J_Appl_Mater_Eng 2020, 60(1), 11-20; doi:10.35995/jame60010002
Machining of Aluminums Alloys with the Addition of Reinforced Carbide Phase
1
Łukasiewicz Research Network—The Institute of Advanced Manufacturing Technology, Wrocławska 37a, 30-011 Krakow, Poland; marcin.podsiadlo@ios.krakow.pl (M.P.); lucyna.jaworska@ios.krakow.pl (L.J.); jolanta.laszkiewicz@ios.krakow.pl (J.L.-Ł); kazimierz.czechowski@ios.krakow.pl (K.C.); tadeusz.krzywda@ios.krakow.pl (T.K.)
2
Faculty of Materials Engineering and Metallurgy, Silesian University of Technology, Krasińskiego 8, 40-019 Katowice, Poland; maciej.dyzia@polsl.pl
*
Corresponding author: piotr.putyra@ios.krakow.pl
How to cite: Putyra, P.; Podsiadło, M.; Jaworska, L.; Laszkiewicz-Łukasik, J.; Dyzia, M.; Czechowski, K.; Krzywda, T. Machining of Aluminums Alloys with the Addition of Reinforced Carbide Phase. J. Appl. Mater. Eng. 2020, 60(1), 12–22, doi:10.35995/jame60010002.
Received: 31 January 2020 / Accepted: 25 May 2020 / Published: 31 May 2020
Abstract
:This paper presents the results of the processes of treating aluminum matrix casting materials with the addition of a ceramic phase. The matrix of the composite material was an Al-Si7 casting alloy with addition of 2 mass% Mg. The volume fraction of the reinforcing phase in the form of silicon carbide ranged from 5 to 15 vol.%. Preliminary machining tests were carried out at the Mori Seiki NL2000SY turning and milling center. The cutting properties were evaluated during longitudinal turning. Cutting tests were carried out using tools made of polycrystalline diamond, regular boron nitride, and cemented carbides. The nature of VBB wear was checked in accordance with PN-ISO 3685:1996. The influence of machining parameters (cutting speed, feed, cutting depth) on the value of cutting tools temperature was determined. An analysis of the chip shaping mechanism during machining was performed at various cutting parameters. The tests were carried out using the FLIR A655 thermal imaging camera and the fast Phantom MIRO M310 fast camera. Cast composite materials were also subjected to the processes of waterjet cutting, EDM cutting, and EDM drilling (EDM electro discharge machining).
Keywords:
composite cast materials; silicon carbide; cutting process; PCD insert1. Introduction
Metal matrix materials reinforced with ceramic phases belong to the group of materials that, due to their properties, are increasingly being used in modern engineering structures (Bhandare and Sonawane 2013; Bharath et al. 2014). This strengthening increases the strength, hardness, stiffness, and abrasion resistance of composite materials. Carbides, oxides, nitrides, borides, and others are used as strengthening particles (Dyzia and Śleziona 2008; Wieczorek et al. 2010; Srinivasu et al. 2015). Aluminum matrix composites reinforced with ceramic particles (e.g., Al2O3, SiC) are gradually implemented for production in the automotive, electronics, and aviation industries, mainly due to their high wear resistance in friction conditions. Composite components operating under high friction loads, such as pistons, drums, and brake discs, are manufactured on an industrial scale (Prasad and Asthana 2004). The main technologies for producing these materials are based on the methods of powder metallurgy, infiltration of porous ceramic preforms, pressure casting, or liquid pressing (Potoczek et al. 2009; O’Donnell and Looney 2001). Obtaining materials with increased mechanical properties requires the use of in situ reinforcement, which is thermodynamically stable, has less tendency to cracking and, due to the lack of intermediate layers, is well connected to the matrix (Fraś et al. 2002; Meena et al. 2013). One of the main advantages of composites is the possibility of obtaining appropriate material properties by shaping its structure in the technological process. The selection of both the matrix material, as well as the type, size, and volume share of reinforcing phases, as well as the selection of technological parameters allows obtaining materials with properties exceeding the properties of unreinforced matrix material (Dyzia et al. 2015). However, production costs, and above all, machining costs, are indicated as significant limitations in the wider implementation of composites (Mikkola and Willson 2014). These materials, due to the content of the hard ceramic phase, belong to difficult-to-cut materials and require the use of special technologies and tools in forming processes (Kathiresan and Sornakumar 2010; Sornakumar and Kathiresan 2010; Putyra et al. 2014; Putyra et al. 2015). In the case of cemented carbide tools, intensive wear of cutting edges and a problem with ensuring dimensional stability within the tolerance provided for a given machining operation are observed. The machining of cast composite materials reinforced with ceramic phases is referred to as intermittent machining, characterized by dynamic impacts exerted on the cutting tool. Due to the degree of material consumption during the machining of cast composite materials, an important aspect is the development of an economically viable shaping method, ranging from cutting off sprues and the flooding system, through turning or drilling of holes. Machining new materials requires the involvement of various methods and a very comprehensive approach to the shaping process.
