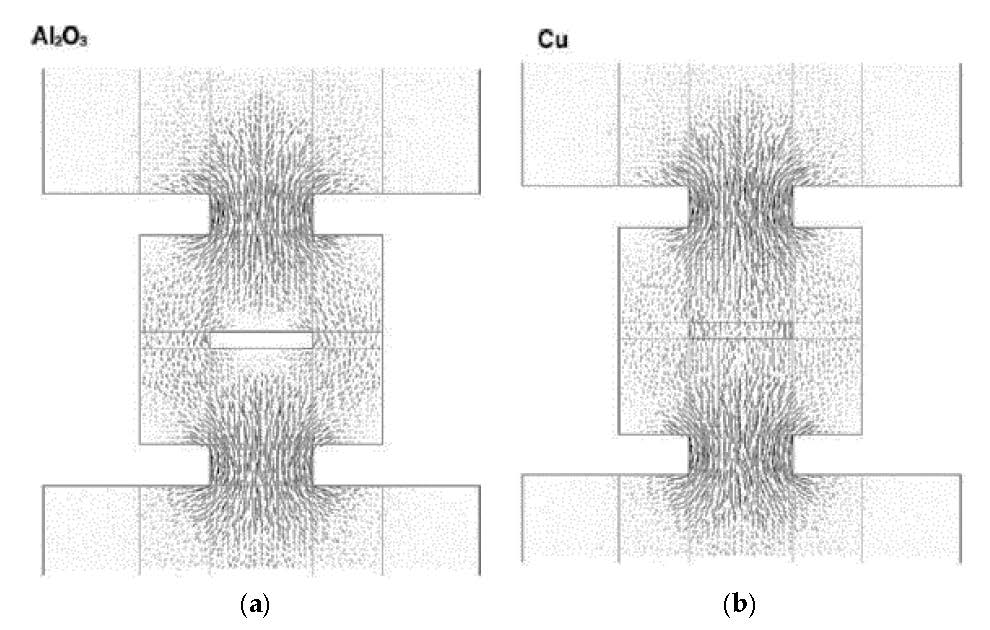
Figure 7.
The results of modelling the temperature distribution on: graphite elements with different geometries and electrical properties (a,b); a specimen with a diameter of D = 200 mm made of cemented carbide (c,d); standard graphite elements (a,c) and graphite elements after shape optimisation (b,d)—heating rate, 100 °C/min and maximum temperature, 2100 °C (Kessel 2009)
Figure 7.
The results of modelling the temperature distribution on: graphite elements with different geometries and electrical properties (a,b); a specimen with a diameter of D = 200 mm made of cemented carbide (c,d); standard graphite elements (a,c) and graphite elements after shape optimisation (b,d)—heating rate, 100 °C/min and maximum temperature, 2100 °C (Kessel 2009)
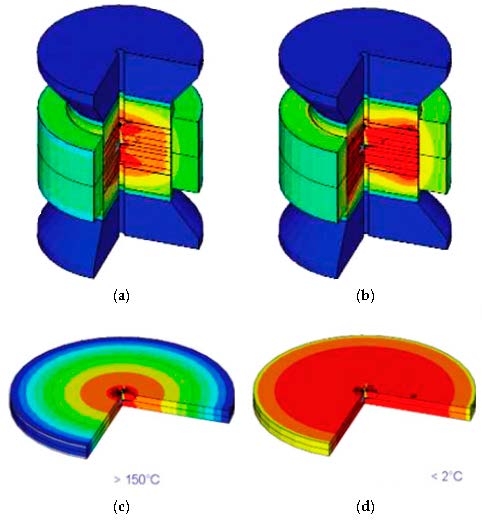
Figure 8.
Number of publications with terms SPS or spark plasma sintering in the title, according to the Web of Science database (as of 25 November 2020) (Web of Science n.d.).
Figure 8.
Number of publications with terms SPS or spark plasma sintering in the title, according to the Web of Science database (as of 25 November 2020) (Web of Science n.d.).