2. Materials and Methods
The subject of the research was a metal composite with an aluminum alloy matrix with the addition of 7% silicon and the addition of reinforcing ceramic phase SiC in amounts of 5%, 10%, or 15%. The detailed chemical composition of the base matrix alloy is shown in Table 1. This material was obtained as part of industrial research at Złotecki Sp. z o.o. company. Silicon carbide powder (prod. SIKA ABR P, Saint Gobain) with a grain size of 40.5 μm was used as the reinforcing phase. The AlSi7 base matrix alloy was melted at 720 °C, then refined with argon for an hour and, after this, mortars containing Mg and Sr were added. Ceramic particles SiC, after initial annealing, were fed onto a mirror of a rotating metal. The homogenization and degassing processes of the suspension were carried out under reduced argon pressure. The materials were cast into die forms. The semi-finished products intended for further testing had the shape of rollers (diameter Ø = 85 mm and length l = 120 mm) or pistons (diameter Ø = 68 mm and length l = 54 mm).
The following shaping methods were selected for treatment composite materials with the addition of the SiC reinforcing phase: machining, electroerosive cutting technology, abrasive waterjet cutting, and electroerosive drilling. The main criterion for evaluating the effectiveness of individual cutting or drilling techniques was their duration. In the case of machining, tool durability was determined, while for processes using EDM or abrasive blasting, the surface roughness of the elements after machining was also determined in addition to the duration of the process. A diagram of processes for shaping elements with the addition of SiC particles is shown in Figure 1.
The cutting off of the flooding system and sprues of AlSiMg composite materials with the addition of silicon carbide was carried out using high-pressure abrasive waterjet and electro-discharge technology. The risers were cut off using a FORACON WS520/15/2.4Z abrasive waterjet machining device, with a working pressure of 380 MPa, equipped with a Paser 2 cutting head, 0.3 mm diameter water nozzle, and 1.0 mm diameter mixing nozzle.
For electroerosive cutting off sprues, a EWEA 40CNC (prod. Institute of Advanced Manufacturing Technology) cutter was used with the possibility of setting the pulse duration in the range from 0.1 to 3 µs and break time from 5 to 330 µs at 150 V. Copper wire (diameter 0.25 mm) with an increased content of zinc was used.
The sample surfaces after cutting with abrasive blasting and electro-discharge cutting were subjected to measurements of surface roughness and waviness profiles. The measurements were carried out using the TOPO 01 system developed and manufactured at the Institute of Advanced Manufacturing Technology.
To make lubrication holes in the piston grooves, electroerosion drill technology was used as an alternative drilling technology. The drilling process was carried out on an EDEA 16CNC machine with adjustable settings of pulse duration in the range from 4 to 2500 µs and break time from 5 to 2500 µs at 160 V. The holes were made using electrodes with diameters of 1 to 3 mm.
The materials, after cutting off the nobs, were subjected to longitudinal turning tests using tools made of polycrystalline diamond (PCD), polycrystalline regular boron nitride (PCBN), and sintered carbides (WC–Co). The durability of PCD tools was determined using the NL2000SY type turning and milling center (from Mori Seiki). The nature of the wear and its size on the flank face were checked (VBB max and VBC parameters). The working time was adopted as the limiting value of tool life, after which the VBB or VBC wear parameter reaches 0.3 mm.
The influence of cutting parameters (speed, feed, and cutting depth) on the value of cutting edges temperature was also determined. The tests were carried out on a TUR50 lathe additionally equipped with a FLIR A655 thermal imaging camera and a Phantom MIRO 310 quick camera. During the cutting tests, the following parameters were chosen: thermal imaging camera parameters (e.g., emissivity of individual materials, transmission value, and external optical system parameters), fast camera parameters (resolution, sampling rate, exposure time) as well as the type of light and lighting method. In the analysis using a thermal imaging camera, it was assumed that as a result of friction of the processed material against the surface of the cutting tool, these elements heat up to the same temperature. The temperature distribution tests were preceded by the system calibration stage and determination of the emissivity factor of the aluminum matrix material with the addition of the SiC phase. An analysis of the chip shaping mechanism during machining was carried out at various cutting parameters as well as microscopic analysis of the flank and rake face of the tool inserts after machining. Analyses were performed using a JEOL JSM 6460LV scanning electron microscope (SEM). Machining was carried out using cutting inserts with polycrystalline diamond (PCD) tools intended for finishing high-speed aluminum alloys, tools of regular boron nitride, and WC–Co sintered carbide. Cutting tools with the following markings were used:
- −
- Polycrystalline diamond PCD (NP-DCMT 11T304 L-F MD220, NP-DCMW 11T304 MD220),
- −
- Polycrystalline boron nitride PCBN (NP-DCGW11T304GS2 MB710, NP-DCGW11T304GS2 MB8025, NP-DCGW11T304GS2 MB4020, GY1G03300F020NGFGS MB8025),
- −
- Tungsten carbide WC–Co (SCGX 09 T3 08-Al H10, CCGX 09 T3 04-Al H10).
The following longitudinal turning parameters were used in testing tool life:
- −
- cutting speed—vc = 100, 200, 300, and 500 m/min;
- −
- feed—f = 0.10, 0.20, and 0.30 mm/rev;
- −
- cutting depth—ap = 0.5, 1.0, 1.5, and 2.0 mm.
Temperature analysis and chip formation mechanism were performed during longitudinal turning with the following parameters:
- −
- cutting speed—vc = 50, 75, 100, and 120 m/min,
- −
- feed—f = 0.08, 0.17, and 0.34 mm/rev
- −
- cutting depth—ap = 0.5, 1.0, and 2.0 mm.
3. Results
For the processing of composite materials with the addition of the SiC reinforcing phase, electroerosion cutting, abrasive waterjet cutting, and electroerosion drilling technology were selected. The main criterion for assessing the effectiveness of individual cutting or drilling techniques was their duration. In the case of cutting off the nod, the most effective was cutting with abrasive waterjet. Regardless of the volume share of the SiC phase in the castings, the total time of cutting off the elements of the system was 10 min, with the majority of time needed to properly fasten the casting. Due to the design and shape of the cutting nozzle, it is not possible to cut off the sprue at the very bottom of the piston. The nod is cut off at a height of 3 to 5 mm above the piston crown. When using electroerosion technology, the cut-off of the nod depending on the parameters used can reach up to 120 min. Table 2 shows the duration of electro-discharge cutting of materials depending on the content of the SiC carbide phase. Shafts with a diameter of 63 mm were cut, with 5 processes performed for each material. Materials with SiC phase content of 5% and 10% after cutting with an abrasive stream and using EDM are shown in Figure 2.
After the process of cutting with waterjet and electroerosion, surface roughness measurements were made. The materials AlSi–Mg–Sr + 5% SiC and AlSi–Mg–Sr + 10% SiC were selected for the research. The measurement results are included in Table 3 and graphically presented in Figure 3 and Figure 4.
For making lubrication holes in the piston grooves, electroerosion drilling technology was used as an alternative to drilling technology. The drilling process was carried out on a MEDIOS machine tool with a UZSD 40CNC generator, using electrodes with a diameter of 1 to 3 mm. The drilling duration for a piston made of an AlSi–Mg–Sr casting alloy with the addition of 10% SiC electrodes with diameters of 1 and 2.5 mm was 1 min. Another advantage of this technology is the fact that holes after drilling do not require deburring. When using drilling technology, the amount of dimensionally compatible pistons does not exceed 60%. Workpiece damage in the drilling process occurs as a result of broken drills and hole broaching. The results of electroerosion drilling of AlSi–Mg–Sr material with the addition of 10% SiC are shown in Figure 5.
The results of the cutting tests depending on the amount of ceramic phase in the AlSi–Mg–Sr matrix, machining parameters, and tool material are presented in Table 4, Table 5 and Table 6. Tool life was determined as the time until VBB build-up or abrasion of 0.3 mm. During cutting, a large amount of heat is generated as a result of friction between the surface of the cutting tool and the chip. The temperature resulting from friction was measured, on the basis of the chip temperature, above the cutting tool. In order to correctly register temperature changes, the appropriate parameters of the measured object were selected. Based on calibration tests, the value of the emissivity coefficient for the AlSi–Mg–Sr material with the addition of SiC of 0.85. The results of temperature measurement of cutting tool made of polycrystalline diamond, during longitudinal turning of the composite material AlSi–Mg–Sr–SiC, are presented in graphic form in Figure 6.
An example of the temperature distribution during machining with a polycrystalline diamond insert and the image recorded by the FLIR thermal imaging camera as well as the image recorded by the Phantom fast camera are shown in Figure 7. Tools made of polycrystalline diamond and tungsten carbide after turning AlSi–Mg–Sr with the addition of SiC, with a visible build-up edge and abrasion of the flank face and tool face are shown in Figure 8 and Figure 9, respectively.
4. Discussion
Due to the content of the hard SiC reinforcing phase in the composites, high-pressure abrasive waterjet cutting and electroerosion machining were used to cut off the nob, and in case of making the hole, machining with PCD, PCBN, WC–Co tools, and electroerosive drilling were used. In the case of cutting off the nobs, the most effective method was cutting with abrasive waterjet. Regardless of the volumetric content of the SiC phase in the castings, the total time of cutting off the elements was 10 min, with the majority of time needed to properly fasten the casting. Cutting off the nod system using electroerosion technology lasts from 1 to several hours, depending on the parameters used. In contrast to waterjet cutting, the surface of the materials after electroerosion cutting is characterized by less roughness and waviness, regardless of the carbide phase content. When drilling holes, electroerosion drilling technology was used as an alternative technology for drilling. The process was carried out using electrodes with a diameter of 1 to 3 mm. The machining time of a piston made of a casting alloy with the addition of 10% SiC with 1 and 2.5 mm electrodes was 1 min.
In the turning tests of aluminum alloy pistons with SiC particles, from the aspect of tool life, much better results were obtained for polycrystalline diamond (PCD) inserts than for inserts made of regular boron nitride and cemented carbide. Tool life decreased with increasing cutting speed and SiC content in the aluminum alloy. Higher durability was obtained for a tool providing a zero back-rake angle than for a tool for which the back-rake angle was 17°. In the tests, regardless of the type of insert used and the type of tool (PCD, regular boron nitride, cemented carbides), chips were obtained in a favorable element form. The wear of polycrystalline diamond and regular boron nitride tool inserts resulted from build-up, while wear of cemented carbide tools was due to intensive abrasion.