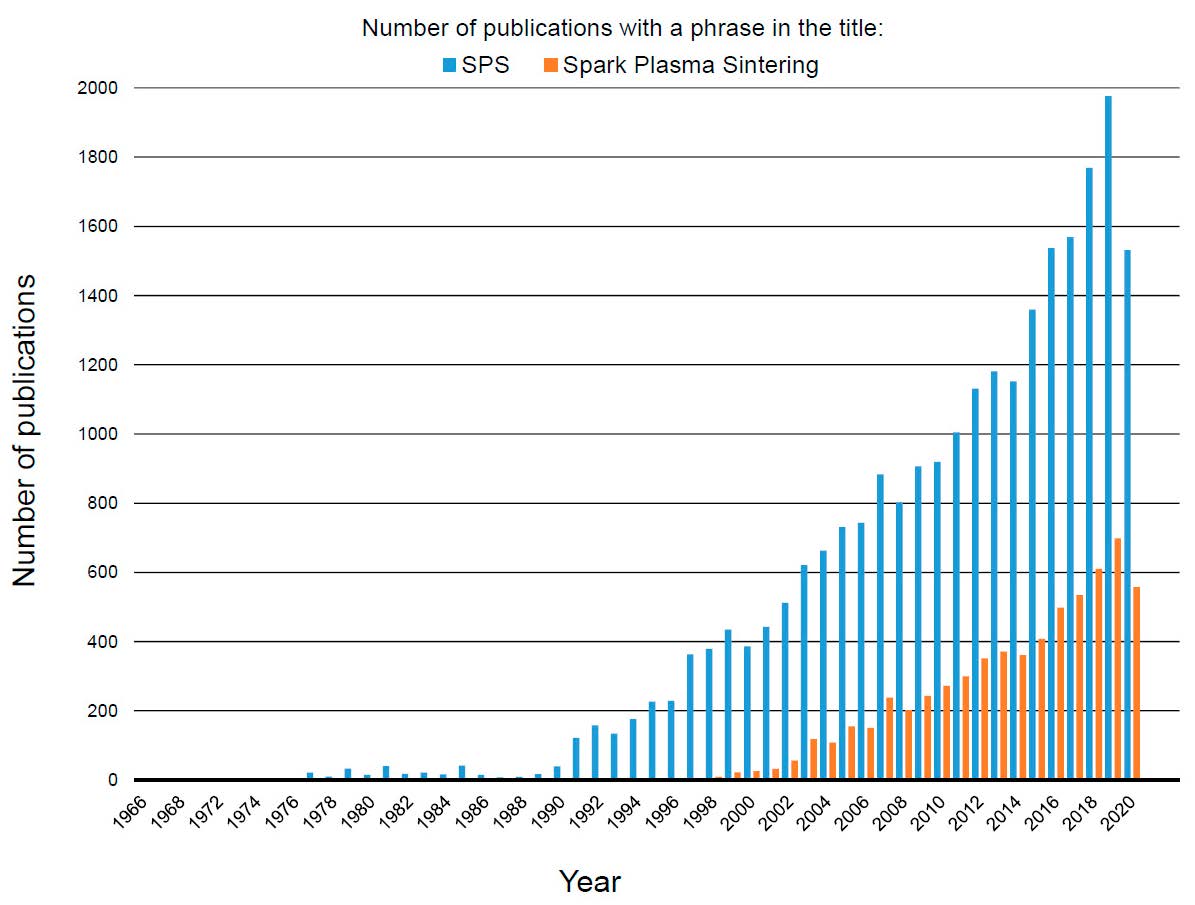
Figure 9.
Differences in the manner of heating materials in the Plasma Assisted Sintering (PAS) (a) and SPS (b) methods (Ertug 2013)
Figure 9.
Differences in the manner of heating materials in the Plasma Assisted Sintering (PAS) (a) and SPS (b) methods (Ertug 2013)
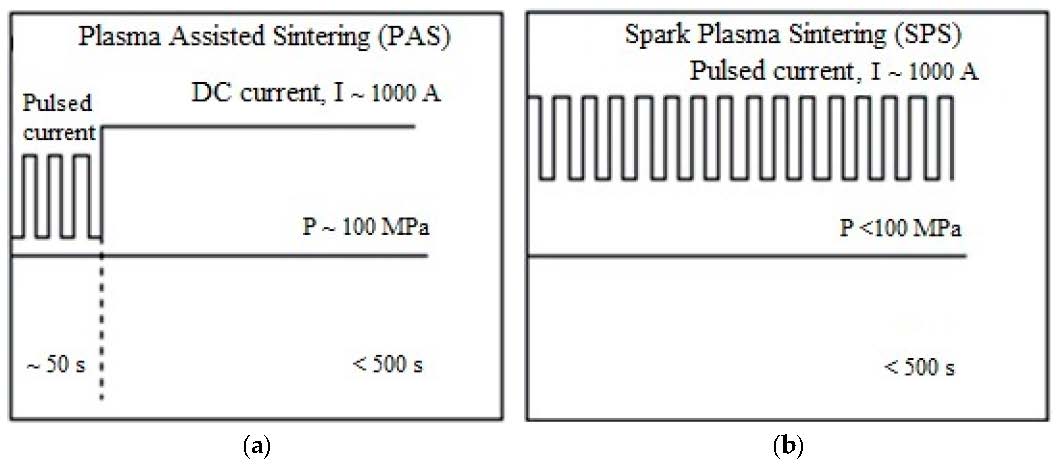
Figure 10.
Impulse heating during sintering by SPS method with the use of devices from FCT GmbH (Ertug 2013)
Figure 10.
Impulse heating during sintering by SPS method with the use of devices from FCT GmbH (Ertug 2013)
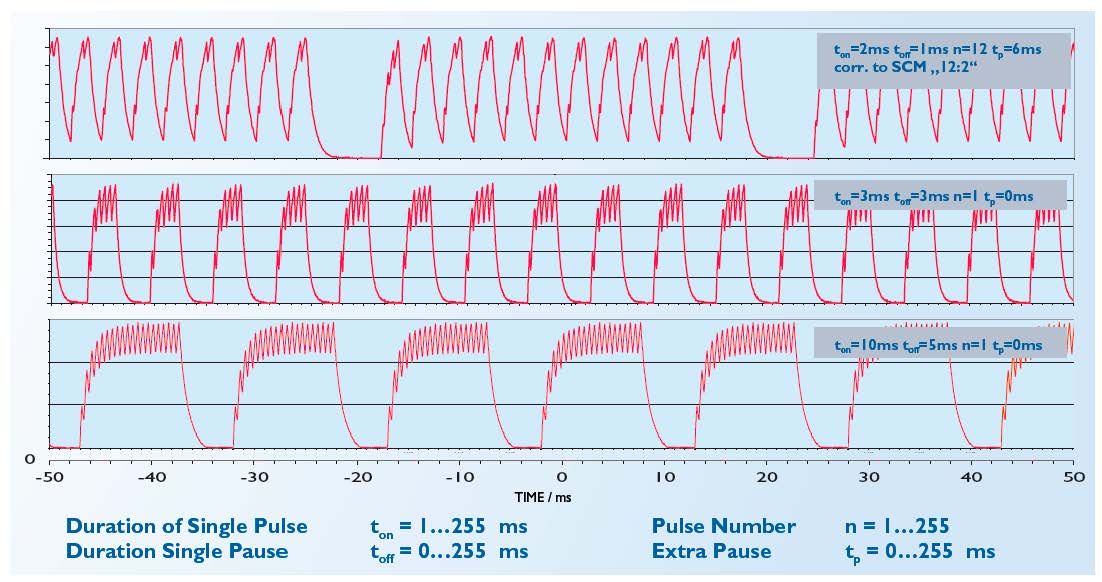
Figure 11.