The stage of chip formation as a result of turning with PCD diamond tools was also registered with the use of the Phantom MIRO 310 high-speed camera. During turning with all tested inserts, regardless of the cutting parameters used, chips were obtained in a favorable element or spiral form, with the chip length not exceeding a dozen or so millimeters. Depending on the machining parameters used (cutting speed, feed, cutting depth), chip breaking occurred as a result of contact with the face of the workpiece (at low feed rates), the side surface of the workpiece, the tool face (at the lowest cutting speed, feed, and cutting depth parameters) or a flank face (at high cutting speeds, regardless of feed rate and depth of cut).
The durability of diamond tools during machining of aluminum matrix material with the addition of 10% SiC at a speed of 500 m/min, regardless of the feeds and depth of cut, did not exceed 10 min. Along with the reduction of cutting speed to the level of 300 m/min, an increase in the tool life of up to 15 min was found. The tool life of polycrystalline diamond tools when turning AlSi–Mg–Sr with 5% SiC at 300 m/min exceeded 80 min. Analysis of the temperature distribution using the FLIR A655 thermal imaging camera showed that the cutting speed of the workpiece has the greatest impact on the amount of heat generated during the cutting process and the temperature value. Subsequently, the depth of cut and feed affect the temperature of the workpiece.
Author Contributions
Machining conceptualization of aluminum alloys, P.P.; Investigation, cutting tests with using of thermo and HS cameras, M.P.; Conceptualization of research, L.J., Microstructure and SEM research, J.L.-Ł.; Development of alloys composition, M.D.; Cutting tests, K.C.; EDM-machining tests, T.K.
Funding
This research was funded by The National Centre for Research and Development from the project under the Applied Research Program: “Development of the phase composition of the composite based on AlSi alloy in terms of the possibility of shaping piston working surfaces”, KOMPCAST, No. PBS1/B6/13/2013.
Conflicts of Interest
The authors declare no conflicts of interest.
References
- Bhandare, Rajeshkumar Gangaram; Sonawane, Parshuram M. Preparation of Aluminium Matrix Composite by Using Stir Casting Method. International Journal of Engineering and Advanced Technology (IJEAT) 2013, 3, 148–55. [Google Scholar]
- Bharath, V.; Madev, Nagaral; Auradi, V; Kori, S. A. Preparation of 6061Al-Al2O3 MMC’s by Stir Casting and Evaluation of Mechanical and Wear Properties. 3rd International Conference on Materials Processing and Characterization (ICMPC 2014). Procedia Materials Science 2014, 6, 1658–67. [Google Scholar] [CrossRef]
- Dyzia, Maciej; Śleziona, Józef. Kompozyty o osnowie aluminium zbrojone dyspersyjnymi fazami azotkowymi. Kompozyty 2008, 8, 269–73. [Google Scholar]
- Dyzia, Maciej; Dolata, Anna J.; Putyra, Piotr; Jaworska, Lucyna. Dobór składu fazowego kompozytu na bazie stopu AlSi pod kątem możliwości kształtowania powierzchni roboczych tłoków. Inżynieria Materiałowa 2015, 6, 519–23. [Google Scholar] [CrossRef]
- Fraś, Edward; Kolbus, Andrzej; Janas, Andrzej. Porównanie niektórych właściwości mechanicznych kompozytów ex situ typu Duralcan z kompozytami in situ typu Al-TiC. Kompozyty (Composites) 2002, 2, 176–79. [Google Scholar]
- Kathiresan, M.; Sornakumar, T. EDM Studies on Aluminum Alloy-Silicon Carbide Composites Developed by Vortex Technique and Pressure Die Casting. Journal of Minerals & Materials Characterization & Engineering 2010, 9, 79–88. [Google Scholar]
- Meena, K. L.; Manna, A.; Banwait, S. S.; Jaswanti. An Analysis of Mechanical Properties of the Developed Al/SiC-MMC’s. American Journal of Mechanical Engineering 2013, 1, 14–19. [Google Scholar] [CrossRef]
- Mikkola, Paul; Willson, Bruce. Investment casting metal matrix composites. Metal Casting Design & Purchasing 2014, November/December, 31–35. [Google Scholar]
- O’Donnell, G.; Looney, L. Production of aluminium matrix composites components using conventional PM technology. Materials Science and Engineering A 2001, 303, 292–301. [Google Scholar] [CrossRef]
- Potoczek, Marek; Śliwa, Robert; Myalski, Jerzy; Śleziona, Józef. Kompozyty metalowo-ceramiczne wytwarzane przez infiltrację ciśnieniową metalu do ceramicznej preformy o budowie piany. Rudy i Metale Nieżelazne 2009, 54, 688–92. [Google Scholar]
- Prasad, S. V.; Asthana, Rajiv. Aluminum metal–matrix composites for automotive applications: Tribological considerations. Tribology Letters 2004, 17, 445–53. [Google Scholar] [CrossRef]
- Putyra, P.; Wojteczko, K.; Dyzia, Maciej; Czechowski, K.; Jaworska, L.; Dolata-Grosz, Anna. Metody kształtowania odlewniczych materiałów kompozytowych. Mechanik 2014, 8–9, 634–36. [Google Scholar]
- Putyra, P.; Jaworska, L.; Dyzia, M.; Czechowski, K.; Krzywda, T. Kształtowanie siluminów z dodatkiem fazy węglikowej. Materiały konferencyjne: JAKOŚĆ I INNOWACYJNOŚĆ W PROCESACH WYTWARZANIA. Paper presented at JAKOŚĆ I INNOWACYJNOŚĆ W PROCESACH WYTWARZANIA, Wisła, Poland, September 24–26; 2015. [Google Scholar]
- Sornakumar, Thambu; Kathiresan, Marimuthu. Machining studies of die cast aluminum alloy-silicon carbide composites. International Journal of Minerals, Metallurgy and Materials 2010, 17, 648–53. [Google Scholar] [CrossRef]
- Srinivasu, R.; Rao, A. Sambasiva; Reddy, G. Madhusudhan; Rao, K. Srinivasa. Friction stir surfacing of cast A356 aluminium-silicon alloy with boron carbide and molybdenum disulphide powders. Defence Technology 2015, 11, 140–46. [Google Scholar] [CrossRef]
- Wieczorek, J.; Śleziona, J.; Dolata-Grosz, A.; Myalski, J. Struktura i właściwości kompozytów po odlewaniu ciśnieniowym. Archiwum Technologii Maszyn i Automatyzacji 2010, 30, 41–49. [Google Scholar]
Figure 1.