SPS device scheme
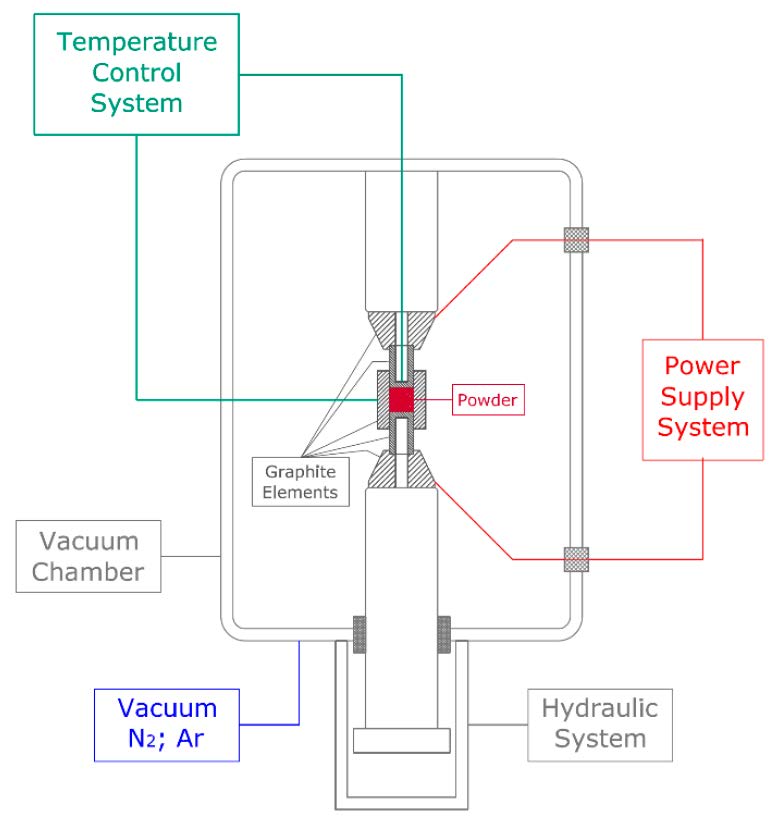
Figure 12.
SPS sintering device, type HP D5 by FCT (a); sintering chamber (b); components of the sintering die (c)
Figure 12.
SPS sintering device, type HP D5 by FCT (a); sintering chamber (b); components of the sintering die (c)
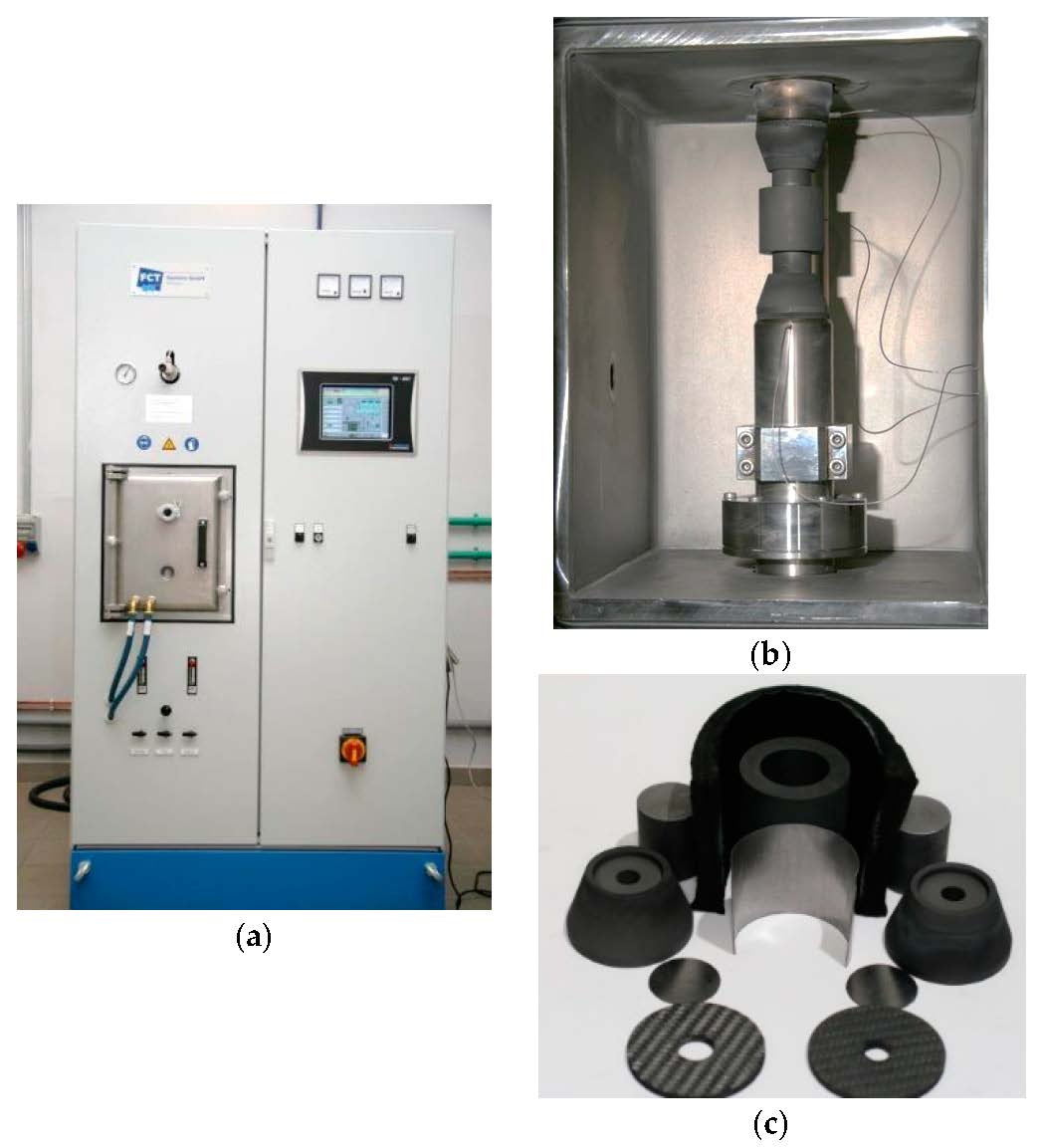
Figure 13.