Scheme of treatment materials made of silumin-reinforced with SiC particles
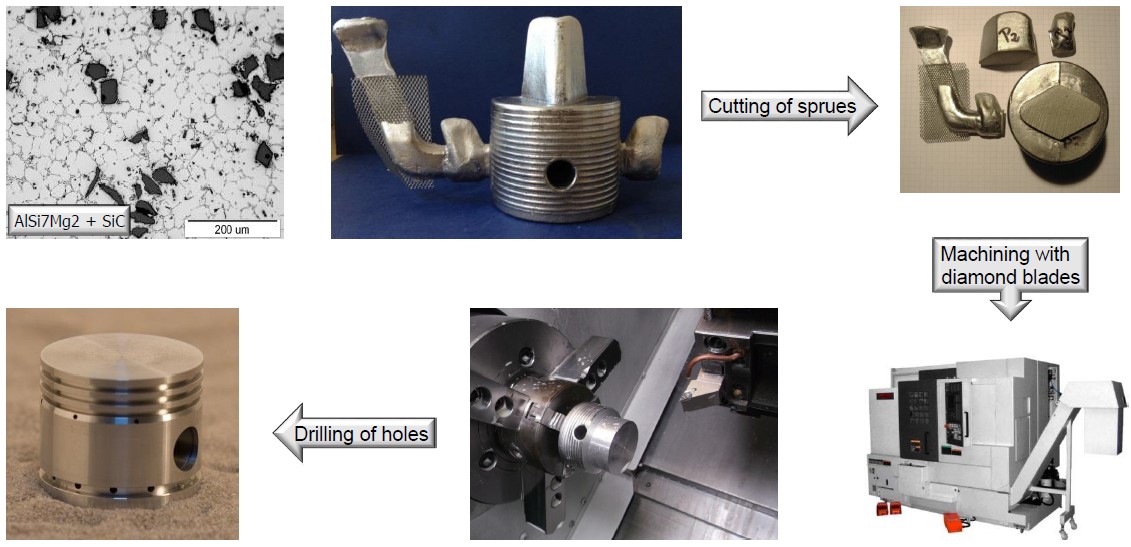
Figure 2.
Cutting off nodes of AlSi–Mg–Sr materials reinforced with a SiC carbide phase: (a) elements after cutting with waterjet; (b) elements after cutting with the EDM method
Figure 2.
Cutting off nodes of AlSi–Mg–Sr materials reinforced with a SiC carbide phase: (a) elements after cutting with waterjet; (b) elements after cutting with the EDM method
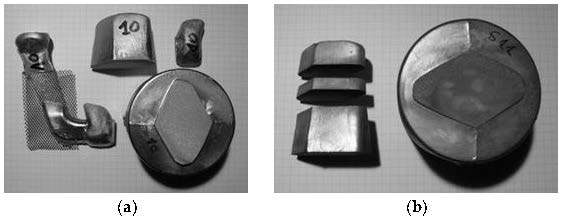
Figure 3.
Measurement of the surface roughness of the AlSi–Mg–Sr + 10 vol.% SiC after cutting with abrasive waterjet
Figure 3.
Measurement of the surface roughness of the AlSi–Mg–Sr + 10 vol.% SiC after cutting with abrasive waterjet
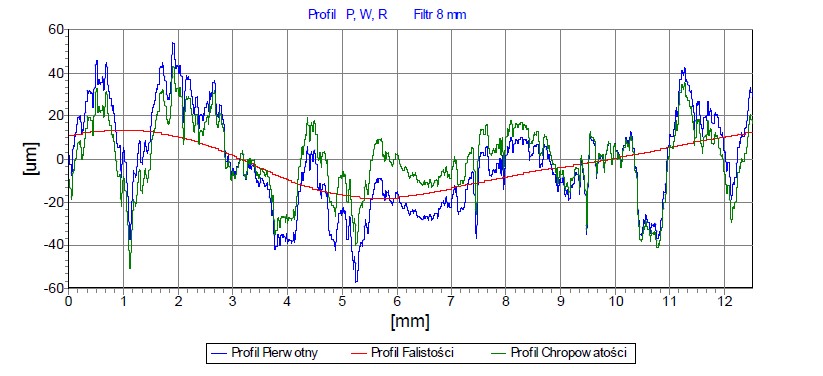
Figure 4.
Measurement of the surface roughness of the AlSi–Mg–Sr + 10 vol.% SiC after EDM cutting
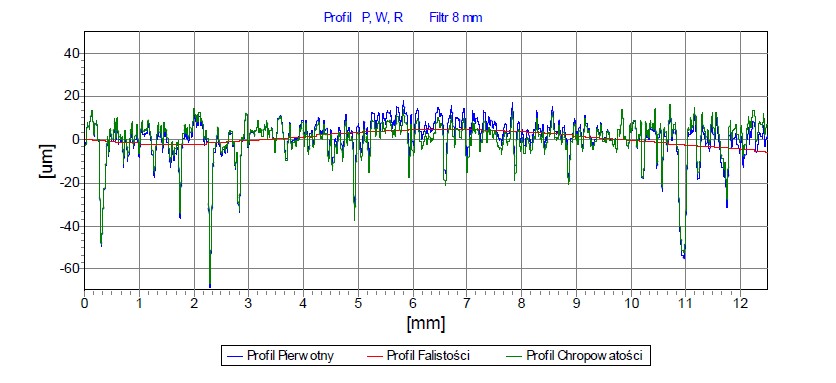
Figure 5.
Electro-discharge drilling of AlSi–Mg–Sr material with the addition of 10 vol.% SiC
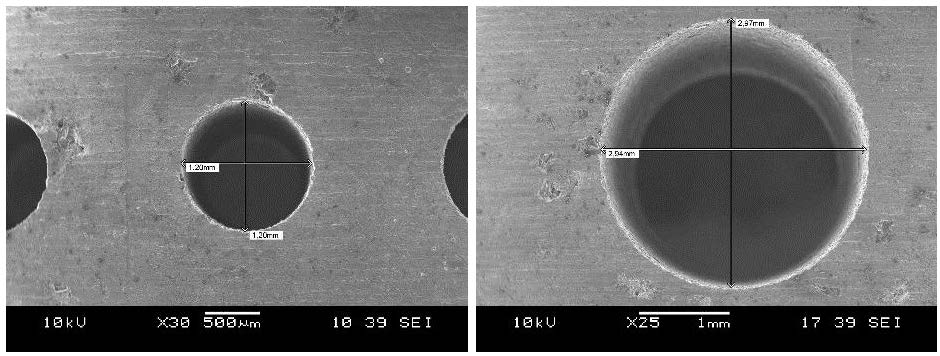
Figure 6.
Influence of cutting parameters (cutting speed, feed, cutting depth) on the temperature of a polycrystalline diamond tool
Figure 6.
Influence of cutting parameters (cutting speed, feed, cutting depth) on the temperature of a polycrystalline diamond tool
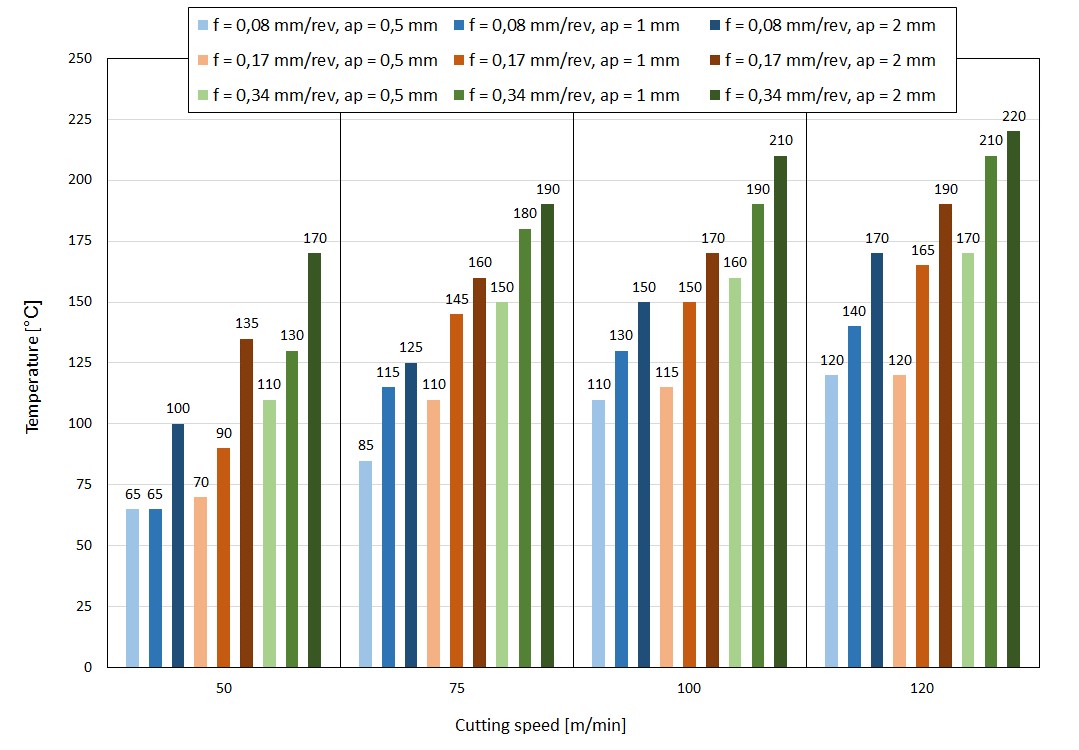
Figure 7.