The influence of the pyrometer location on the temperature difference between the sample and the place of measurement. Test conditions: TiN material, relative density 97%, sample dimensions ϕ50 × 10 mm and sample temperature 1500 °C [FCT GmbH advertising materials]
Figure 13.
The influence of the pyrometer location on the temperature difference between the sample and the place of measurement. Test conditions: TiN material, relative density 97%, sample dimensions ϕ50 × 10 mm and sample temperature 1500 °C [FCT GmbH advertising materials]
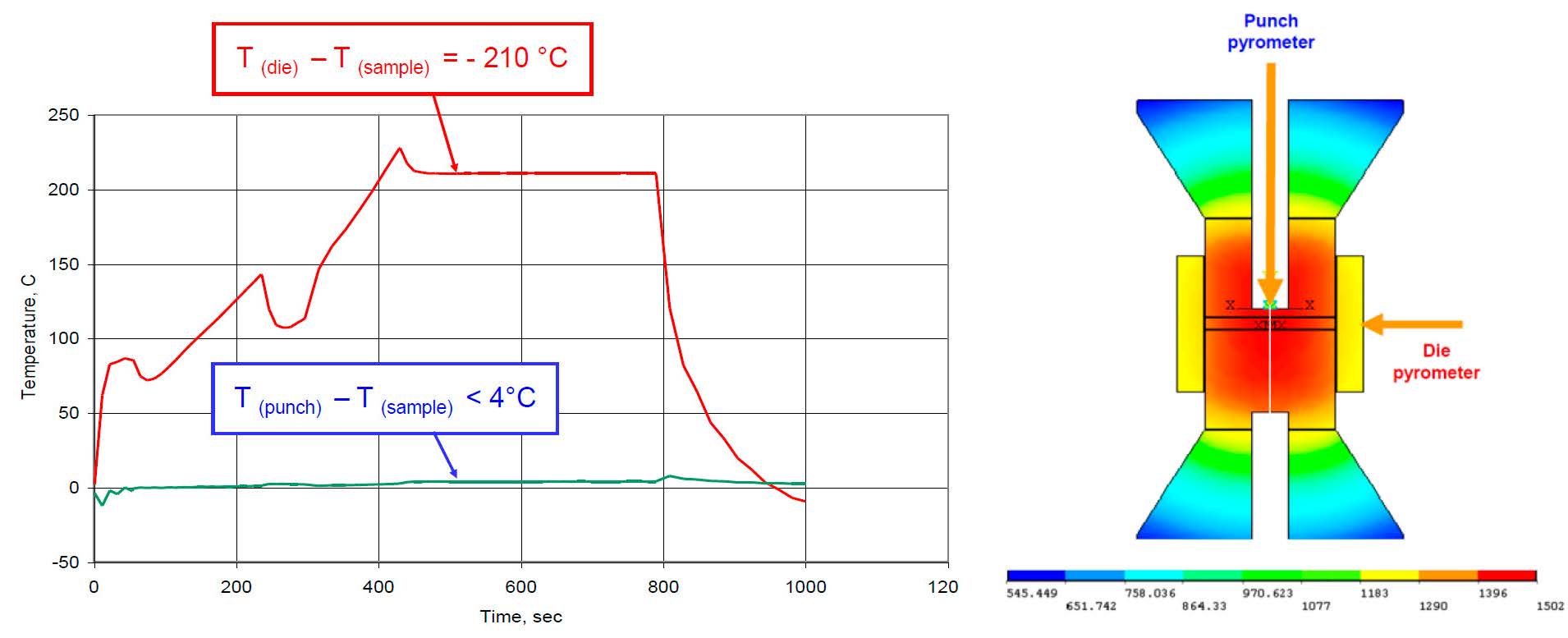
Figure 14.