Frame from measurements using a thermal imaging camera (a); temperature distribution during machining (b); chip forming mechanism (c) (for parameters: cutting speed: 45 m/min, feed: 0.34 mm/rot., cutting depth: 2.0 mm)
Figure 7.
Frame from measurements using a thermal imaging camera (a); temperature distribution during machining (b); chip forming mechanism (c) (for parameters: cutting speed: 45 m/min, feed: 0.34 mm/rot., cutting depth: 2.0 mm)
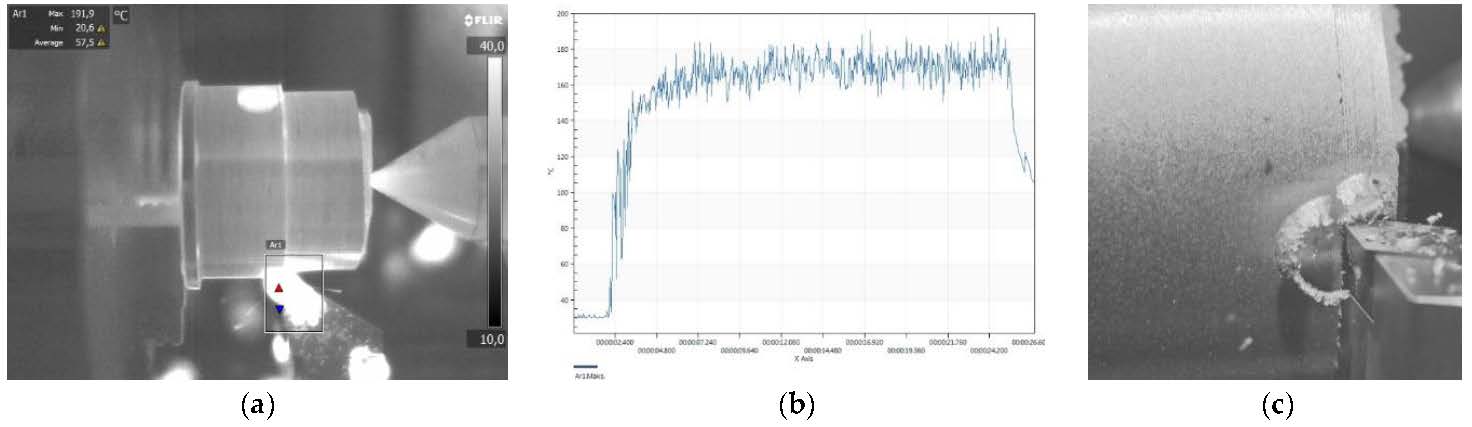
Figure 8.
Polycrystalline diamond (PCD) diamond tools after turning AlSi–Mg–Sr–SiC material (vs = 500 m/min, VB = 0.30 mm, T = 2.8 min): flank face (a); tool face (b)
Figure 8.
Polycrystalline diamond (PCD) diamond tools after turning AlSi–Mg–Sr–SiC material (vs = 500 m/min, VB = 0.30 mm, T = 2.8 min): flank face (a); tool face (b)
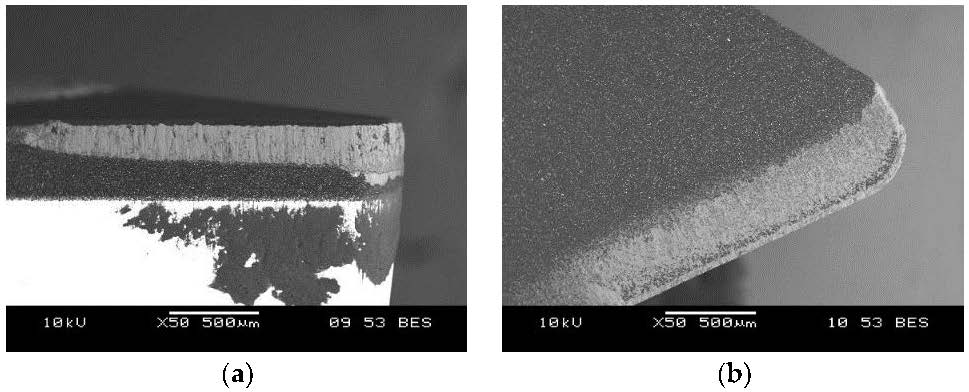
Figure 9.
Tungsten carbide tools after turning AlSi–Mg–Sr–SiC material (vs = 60 m/min, VB > 0.30 mm, T < 1 min): flank face (a), tool face (b)
Figure 9.