Example of Field Assisted Sintering Technology (FAST)/SPS sintering curves
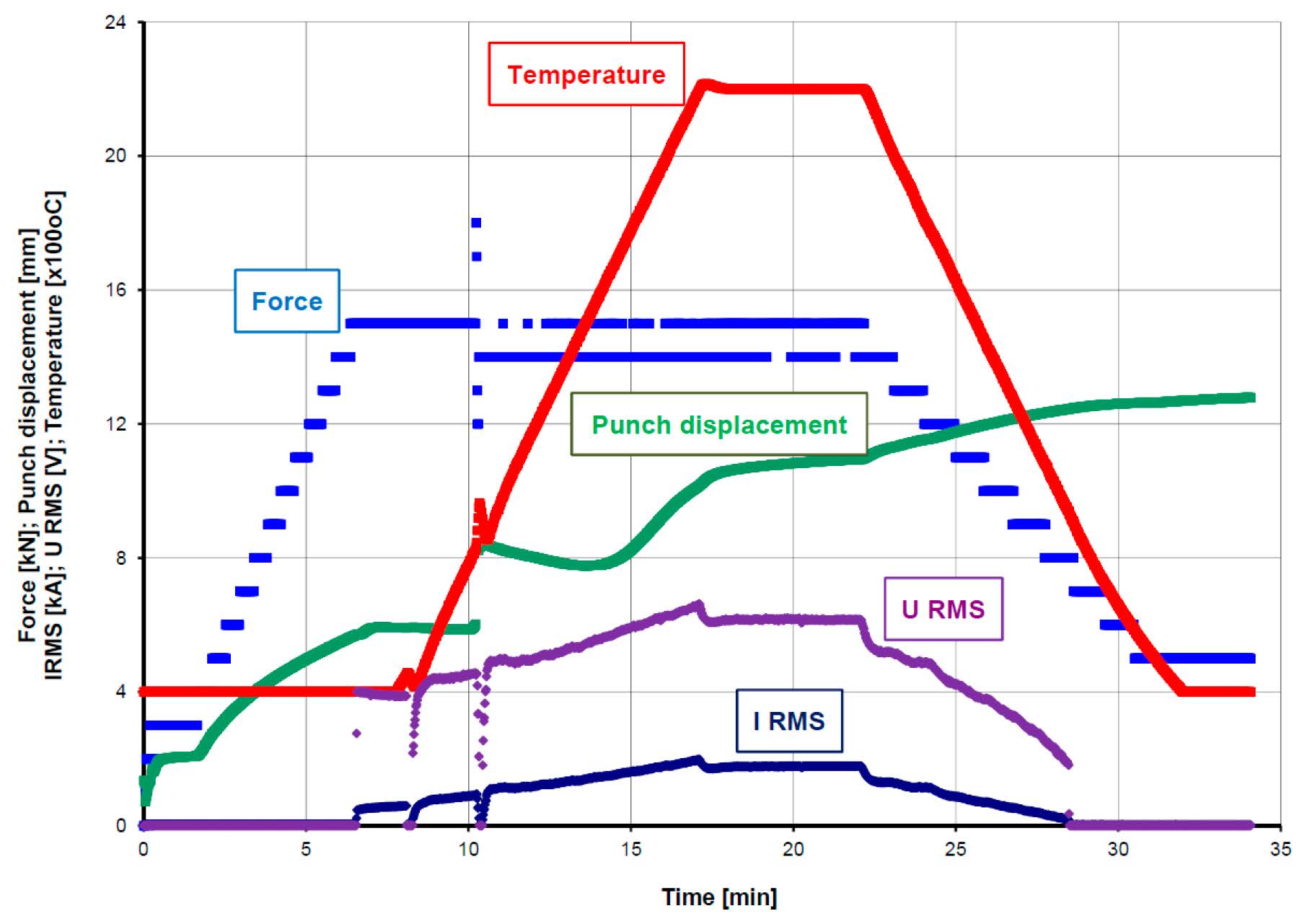
Figure 15.
Example of sample shrinkage during FAST/SPS process
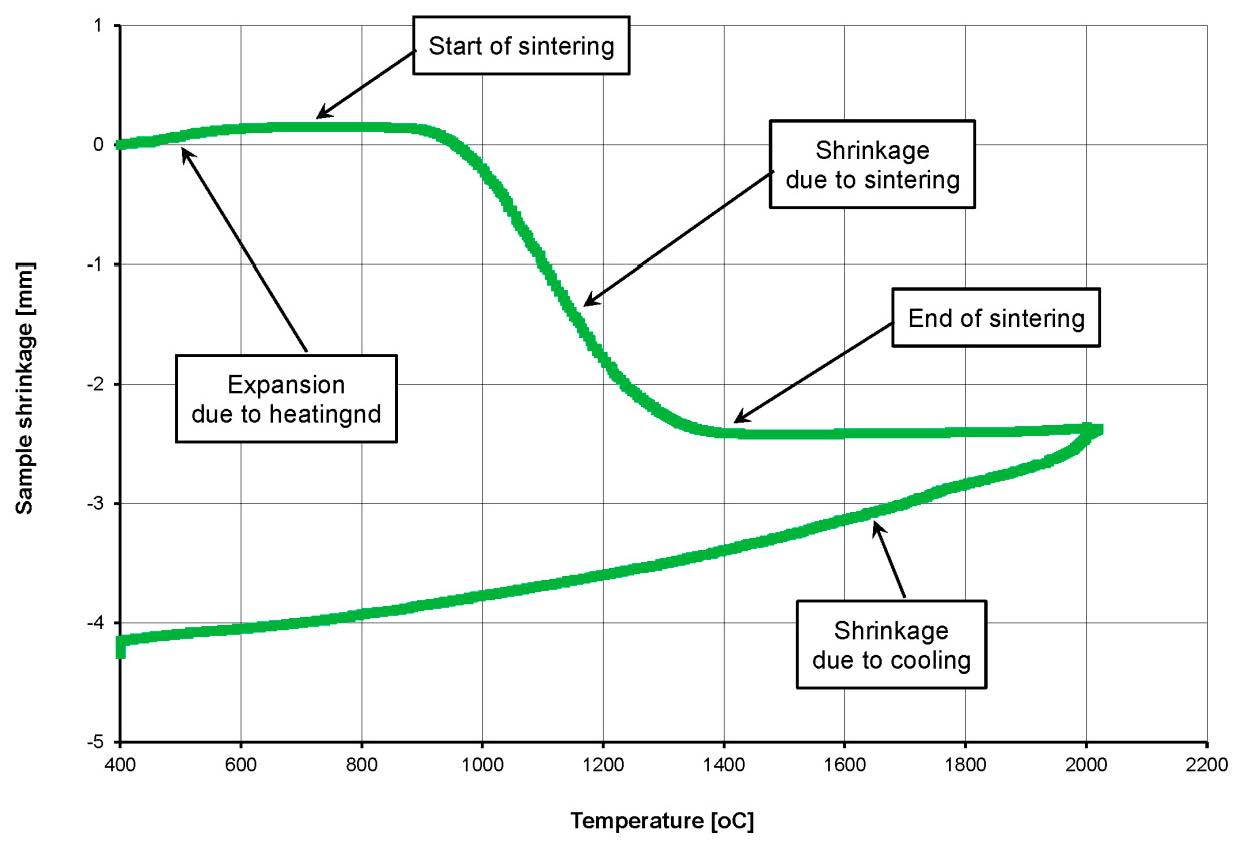
Figure 16.
Flash SPS configurations: (a) die isolated from punches; (b) die-less sintering; (c) sintering with sacrificial material (Biesuz et al. 2020)
Figure 16.