Tungsten carbide tools after turning AlSi–Mg–Sr–SiC material (vs = 60 m/min, VB > 0.30 mm, T < 1 min): flank face (a), tool face (b)
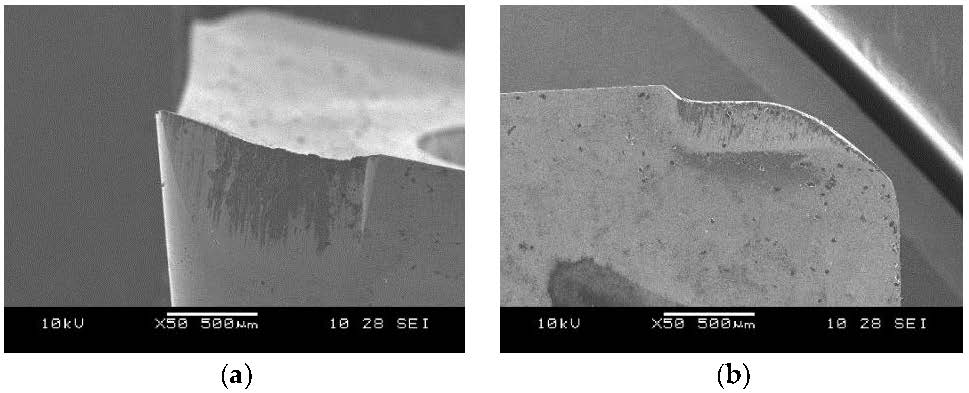
Table 1.
Chemical composition of the base casting alloy (in weight %)
Al | Si | Fe | Mg | Sr |
---|---|---|---|---|
balance | 7 | 0.5 | 2 | 0.03 |
Table 2.
Electro-discharge cutting of composite materials
Materials | Cutting duration (min) |
---|---|
AlSi–Mg–Sr + 5 vol.% SiC | 40–45 |
AlSi–Mg–Sr + 10 vol.% SiC | 100–110 |
AlSi–Mg–Sr + 15 vol.% SiC | 90–95 |
Table 3.
Results of material surface roughness measurements after cutting with waterjet and electro-discharge machining
Table 3.
Results of material surface roughness measurements after cutting with waterjet and electro-discharge machining
Materials | Treatment method | Roughness Ra (µm) |
---|---|---|
AlSi–Mg–Sr + 5 vol.% SiC | abrasive waterjet | 16.2 |
electroerosion | 5.4 | |
AlSi–Mg–Sr + 10 vol.% SiC | abrasive waterjet | 15.5 |
electroerosion | 9.9 |
Table 4.
Polycrystalline diamond insert durability during longitudinal turning of the composites, depending on the SiC phase content and used cutting speeds
Table 4.
Polycrystalline diamond insert durability during longitudinal turning of the composites, depending on the SiC phase content and used cutting speeds
Materials | v (m/min) | VB (mm) | T (min) |
---|---|---|---|
AlSi7Mg2 + Sr + 5 vol.% SiC | 100 | 0.13 | 25.0 |
300 | 0.13 | 13.7 | |
0.30 | 82.0 | ||
500 | 0.30 | 17.0 | |
AlSi7Mg2 + Sr + 10 vol.% SiC | 300 | 0.19 | 6.8–14.7 |
500 | 0.30 | 2.8–9.1 | |
AlSi7Mg2 + Sr | 500 | 0.07 | 40.5 |
Table 5.
Durability of polycrystalline diamond inserts during longitudinal turning of the AK7–10 vol.% SiC composite
Table 5.
Durability of polycrystalline diamond inserts during longitudinal turning of the AK7–10 vol.% SiC composite
Machining parameters | Tool life | ||
---|---|---|---|
Cutting speed | Feed | Cut depth | |
vc (m/min) | f (mm/obr) | ap (mm) | T (min) |
200 | 0.15 | 1.5 | 12.3 |
300 | 0.10 | 0.5 | 14.7 |
0.10 | 1.0 | 9.5 | |
0.20 | 1.0 | 12.5 | |
0.30 | 1.0 | 8.2 | |
500 | 0.10 | 0.5 | 2.5 |
0.10 | 1.0 | 1.7 | |
0.20 | 1.0 | 0.7 | |
0.20 | 2.0 | 0.5 | |
0.30 | 1.0 | 0.5 |
Table 6.
Durability of polycrystalline diamond, regular boron nitride and cemented carbide inserts during longitudinal turning of the AK7–10 vol.% SiC composite
Table 6.
Durability of polycrystalline diamond, regular boron nitride and cemented carbide inserts during longitudinal turning of the AK7–10 vol.% SiC composite
Materials | v (m/min) | VB (mm) | T (min) |
---|---|---|---|
PCD | 300 | 0.30 | 6.8–14.7 |
500 | 2.8–9.1 | ||
PCBN | 100 | 0.30 | 1.2–4.7 |
300 | 0.7–1.1 | ||
WC–Co | 60–100 | 0.7–1 | <1 |
© 2020 Open Access. This article is distributed under the terms of the Creative Commons Attribution-ShareAlike 3.0 (CC BY-SA 3.0).