Flash SPS configurations: (a) die isolated from punches; (b) die-less sintering; (c) sintering with sacrificial material (Biesuz et al. 2020)
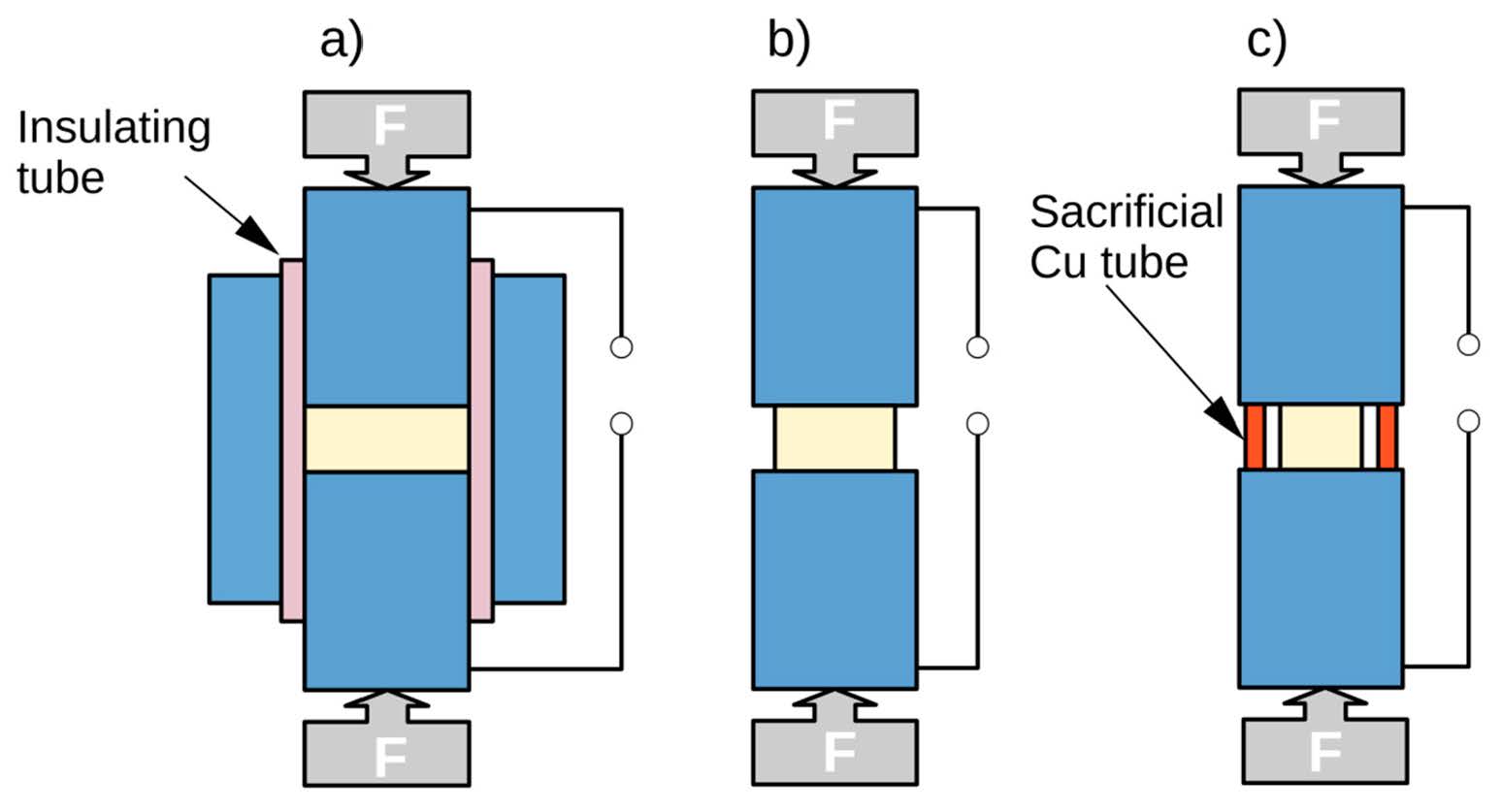
© 2021 Open Access. This article is distributed under the terms of the Creative Commons Attribution-ShareAlike 3.0 (CC BY-SA 3.0).